La corrosione dei recipienti in pressione rappresenta una sfida critica per gli impianti industriali, richiedendo soluzioni rapide, sicure ed economiche per ripristinare l’integrità strutturale e garantire la sicurezza operativa.
Nel caso di uno stabilimento petrolchimico nel Golfo Persico, un recipiente a pressione corroso minacciava la stabilità dell’impianto con segni evidenti di cavitazione e rischio di perdite imminenti. La sostituzione completa dell’apparecchiatura non era pratica né conveniente, mentre le tradizionali opzioni di saldatura comportavano rischi di sicurezza e problemi ambientali, specialmente considerando le temperature estreme della regione.
In questo caso di studio possiamo vedere le soluzioni Devcon® per la corrosione e riparazione dei recipienti in pressione.
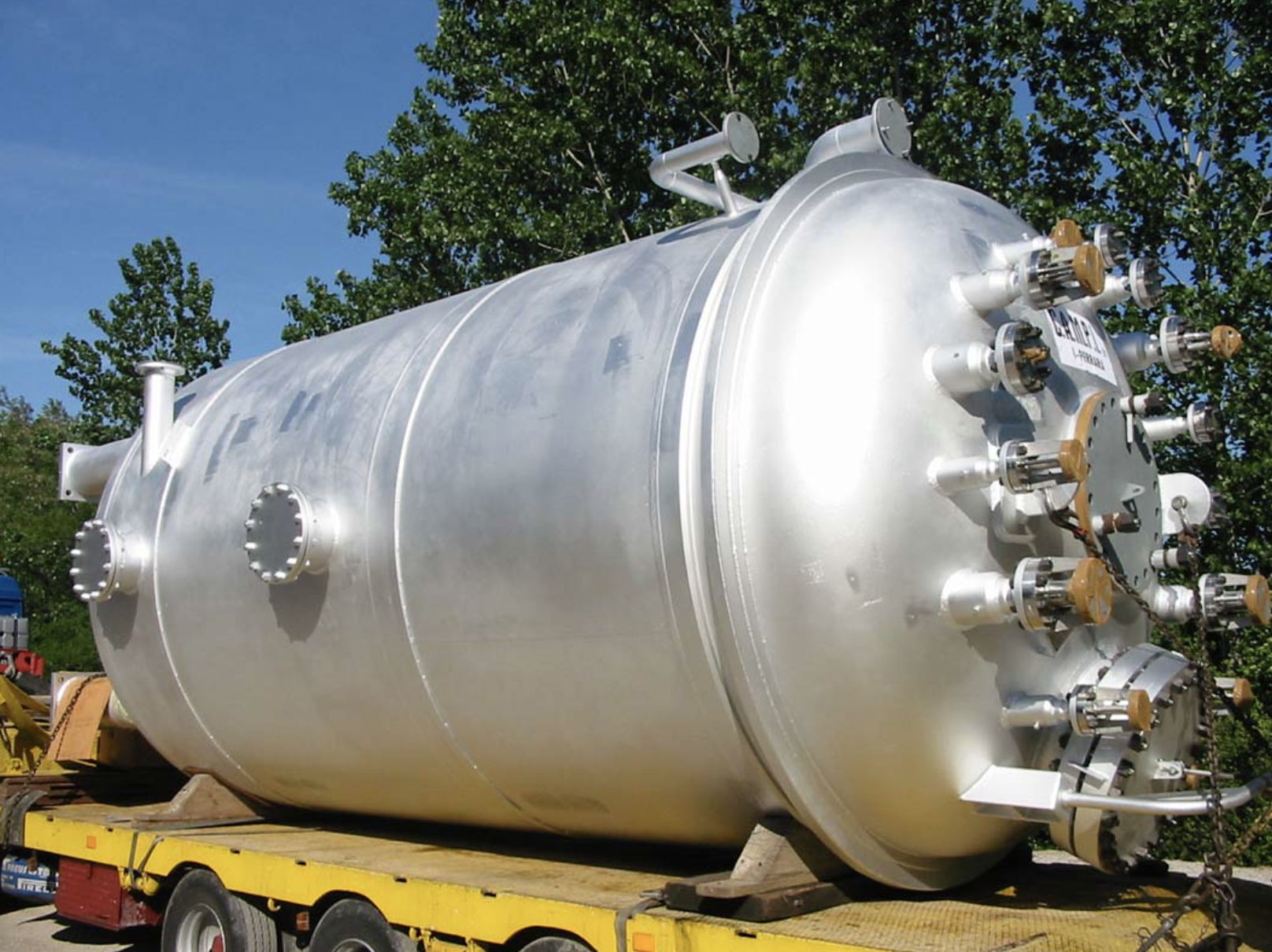
Il problema dell’impianto
Un impianto petrolchimico situato nella regione del Golfo Persico aveva un recipiente a pressione corroso che doveva essere riparato con urgenza. Con segni evidenti di cavitazione all’interno dell’apparecchiatura e un rischio crescente di perdite, il cliente cercava una soluzione di riparazione sicura, rapida ed economica.
