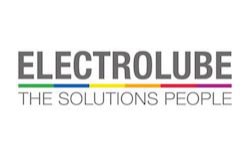
Il ruolo dei Lubrificanti per contatti nell’ industria automobilistica
L’industria automobilistica continua a posizionarsi all’avanguardia per quanto concerne lo sviluppo tecnologico e a svolgere un ruolo di guida per tutte le altre industrie. I più recenti sviluppi nell’industria riguardano le innovazioni elettroniche, sia nel miglioramento dell’esperienza di guida per pilota e passeggeri che per l’evoluzione degli standard di sicurezza (come ad esempio con la frenata assistita o il controllo di velocità). In questo momento il focus è indirizzato all’evoluzione dei motori, passando dai motori a combustione interna verso sistemi che utilizzino fonti alternative di energia al fine di preservare l’ambiente, dove gli esempi più notabili sono i veicoli elettrici (EV) e le opzioni ibride (HEV). In quest’ottica nuove sfide si stanno affacciando per circuiti, contatti e resistenze elettriche.
Indipendentemente dall’industria presa in considerazione, I lubrificanti per parti elettriche sono utilizzati per migliorare la performance e l’affidabilità di contatti e connessioni elettriche. L’utilizzo di questi lubrificanti, inventati originariamente nel 1941 dal fondatore di Electrolube, si è diffuso ampiamente per decenni all’interno di molteplici differenti industrie, ed è diventato al giorno d’oggi un fattore cruciale nelle prestazioni delle componenti automobilistiche.
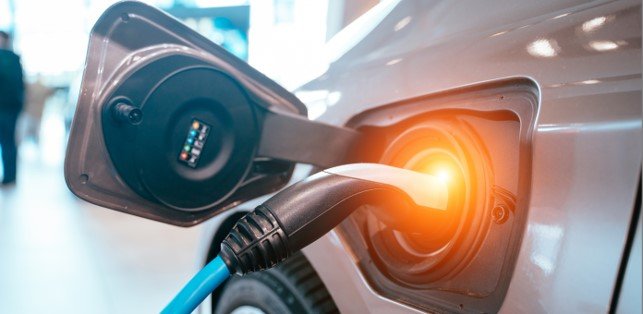
I lubrificanti per contatti sono grassi ed oli specificatamente formulati per ridurre l’attrito e l’usura, e per migliorare le prestazioni elettriche della corrente tra interfacce metalliche, come ad esempio negli interruttori o connettori. L’applicazione di lubrificanti per contatti permette di ricoprire tutte le imperfezioni della superficie, visto che nessuna interfaccia metallica ne è priva, migliorando le prestazioni e aumentando la durata della vita del contatto stesso. Riempiendo gli spazi d’aria tra i contatti, i lubrificanti per contatto aumentano notevolmente la superficie effettiva, a loro volta prevenendo l’arco elettrico, il relativo aumento di temperatura e la formazione di ossido. Forniscono inoltre una barriera agli agenti contaminanti presenti nell’aria e riducono gli effetti dell’attrito facilitando il movimento regolare. Inoltre, l’uso di lubrificanti per contatti viene generalmente valutato in base alle loro caratteristiche di “sensibilità”, migliorando la qualità del movimento ad esempio di un interruttore o di semplici contatti di plastica-plastica. Sia nel caso che l’applicazione sia per componenti interne, come le bocchette di ventilazione dell’aria condizionata; che per componenti esterni come le reg olazioni dello specchio laterale; o che sia per contatti critici all’interno del cablaggio del veicolo; le applicazioni per i lubrificanti per contatti sono in continuo aumento all’interno dei progressi nelle tecnologie “CASE” (Connected, Autonomous, Shared, Electric).
