Voith e Huntsman Advanced Materials hanno stretto una partnership per soddisfare la domanda dell’industria di serbatoi a pressione per idrogeno sicuri, leggeri e di alta qualità.
La collaborazione mirava a raggiungere il miglior rapporto costo-prestazioni dei serbatoi a pressione implementando un nuovo processo di produzione di massa che utilizza il materiale towpreg.
Sfruttando l’esperienza e il know-how di Voith e Huntsman nei prodotti per il processo di filament winding, le due aziende stanno costruendo serbatoi di maggiore capacità di stoccaggio senza compromettere la sicurezza alle alte pressioni, con l’obiettivo di raggiungere la produzione in serie. Consentendo il miglior rapporto costo-prestazioni grazie ai towpreg (alto numero di filamenti pre-impregnati con una quantità ottimale di resina), Carbon4Tank 700-bar H2 è una soluzione migliorata e sostenibile per lo stoccaggio dell’idrogeno, che soddisfa gli standard di qualità del settore automobilistico.
Serbatoi H2 a più alta densità di stoccaggio
I serbatoi di H2 di tipo IV da 700 bar sviluppati per l’uso in autocarri a zero emissioni alimentati a idrogeno mostrano significativi miglioramenti delle prestazioni rispetto ai serbatoi di tipo IV convenzionali (Figura 1).
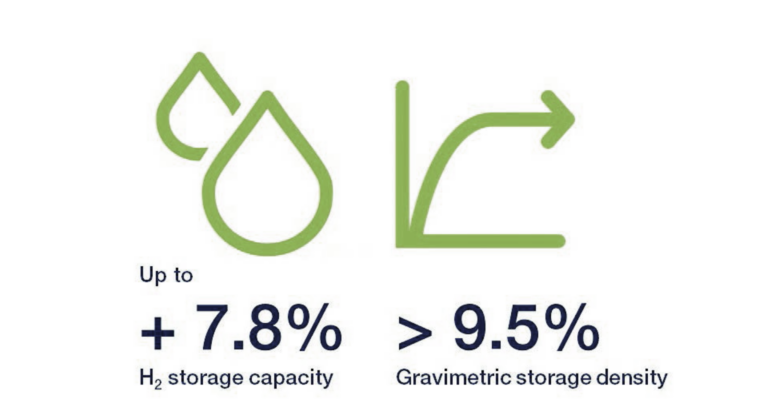
Figura 1: Risultati relativi ai serbatoi di H2 di tipo IV da 700 bar con il nuovo sistema towpreg Voith Composites Carbon4 Tank GEN II – serbatoio di idrogeno di tipo IV da 700 bar con capacità di 15,5 kg di H2, lunghezza di 2.140 mm e diametro di 555 mm.
Grazie ai vantaggi prestazionali del design dei serbatoi H2 di Voith, il nuovo sistema di resina towpreg di Huntsman Advanced Materials ha aiutato Voith a migliorare il costo totale di gestione (TCO) dei nuovi serbatoi, rispettando al contempo gli standard di qualità e sicurezza dell’industria automobilistica.
Requisiti rigorosi per uno stoccaggio sicuro dell’idrogeno
I requisiti dei produttori di autocarri per i serbatoi di idrogeno sono chiari e rigorosamente definiti. I cosiddetti serbatoi a pressione di Tipo IV devono garantire lo stoccaggio di idrogeno compresso a pressioni elevate, fino a 700 bar. Pertanto, i serbatoi compositi devono soddisfare i seguenti requisiti:
- soddisfare gli standard automobilistici: il regolamento UN/ECE n°134 regolamenta
- i requisiti tecnici, per i quali i serbatoi devono resistere ai test di resistenza agli urti e agli agenti chimici e ai cicli di fatica a varie temperature, per garantire uno stoccaggio e un trasporto sicuri dell’idrogeno;
- compatibilità con la produzione di massa: il progetto doveva soddisfare gli obiettivi di produzione e di costo dell’industria, grazie alla produzione ad alta velocità e alla riproducibilità;
- leggerezza: serbatoi a pressione più leggeri consentono una maggiore capacità di stoccaggio e si traducono in una maggiore autonomia e in un carico utile più elevato;
oith Composites e Huntsman Advanced Materials hanno unito le forze e hanno individuato nel processo di produzione towpreg la soluzione migliore, perché offre diversi vantaggi. Poiché la linea di impregnazione towpreg opera a una velocità fino a 100 m/min, la produttività aumenta. Un eccellente controllo della qualità assicura un contenuto ottimale di resina e la riproducibilità di serbatoi di alta qualità e sicurezza in un ambiente di processo pulito.
Le possibilità di avvolgimento aggiuntive rispetto all’avvolgimento convenzionale dei filamenti consentono di ridurre lo spessore delle pareti del composito e, di conseguenza, il consumo di materiale e il peso complessivo del serbatoio a pressione.
