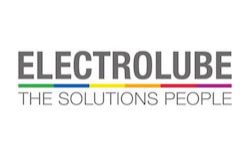
PCB autopsy – Pre- and post-coating variables that cause board failures
Conformal coatings are widely used in applications where safety is a key concern, where the impact of an electronic failure can have very serious consequences. To ensure that a conformal coating meets the desired requirements, coated assemblies must be exposed to different environments through appropriate test conditions to establish the performance range and any limitations of the product. Basic tests monitor electrical performance and resistance to ‘humidity a, while advanced tests can mimic severe conditions such as salt spray, extreme temperatures or rapid environmental changes.
Conformal coatings are designed to protect PCBs and ensure that they function efficiently in their end-use environment. However, there are cases where the boards may not work properly despite being properly coated.
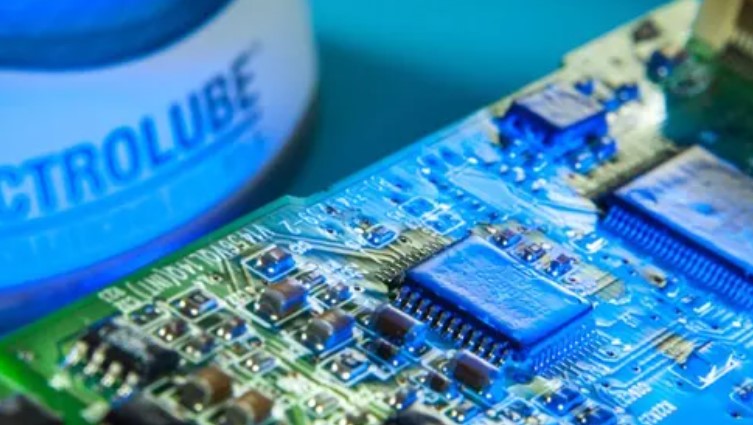
Phil Kinner, Global Business & Technical Director for Conformal Coatings at Electrolube, explores why testing is so important and examines several variables that can cause board failures.
As electronics evolve to reduce size, the chances of failure increase. As components become smaller, many designs also challenge the limits of manufacturability itself. It is obvious that when designers push the boundaries, the possibility of failure is greatly increased.
In addition to design-related failure problems, the proximity of components due to higher density inherently makes hardware more vulnerable to corrosion. Cleaning before the coating process will do much to remove corrosion conditions, allowing conformal coating to be applied more efficiently to increase insulation resistance and mitigate the effects of the operating environment in the event of failure.
COMPONENT CLEANING
When a PCB fails, it is likely that problematic conditions were already present on the board prior to the coating process.
One threat to the PCB, is certainly the application of conformal coating to components and surfaces that have not been properly cleaned prior to coating application.
The first and most critical procedure to be used is to perform an inspection before applying the coating. This is essential because it validates the overall quality of the PCB, ensuring that it is fit for purpose and in line with customer specifications. Inspection at this stage is also critical to detect any conditions that could potentially cause board failure.
Contaminants on the surface prior to coating application will be sealed by the operation and will cause long-term problems-such contaminants could include fingerprints, flow residues and moisture, and other air pollutants.
Panels should always be cleaned and dried before ‘conformal coating application for optimal performance.