La sostituzione dell’intera apparecchiatura non era né rapida né efficace dal punto di vista dei costi. La saldatura non era appropriata a causa di problemi di sicurezza e fattori ambientali. Inoltre, le temperature nella regione potevano raggiungere i 122°F / 50°C. Poiché la maggior parte dei lavori di riparazione doveva essere effettuata manualmente all’interno del recipiente in acciaio al carbonio da 108″ (9 piedi) per proteggere l’apparecchiatura dalla corrosione e dalle perdite, l’intervento di riparazione doveva essere rapido e semplice.
La soluzione con prodotti Devcon®
Per riparare e rimettere rapidamente in servizio il recipiente a pressione sono stati scelti i rivestimenti Devcon® Titanium Putty e Devcon Brushable Ceramic ad alte prestazioni. Ecco gli step:
Per la preparazione della superficie del mantello interno del serbatoio, la metà inferiore del serbatoio è stata sottoposta a sabbiatura SA3 – SSPC5 con un profilo superficiale da 80μ a 90μ. Il test di controllo del profilo superficiale è stato eseguito dal cliente per garantire il rispetto delle specifiche richieste.
La parte A e la parte B dello stucco al titanio Devcon sono state accuratamente miscelate sul tavolo di miscelazione utilizzando una spatola da 3″. Questa miscela è stata utilizzata per riempire e correggere le anomalie/difetti del recipiente.
Lo stucco Devcon Titanium è stato quindi steso per riempire tutte le anomalie, quindi lo spessore dell’applicazione è stato unificato su tutti i punti di corrosione. Dopo l’indurimento, è stato applicato il primo strato di Devcon Brushable Ceramic con un pennello manuale.
Lo spessore del film umido di Devcon Brushable Ceramic è stato confermato all’interno dell’intervallo accettabile (da 350 a 500 micron). È stato applicato un ulteriore strato utilizzando la stessa metodologia. Al termine, il rilevatore Holiday non ha rilevato alcuna scintilla.
Risultati ottenuti dalla riparazione del recipiente in pressione
Rivestimenti altamente durevoli
I rivestimenti Devcon® Titanium Putty e Devcon® Brushable Ceramic Blue forniscono una protezione anticorrosione a lungo termine che ha riportato il serbatoio a pressione alle condizioni operative originali e previste.
Installazione sicura
La saldatura a freddo offerta dal sistema di riparazione Devcon rende i rivestimenti un’alternativa molto più sicura alla saldatura in un impianto petrolchimico; l’idea principale alla base della creazione di Devcon nel 1947: evitare il lavoro a caldo (saldatura) quando si affrontano ambienti esplosivi.
Applicazione facile e veloce
Le aree con vaiolatura, corrosione ed erosione sono state riempite e riparate in poche ore, poiché i rivestimenti Devcon sono rapidi da miscelare e facili da applicare.
Oltre al vantaggio di avere un’applicazione facile e sicura, Devcon Coatings hanno contribuito a prolungare la vita utile del recipiente in pressione, evitando di pressione, evitando la necessità di sostituire l’attrezzatura e riducendo così i costi di manutenzione e i tempi di inattività. ridurre i costi complessivi di manutenzione e i tempi di inattività.