Entrambi i partner hanno unito il loro know-how e la loro esperienza per sviluppare una nuova generazione di materiale towpreg a base di fibra di carbonio dedicato alla produzione di serbatoi di idrogeno di tipo IV ad alte prestazioni da 700 bar: Huntsman Advanced Materials si è concentrata sulla formulazione di sistemi di resine a base epossidica con prestazioni termomeccaniche ottimizzate e facilità di processo, mentre Voith Composites ha lavorato sulla progettazione dei serbatoi, sulle certificazioni e sul processo automatizzato per una produzione su larga scala efficace dal punto di vista dei costi, per una maggiore efficienza economica dei serbatoi di H2 ad alta pressione.
Sviluppo di una nuova generazione di towpreg
È stata sviluppata una nuova formulazione a base epossidica per conferire al materiale towpreg maggiori possibilità di stoccaggio, una reologia specifica, l’adesività e la coesione dei filamenti di fibra di carbonio per ottimizzare la produzione del serbatoio senza sacrificare le prestazioni termomeccaniche.
La soluzione towpreg Araldite può essere conservata fino a 3 mesi a 23°C dopo la produzione delle bobine di towpreg, riducendo così i problemi logistici, il consumo di energia, i costi di stoccaggio e le operazioni che richiedono tempo.
Il profilo reologico porta a un’ottima impregnazione del nastro di carbonio durante la produzione dei towpreg, a una velocità fino a 100 m/min. L’adesività specifica della resina e la viscosità a temperatura ambiente sono state messe a punto per ottenere un equilibrio ottimale tra rigidità del tow e drappeggiabilità. I filamenti di fibra di carbonio si tengono insieme durante il processo di avvolgimento e possono allargarsi quando vengono depositati sul layup del serbatoio a bassa e alta tensione per raggiungere una larghezza del nastro adeguata.
L’adesività dei towpregs consente di raggiungere la massima velocità di avvolgimento della macchina (fino a 6 m/sec.) e di posizionare accuratamente i tow sul percorso prestabilito, durante la produzione dei serbatoi a pressione. Il posizionamento altamente accurato delle fibre e la possibilità di raggiungere angoli di avvolgimento più bassi senza slittamenti consentono di ottimizzare lo schema di avvolgimento e il design (Figura 2).
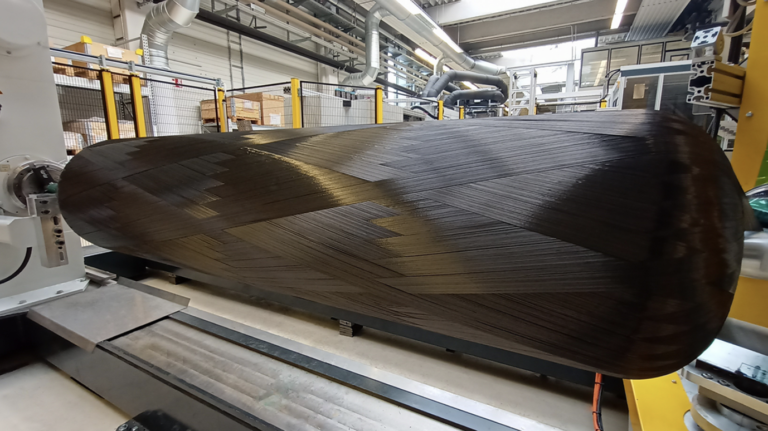
Fig. 2: Schema di avvolgimento specifico
Sia lo sviluppo del sistema di resine che l’ottimizzazione del design del serbatoio a pressione hanno beneficiato dell’esperienza di simulazione cinetica della polimerizzazione offerta da Huntsman. La simulazione della polimerizzazione fornisce uno strumento prezioso per valutare rapidamente gli effetti delle modifiche ai cicli di polimerizzazione e per ottenere informazioni su tutte le aree del pezzo simulato. Sono stati generati modelli dettagliati di dati del materiale per fare previsioni accurate sulla temperatura di esotermica, sul grado di polimerizzazione e sulle temperature di transizione vetrosa (Tg).
Si tratta di un potente strumento per accelerare lo sviluppo del prodotto e ottimizzare la produzione, con conseguente aumento della qualità dei pezzi e riduzione dei tempi di ciclo di produzione.
La Figura 3 mostra la distribuzione della temperatura durante il ciclo di polimerizzazione del serbatoio per tenere sotto controllo la temperatura esotermica e prevedere il comportamento della polimerizzazione. Il ciclo di polimerizzazione complessivo dei serbatoi è stato ottimizzato per aumentare la produzione e raggiungere il grado ottimale di polimerizzazione del sistema di resina per garantire la sicurezza. Le prestazioni termomeccaniche, statiche e dinamiche, nonché la resistenza chimica, sono governate dal sistema di resina e sono state ottimizzate per resistere in modo sicuro a sollecitazioni estreme durante la vita dei serbatoi.