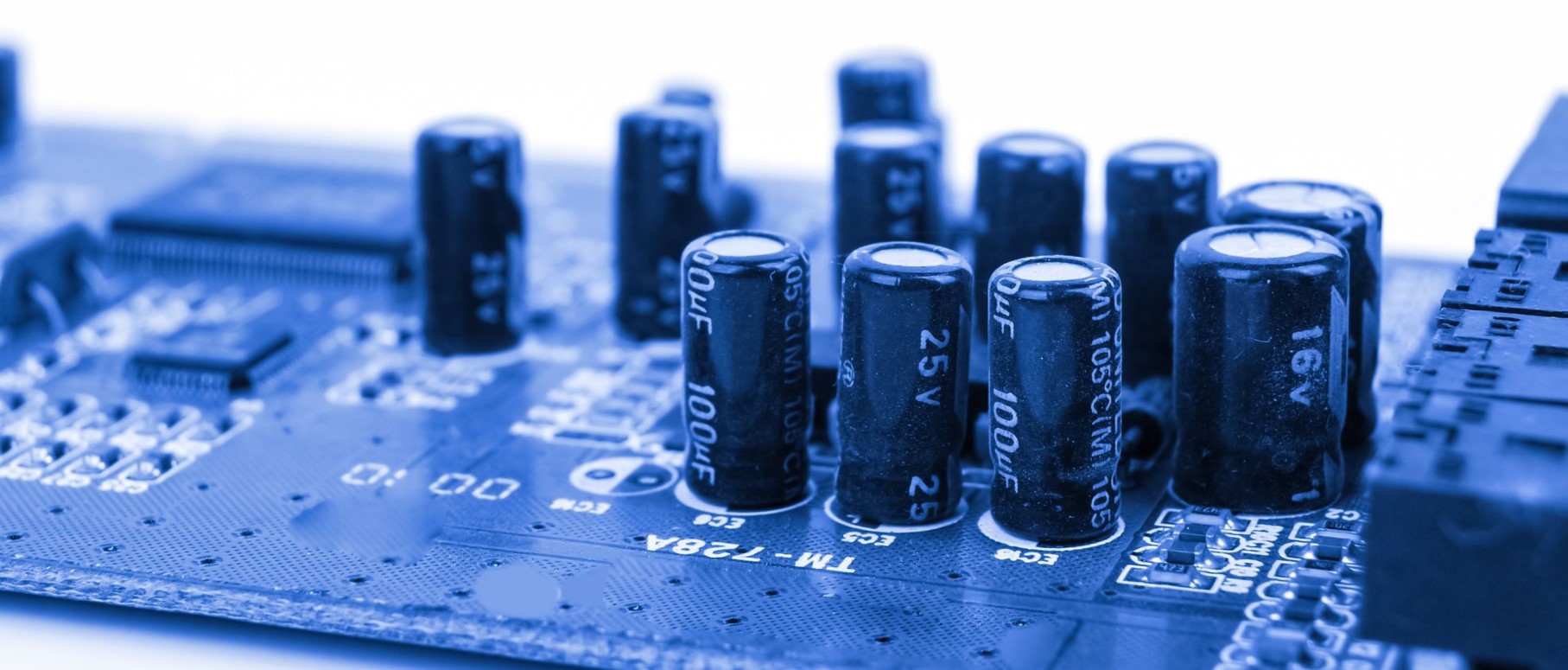
THE HEAT
Another enemy of PCBs and components is heat. During operation, materials within the PCB will undergo temperature changes, and each component has a specific range of heat it can absorb, largely dependent on its size and shape. Electronics of higher power and density produce more heat, and excessive heat can cause significant mechanical stress that can affect solder connections and burn components. It is essential to manage heat transfer efficiently to increase the life of the device and prevent failure. Overheating not only accelerates failure mechanisms, but can also make devices too hot to handle and, in some cases, present a fire hazard.
In addition to the problems surrounding heat, the continuing push toward miniaturization means that spaces are small so it becomes increasingly difficult to meet dispersion requirements. Even very minor changes in the environment, whether it is an increase in dust, higher humidity, splashing water, or exposure to potentially corrosive gaseous materials, can be enough to cause performance failures.
Although this is not an exhaustive list of every single factor contributing to PCB failure, it should help provide a comprehensive overview of the key elements to pay attention to. Finally, the design itself could be responsible for PCB failure. To increase the life of the board, it is imperative to ensure that the appropriate components and materials have been selected, that the layout of the board is sufficient, and that the design is verified for its specific requirements.
POST COATING PCB MALFUNCTION
There are a number of variables that could be responsible for circuit board malfunction after the coating process. In general, the results could indicate poor product selection and/or application, or some underlying problem resulting from insufficient surface preparation or some chemical activity going on under the coating itself.
Poorly performing conformal coatings risk failing to insulate PCB surfaces when water condenses on top of it. There are many conformal coatings that resist this type of condition, so this type of problem can be avoided by making appropriate material selection.
If the coating has not dried properly, it will not be able to fully develop its protective properties. Proper application is a prerequisite for coating success, for example, poor coverage, insufficient thickness, and edge coverage can be difficult to achieve with inadequate conformal coating.