Ci sono 3 ragioni principali per le quali i lubrificanti per contatti vengono utilizzati nelle applicazioni automobilistiche:
- Per migliorare il trasferimento elettrico e l’affidabilità del contatto
I lubrificanti per contatti aumentano le superfici di contatto riempiendo eventuali imperfezioni e riducendo la resistenza elettrica. Con l’evoluzione delle automobili, la tecnologia si è estesa ad operazioni sempre più importanti per la sicurezza, e con “richiami” in aumento dovute a componenti elettronici, è imperativo che queste connessioni critiche per la sicurezza siano mantenute correttamente. In un recente rapporto di AlixPartners, è stato evidenziato che i “richiami” per correggere i guasti negli impianti elettronici o elettrici sono cresciute del 30% all’anno negli ultimi anni. Anche se tali guasti possono includere anche problemi nel software, la stragrande maggioranza di queste sono in realtà causate da guasti legate a componenti elettrici integrati. In qualità di fornitore di soluzioni elettrochimiche approvato secondo IATF 16949, a Electrolube viene spesso richiesto di aiutare a prevenire il verificarsi di tali problemi e di comprendere appieno l’impatto che tali guasti possono avere sulle aziende, comprese le conseguenze sulla reputazione del marchio per il produttore automobilistico. È quindi estremamente importante considerare tutti gli aspetti dei sistemi elettronici, compresa la connessione tra i dispositivi e la selezione del lubrificante per contatti corretto.
Tradizionalmente, la protezione delle proprietà elettriche di interruttori e connessioni nell’industria automobilistica era riferito ad interruttori generali e a bassa tensione; nel corso degli anni con lo sviluppo di collegamenti elettronici sempre più interconnessi all’interno dei veicoli, l’utilizzo dei lubrificanti si è mosso verso applicazioni sempre più critiche. Fino ad arrivare all’attualità dove lo spostamento verso la tecnologia delle auto elettriche, ha posto una ulteriore serie di sfide, tra cui la presenza di un numero maggiore di connettori elettrici con tensioni molto più elevate. Con esperienza in altri settori al di fuori di quello automobilistico dove le tensioni sono normalmente medie e alte (come ad esempio centrali elettriche, stabilimenti di galvanotecnica), Electrolube ha già una gamma di prodotti per soddisfare le nuove esigenze del mercato dei veicoli elettrici.
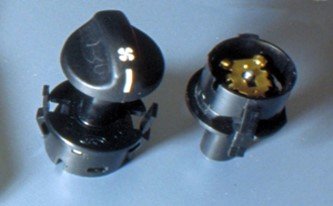
2. Per ridurre gli effetti delle influenze ambientali esterne, riducendo la corrosione e l’usura
L’ aumento dei dispositivi elettronici all’interno di connessioni sempre più complesse ed interconnesse ha obbligato i produttori ad utilizzare materiali differenti al fine di mantenere o ridurre il peso finale dei veicoli. L’utilizzo di tali materiali, come l’alluminio, ha portato una serie di nuove sfide nella manutenzione dei sistemi elettronici dell’automobile, dove diventa importante prevenire eventuali ossidazioni e corrosioni elettrochimiche in presenza di umidità e contatto tra metalli differenti. La corrosione causata dal “fretting” può essere ad esempio ridotta applicando un lubrificante sui contatti in alluminio, riducendo notevolmente i guasti delle parti elettriche.
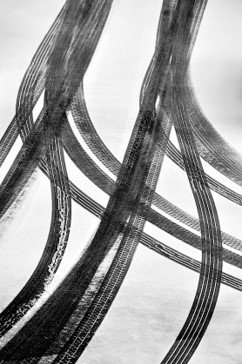
Le influenze ambientali includono variazioni di temperature, esposizione all’umidità e ad atmosfere corrosive. Profonde variazioni di temperatura possono modificare le caratteristiche di consistenza di un lubrificante; ad esempio un valore di penetrazione di 320 rilevato a 25 C˚, può drasticamente ridursi in casi di temperature di -40 C˚ o più basse. La corretta scelta dei lubrificanti in relazione alle caratteristiche ambientali di un’applicazione viene determinata da Electrolube grazie a un serie di test che permettano di evidenziare i differenti comportamenti dei vari prodotti e di fornire una migliore assistenza al cliente.
Questi test includono prove di umidità seguiti da test in nebbia salina, prove di resistenza al cloro e verifiche con diversi materiali. I test combinati sull’umidità e la nebbia salina sottopongono i lubrificanti al 90% di umidita a 35 C˚ per 3 settimane, a cui segue 1 settimana a 35 C˚ nella camera di nebbia salina. La protezione dei substrati in rame e acciaio viene valutata visivamente dopo questo test. Tipicamente, i lubrificanti sintetici, come Electrolube CTG forniscono la migliore protezione in questo tipo ambiente. Nel caso di contatti in oro e argento, i risultati in nebbia salina evidenziano che alcuni lubrificanti a base minerale non sono adatti per proteggere questi materiali in ambienti difficili. Infine, anche i test in condizioni estreme (2 mesi a 35 C˚ in un ambiente ossidativo saturo di cloro) confermano che Electrolube CTG fornisce una protezione eccezionale, seguita da vicino da Electrolube CG53A e CG60.