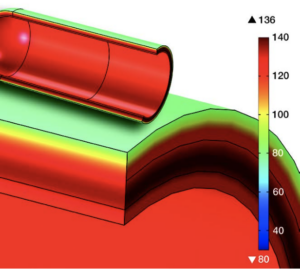
Fig. 3: Simulazione di polimerizzazione di serbatoi a pressione
In sintesi, questo nuovo materiale towpreg consente un aumento della produttività grazie alla rapida produzione interna delle bobine, all’eccezionale velocità di avvolgimento e ai cicli di polimerizzazione controllati; nuove possibilità di avvolgimento per nuovi design di lay-up; un ottimo controllo e riproducibilità dei parametri di produzione per garantire qualità e sicurezza durante la vita dei serbatoi a pressione e tempi di polimerizzazione più brevi per una maggiore produttività.
Uso ottimizzato del materiale towpreg per una produzione economica e completamente automatizzata di serbatoi H2 di tipo lV
Voith ha individuato diversi modi per migliorare il TCO:
- la produzione interna del materiale towpreg ottimizza la catena del valore dei serbatoi H2, riducendo le spinte dei costi lungo la catena di fornitura e i costi di stoccaggio e trasporto;
- tasso di scarto estremamente basso grazie a processi di impregnazione controllati e monitorati online per i più elevati standard di qualità automobilistica; la riduzione del consumo di materiale nel processo di impregnazione e nel successivo processo di avvolgimento fa scendere i costi e riduce il peso del serbatoio ottenendo le migliori prestazioni meccaniche dal materiale di carbonio;
- le capacità di progettazione offerte dalle nuove possibilità di avvolgimento (possibilità di angoli ridotti) consentono di ridurre lo spessore del laminato. Ciò consentirà una maggiore capacità di stoccaggio di H2 per kg di composito. L’aumento della produttività nell’intero processo produttivo è ottenuto grazie a linee di produzione completamente automatizzate; velocità di avvolgimento più elevate (tre volte più veloci della WFW); indurimento rapido con la nuova formulazione della resina;
- il layout di produzione ben studiato secondo i principi del Composito 4.0 favorisce l’efficienza dei costi con meno errori e difetti.
I sistemi di stoccaggio H2 plug and drive soddisfano i requisiti degli OEM di autocarri
Voith Composites e Voith Turbo hanno sviluppato congiuntamente un sistema completo di stoccaggio di H2 pronto all’uso per autocarri pesanti (Figura 4). Il sistema completo, che include le periferiche H2 e il controllo elettrico, è caratterizzato da prestazioni eccezionali e lunga durata.
Il sistema di stoccaggio plug and drive, modulare e basato su una piattaforma, viene offerto con 4-8 serbatoi di idrogeno di tipo IV. Il peso ridotto e le pareti sottili del serbatoio di idrogeno da 700 bar consentono di aumentare il carico utile di circa 5 tonnellate e di aumentare l’efficienza dello spazio sul camion rispetto alla versione elettrica a batteria. Il modulo completo di stoccaggio dell’idrogeno, dall’ugello del serbatoio all’ingresso della cella a combustibile, un sistema collaudato e pronto per l’installazione con 700 bar in qualità di serie automobilistica, è pronto per la guida dopo meno di 10 minuti di ricarica. Il sistema di stoccaggio di H2 plug and drive di Voith è adatto a lunghe distanze e consente un’autonomia fino a 1.000 km.
“Questo progetto comune illustra perfettamente come una collaborazione fiduciosa possa accelerare lo sviluppo e il time to market”, ha dichiarato Simon Burkel. “La condivisione delle competenze e la comprensione dei vincoli e delle esigenze reciproche sono state determinanti per il successo di questo sviluppo”, ha aggiunto Carolin Cichosz.
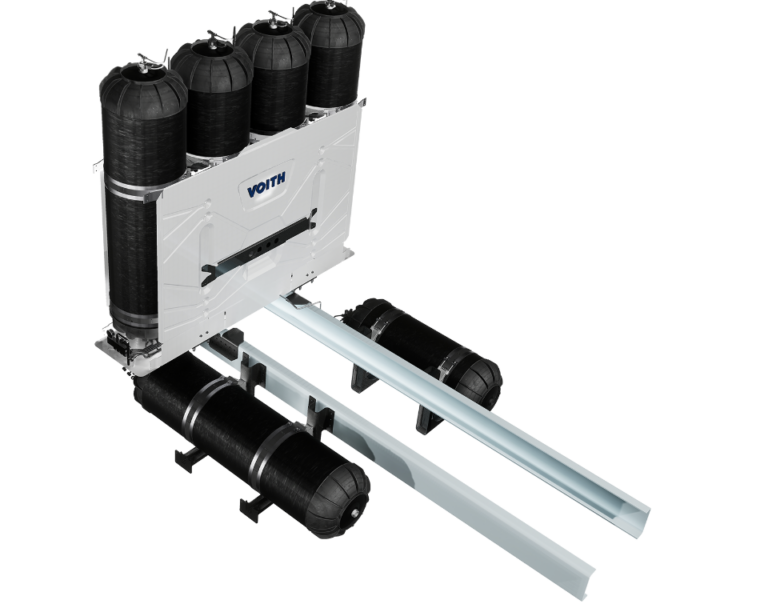