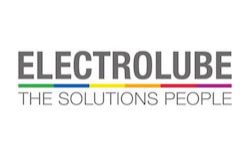
Autopsia del PCB – Variabili pre e post rivestimento che causano guasti alla scheda
I conformal coating sono ampiamente utilizzati in applicazioni in cui la sicurezza è un aspetto fondamentale, dove l’impatto di un guasto elettronico può avere conseguenze molto gravi. Per garantire che un conformal coating soddisfi i requisiti desiderati, i gruppi rivestiti devono essere esposti ad ambienti differenti tramite condizioni di test appropriate per stabilire l’intervallo di prestazioni e gli eventuali limiti del prodotto. I test di base monitorano le prestazioni elettriche e la resistenza all’ umidità a, mentre i test avanzati possono imitare condizioni severe come nebbia salina, temperature estreme o rapidi cambiamenti ambientali.
I conformal coating sono progettati per proteggere i PCB e garantire che funzionino in modo efficiente nel loro ambiente di utilizzo finale. Tuttavia, ci sono casi in cui le schede potrebbero non funzionare adeguatamente nonostante siano rivestite correttamente.
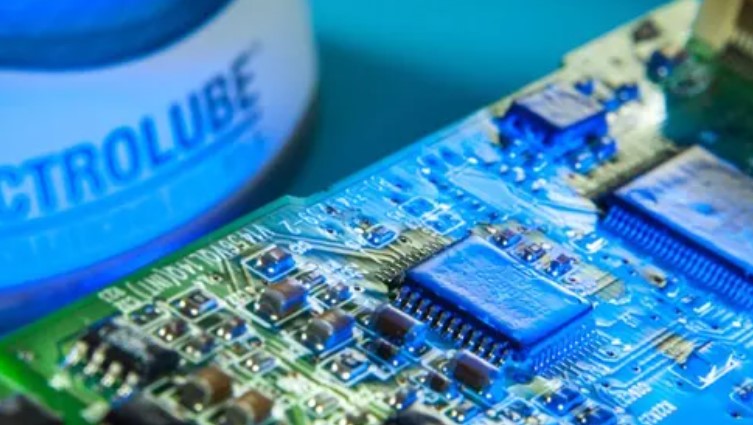
Phil Kinner, Global Business & Technical Director for Conformal Coatings di Electrolube, esplora i motivi per cui i test sono così importanti ed esamina diverse variabili che possono causare guasti alla scheda.
L’elettronica si evolve per ridurre le dimensioni, e le possibilità di guasti aumentano. Man mano che i componenti si riducono, molti progetti sfidano anche i limiti di producibilità stessa. È ovvio che quando i designer spingono i confini, la possibilità di fallimento aumenta notevolmente.
Oltre ai problemi di guasto relativi alla progettazione, la vicinanza dei componenti a causa della maggiore densità rende intrinsecamente l’hardware più vulnerabile alla corrosione. La pulizia prima del processo di rivestimento farà molto per rimuovere le condizioni di corrosione, consentendo l’applicazione del conformal coating in modo più efficiente per aumentare la resistenza di isolamento e mitigare gli effetti dell’ambiente operativo in caso di guasto.
PULIZIA DEL COMPONENTE
Quando un PCB si guasta è probabile che sulla scheda fossero già presenti condizioni problematiche prima del processo di rivestimento.
Una minaccia al PCB, è certamente l’applicazione di un conformal coating su componenti e superfici che non sono state pulite adeguatamente prima dell’applicazione del rivestimento.
La prima e più critica procedura da utilizzare è eseguire un’ispezione prima dell’applicazione del rivestimento. Ciò è essenziale perché convalida la qualità complessiva del PCB, assicurando che sia adatto allo scopo e in linea con le specifiche del cliente. L’ispezione in questa fase è anche fondamentale per rilevare eventuali condizioni che potrebbero potenzialmente causare guasti alla scheda.
Gli agenti contaminanti presenti sulla superficie prima dell’applicazione del rivestimento saranno sigillati dall’operazione e causeranno problemi a lungo termine – tali contaminanti potrebbero includere impronte digitali, residui di flusso e umidità, nonché altri inquinanti atmosferici.
I pannelli devono essere sempre puliti e asciugati prima del’ applicazione del conformal coating per ottenere prestazioni ottimali.