3. Per migliorare la qualità e la “sensibilità’” in connettori ed interruttori.
I lubrificanti per contatti sono anche ampiamente utilizzati in molte applicazioni per migliorare la “sensibilità’” di un interruttore, dando così l’impressione di alta qualità. Ciò vale anche per molte applicazioni all’interno dei veicoli, garantendo che i contatti metallo-metallo, plastica-metallo e plastica-plastica abbiano un buon collegamento tra le parti, riducendo così il rumore e il movimento quando sottoposti a vibrazioni causate dal normale funzionamento dell’automobile. Con un passaggio verso auto più silenziose, i miglioramenti nella tecnologia degli pneumatici e l’evoluzione dei veicoli elettrici, l’interno del veicolo diventa un posto molto più silenzioso e come tale, la qualità di questi contatti e la diminuzione generale del rumore sono essenziali per garantire un’esperienza di guida di alta qualità.
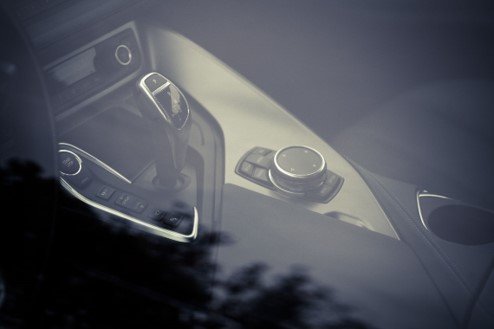
Prodotti come Electrolube CG60 e SPG sono stati utilizzati per tali applicazioni automobilistiche per molti anni, garantendo il massimo comfort nell’esperienza di guida. In alcuni casi, un lubrificante fluorato, come l’EGF di Electrolube, può essere necessario per offrire prestazioni ancora maggiori. L’utilizzo di questa tipologia di lubrificanti sarà sempre più necessario in futuro con il continuo aumento dei sistemi elettronici all’interno dei veicoli e con lo spostamento verso la tecnologia delle auto elettriche. In quest’ottica un recente studio di Research and Markets conferma che nel comparto automotive la componente elettronica sarà quella che crescerà più rapidamente nell’orizzonte temporale 2020/2025 grazie allo sviluppo di tecnologie sempre più avanzate, tra cui sistemi di assistenza alla guida e integrazioni di sicurezza.
L’industria automobilistica è in un periodo di costante cambiamento ed evoluzione. Passando a HEV ed EV, una nuova serie di sfide per connettori elettrici, interruttori e dispositivi vengono proposte e continueranno ad evolversi anche per gli anni a venire. Gli sviluppi nella tecnologia delle batterie e nelle interfacce utente, nelle fonti di carburante alternative e nell’evoluzione della guida assistita aggiungeranno ulteriori sfide. Affrontando l’apparentemente piccolo compito di garantire connessioni di alta qualità, affidabili e protette, i lubrificanti per contatti aiuteranno a soddisfare queste nuove esigenze. Ad esempio, il propulsore di un’auto elettrica è in media due volte e mezzo più costoso rispetto ai propulsori convenzionali (AlixPartners), ostacolandone la crescita del mercato. Tuttavia, questo costo aggiuntivo tenderà a ridursi naturalmente nel corso del tempo con economie di scala e attraverso miglioramenti della tecnologia. Ciò, combinato con la riduzione dei costi complessivi, derivata da una manutenzione di elevata qualità e da una diminuzione dei “richiami” per guasti elettrici, è la ragione per la quale i produttori devono mettere la scelta dei lubrificanti per contatti in cima alle loro agende di sviluppo ora e per molti anni a venire.
Si ringrazia per la stesura di quest’ approfondimento Jade Bridges – Responsabile del supporto tecnico globale di Electrolube
(Traduzione di M.M)