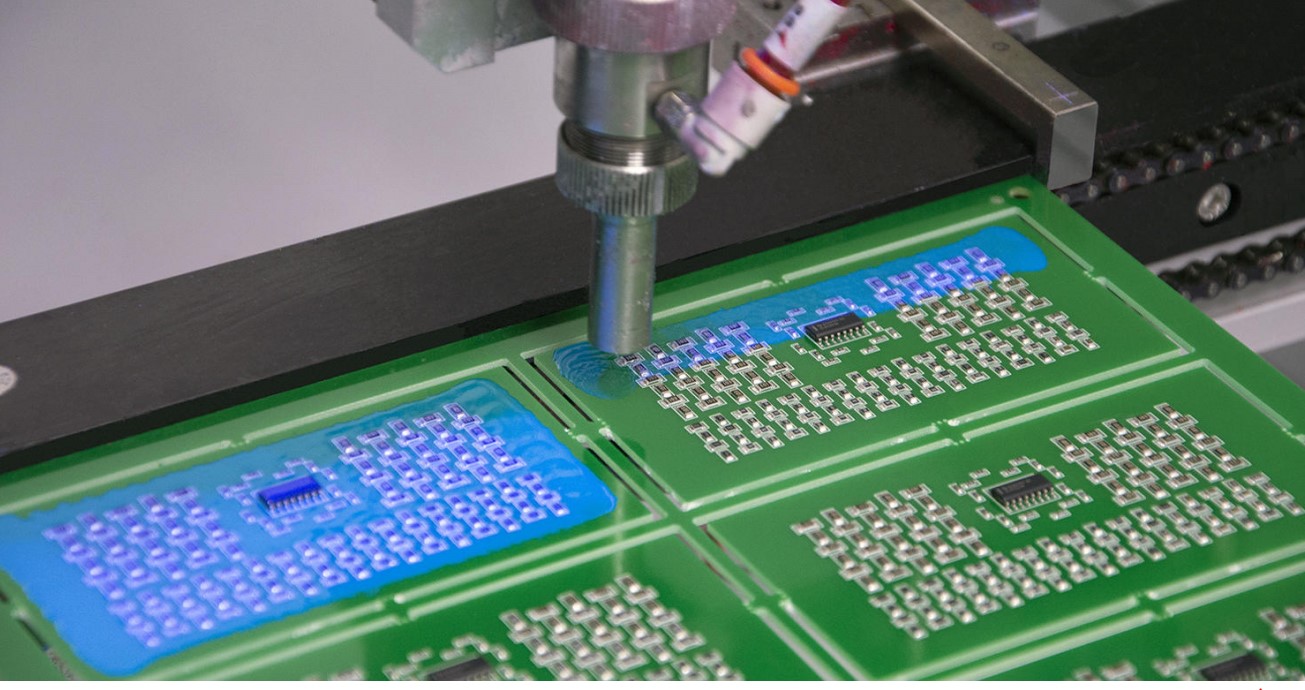
THICKNESS AND MODE OF APPLICATION OF CONFORMAL COATINGS
A combination of material selection and application technique will solve these kinds of problems. A conformal coating can be between 30 and 130 microns thick, with the greatest thickness being achieved by applying multiple layers of coating. Trying to achieve a dry film thickness of 130 microns from a single coating process with a solvent-based acrylic material, for example, is a recipe for disaster, which could result in excessive bubble formation, film shrinkage, coating delamination, and additional stress on components. The result will be poorer protection. Aiming for 30-50 micron uniformity and focusing on achieving perfect coverage in each application is a much better approach to improving protection of electronic circuits.
Achieving the correct coating thickness is important; always keep in mind that a coating that is too thick can cause the coating to crack during curing, or even break the components themselves.
The number one determinant of success for coating reliability lies in the application. Often a poor material applied well can be as good or sometimes better than a material with great properties that is applied poorly. Of course, some materials “apply better” than others and make this process the easiest.
HUMIDITY.
The most severe test to evaluate the performance of a conformal coating is in wet conditions, whether this is due to condensation, immersion or salt spray. To provide protection under these circumstances, it is essential to achieve 100 percent defect-free coverage, and this presents a real challenge for both the material itself and the application process. Fortunately, a new class of two-part conformal coating materials called “2K” allows for much greater thickness and perfect coverage, with a much higher level of protection. The superior performance advantages of Electrolube’s 2K materials, which combine the tough properties of an encapsulation resin with the easy application of a coating, have been positively demonstrated in the most severe tests these materials can be subjected to.
Conclusion
PCBs are the life force of all the electronic devices we rely on every day, from smartphones, tablets, PCs and laptops to street lighting, TVs, refrigerators, microwaves and cars. Therefore, the materials selected to protect electronic assemblies make a difference, particularly if they are required to withstand substantial physical shocks and thermal cycling. Pre- and post-coating inspections and tests are essential to ensure that the PCB functions reliably and increases its service life. Select the appropriate material for the required protection, apply and cure well. Check for interactions with other process chemicals and thoroughly clean the assembly before coating. If possible, spend time to simplify the coating process at the design stage. PCB failures can unfortunately occur as a result of applying a conformal coating, but the positive news is that failure can be prevented with systematic pre-coating inspections, correct material selection/application method, and further rigorous post-coating testing.