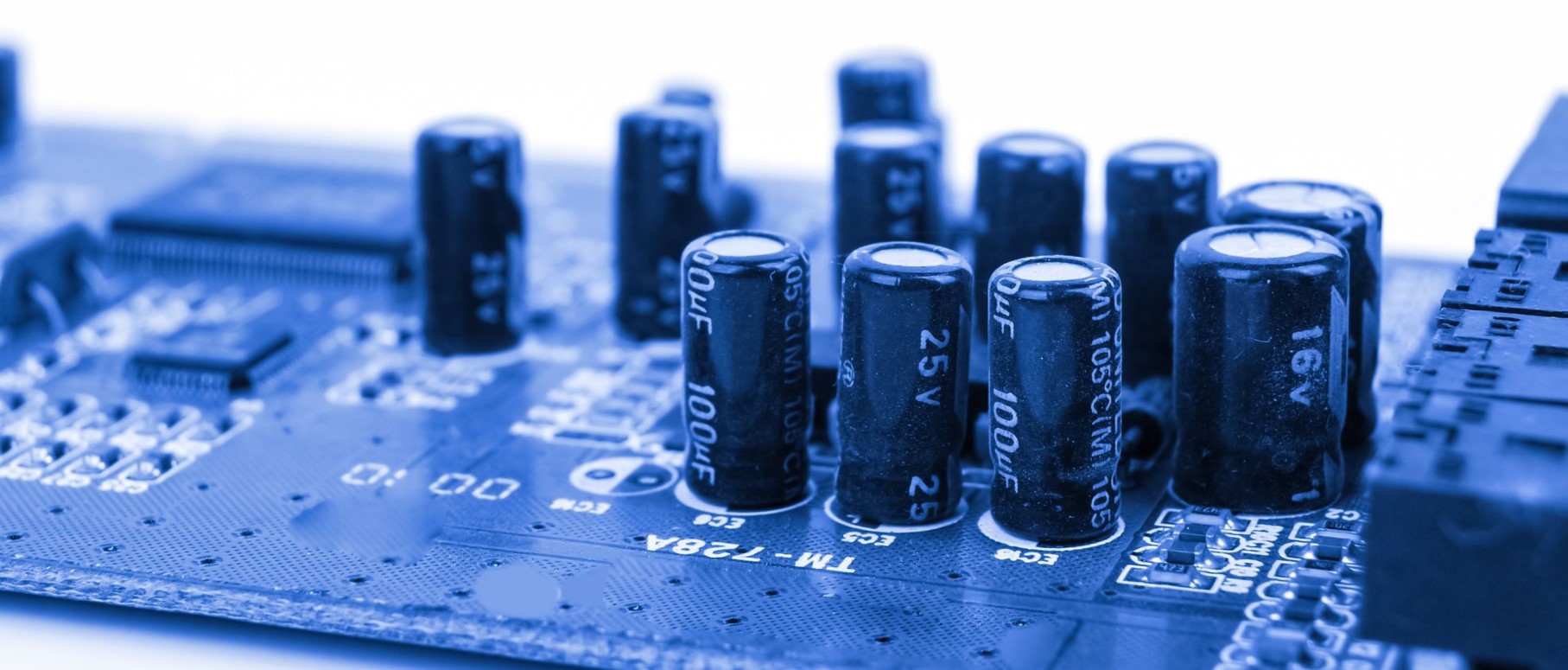
IL CALORE
Un altro nemico dei PCB e dei componenti è il calore. Durante il funzionamento, i materiali all’interno del PCB subiranno variazioni di temperatura e ogni componente ha un intervallo specifico di calore che può assorbire, in gran parte dipendente dalle sue dimensioni e forma. L’elettronica di maggiore potenza e densità produce più calore e il calore eccessivo può causare uno stress meccanico significativo che può influire sulle connessioni di saldatura e bruciare i componenti. È essenziale gestire il trasferimento di calore in modo efficiente per aumentare la durata del dispositivo e prevenire guasti. Il surriscaldamento non solo accelera i meccanismi di guasto, ma può anche far diventare i dispositivi troppo caldi per essere maneggiati e, in alcuni casi, presentare un rischio di incendio.
Oltre ai problemi che circondano il calore, la continua spinta verso la miniaturizzazione implica che gli spazi siano ridotti quindi diventa sempre più difficile soddisfare i requisiti di dispersione. Anche cambiamenti molto lievi nell’ambiente, che si tratti di un aumento di polvere, umidità più elevata, spruzzi d’acqua o esposizione a materiali gassosi potenzialmente corrosivi, possono essere sufficienti per causare fallimenti delle prestazioni.
Sebbene questo non sia un elenco esaustivo di ogni singolo fattore che contribuisce al guasto del PCB, dovrebbe aiutare a fornire una panoramica completa degli elementi chiave a cui prestare attenzione. Infine, il design stesso potrebbe essere responsabile del guasto del PCB. Per aumentare la durata della scheda, è imperativo assicurarsi che siano stati selezionati i componenti e i materiali appropriati, che il layout della scheda sia sufficiente e che il progetto sia verificato per i suoi requisiti specifici.
MALFUNZIONAMENTO PCB POST RIVESTIMENTO
Ci sono una serie di variabili che potrebbero essere responsabili di un malfunzionamento del circuito stampato dopo il processo di rivestimento. In generale, i risultati potrebbero indicare una cattiva selezione e / o applicazione del prodotto, o qualche problema sottostante derivante da una preparazione superficiale insufficiente o da qualche attività chimica in corso sotto il rivestimento stesso.
I conformal coating con prestazioni scadenti rischiano di non isolare le superfici del PCB quando l’acqua si condensa sopra esso. Esistono molti conformal coating che resistono a questo tipo di condizioni, quindi questo tipo di problema può essere evitato effettuando una selezione appropriata del materiale.
Se il rivestimento non si è asciugato adeguatamente, non sarà in grado di sviluppare appieno le sue proprietà protettive. La corretta applicazione è un prerequisito per il successo del rivestimento, ad esempio, una scarsa copertura, uno spessore insufficiente e una copertura dei bordi possono essere difficili da ottenere con conformal coating non adeguati.
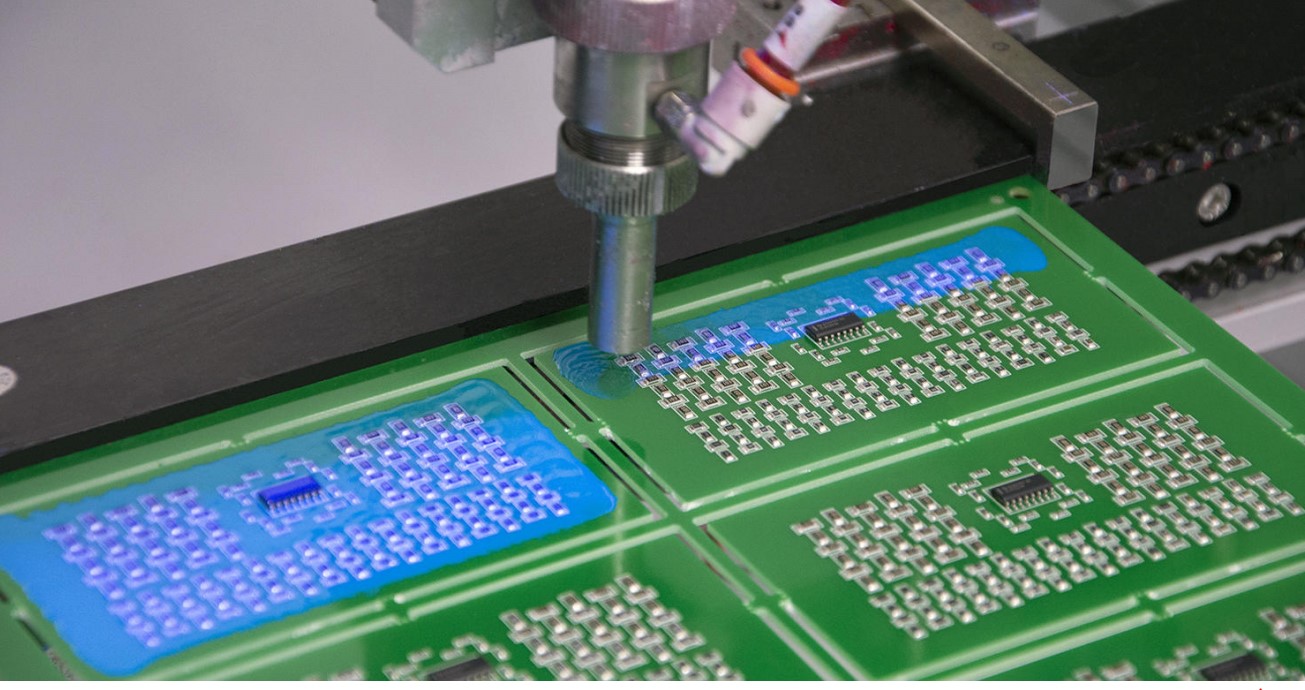
SPESSORE E MODALITA’ DI APPLICAZIONE DEI CONFORMAL COATING
Una combinazione di selezione dei materiali e tecnica di applicazione risolverà questo tipo di problemi. Un conformal coating può avere uno spessore compreso tra 30 e 130 micron, lo spessore maggiore viene ottenuto mediante l’applicazione di più strati di rivestimento. Cercare di ottenere uno spessore di film secco di 130 micron da un singolo processo di rivestimento con un materiale acrilico a base di solvente, ad esempio, è una ricetta per un disastro, che potrebbe provocare un’eccessiva formazione di bolle, restringimento del film, delaminazione del rivestimento e stress aggiuntivo sui componenti. Il risultato sarà una protezione più scarsa. Puntare a 30-50 micron uniformi e concentrarsi sul raggiungimento di una copertura perfetta in ogni applicazione è un approccio molto migliore per migliorare la protezione dei circuiti elettronici.
Il raggiungimento dello spessore di rivestimento corretto è importante; tenere sempre presente che un rivestimento troppo spesso può causare la rottura del rivestimento durante la polimerizzazione, o persino la rottura dei componenti stessi.
Il fattore determinante numero uno del successo per l’affidabilità del rivestimento risiede nell’applicazione. Spesso un materiale scadente applicato bene può essere altrettanto buono o talvolta migliore di un materiale con grandi proprietà che viene applicato male. Naturalmente, alcuni materiali “si applicano meglio” di altri e rendono questo processo il più semplice.
UMIDITA’
Il test più severo per valutare le prestazioni di un conformal coating è in condizioni di bagnato, sia che ciò sia dovuto a condensa, immersione o nebbia salina. Per fornire protezione in queste circostanze, è essenziale ottenere una copertura priva di difetti al 100%, e questo rappresenta una vera sfida sia per il materiale stesso che per il processo di applicazione. Fortunatamente, una nuova classe di materiali di conformal coating a due parti denominata “2K” consente di ottenere uno spessore molto maggiore e una copertura perfetta, con un livello di protezione molto più elevato. I vantaggi in termini di prestazioni superiori dei materiali 2K di Electrolube, che combinano le proprietà resistenti di una resina di incapsulamento con la facile applicazione di un coating, sono stati dimostrati positivamente nei test più severi a cui questi materiali possono essere sottoposti.
Conclusione
I PCB sono la forza vitale di tutti i dispositivi elettronici su cui facciamo affidamento ogni giorno, da smartphone, tablet, PC e laptop all’illuminazione stradale, TV, frigoriferi, microonde e automobili. Pertanto, i materiali selezionati per proteggere i gruppi elettronici fanno la differenza, in particolare se sono necessari per sopportare shock fisici e cicli termici sostanziali. Ispezioni e test pre e post rivestimento sono essenziali per garantire che il PCB funzioni in modo affidabile e aumenti la sua durata. Selezionare il materiale appropriato per la protezione richiesta, applicarlo e polimerizzarlo bene. Verificare le interazioni con altre sostanze chimiche di processo e pulire accuratamente l’assieme prima del rivestimento. Se possibile, dedica del tempo a semplificare il processo di rivestimento in fase di progettazione. I guasti dei PCB possono purtroppo verificarsi in seguito all’applicazione di un rivestimento conforme, ma la notizia positiva è che il guasto può essere prevenuto con ispezioni pre-rivestimento sistematiche, metodo di selezione / applicazione corretto del materiale e ulteriori test di post-rivestimento rigorosi.