OUR PROPOSAL
Our knowledge of the chemical, our manufacturing capability, allows us to make seals directly on your component.
MASCHERPA with
DM INDUSTRY
is ready to:
- Designing the replacement of your preformed gaskets
- Verify with prototypes the goodness of the proposed solution
- Apply gaskets directly to your components
- Improve your production cycles
INTEGRATED SILICONE SEALS
Replace Preformed Gaskets
A highly reactive material is applied to a component automatically. This is first mixed with the help of a mixing system, then, applied along a perimeter.
Once cured, the material cured on the perimeter forms the foamed gasket, this remains perfectly integral with the substrate on which it is dispensed, thus increasing convenience in all subsequent stages of assembly.Thanks to this particular sealing system, it is possible to achieve hermetic properties alternative to die-cut gaskets, O-rings, rubber cords and other sealing systems.
Learn more with the technical brochure. Download now
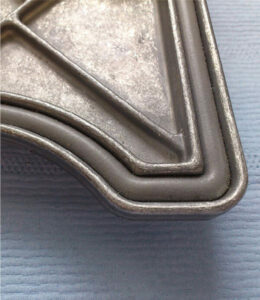
THE ADVANTAGES OF FIPFG TECHNOLOGY OVER PREFORMED GASKETS
COST REDUCTION AND INCREASE
PRODUCTION SPEED
The advantages associated with the production of the FIPFG gasket are countless, chief among them being the absence of inventory and the consequent management of myriad preformed gasket or oring part numbers, and the complex procurement system.
FIPFG technology enables the application of customized silicone gaskets, optimizing production, automating processes, and significantly reducing the time required for manual application.
Robotic application reduces costs, and integrates processes; directly producing seals for one’s own products eliminates inefficiencies.
EXCELLENT KEEPING
ON EVERY SURFACE
This sealing system enables hermetic properties as an alternative to die-cut gaskets, O-rings and other sealing systems, improving the quality and performance of seals in terms of protection against fluid, moisture and dust penetration. These gaskets do not just “fit” they are entirely made and designed to seal that particular component.
Assembly and subsequent maintenance is facilitated due to the perfect adhesion to the substrate to which the seal is applied.
GREAT FREEDOM
OF DESIGN
The ease with which the proposed machines can be programmed also allows them to operate with great design freedom: in fact, gaskets of all shapes and sizes can be made, an opportunity particularly appreciated in situations where the use of traditional gaskets is unthinkable, such as some applications in lighting and automotive.
Indeed, the designer can devise geometries of all kinds without worrying about finding the correct seal later.
The possibility of depositing the gasket directly on the part makes it possible to correct any minor differences between the design and molding of the part, modulating different thicknesses or other technical devices.
THE ADVANTAGES OF TECHNOLOGY
SILICONIC
Silicone foams are ideal for gasketing, insulation, and vibration damping, especially in applications where the sealing surface is not smooth and temperatures vary widely, due to silicone’s excellent versatility.
features and benefits
- Medium hardness (Shore 50).
- Application of low-flow adjuvants for sloping surfaces.
- Easy to use, easy to handle 1:1 mixing ratio.
- Rapid polymerization at room temperature.
- Low compression set that is maintained at high service temperatures.
- Stable and flexible over a wide temperature range.
THE CHARACTERISTICS
OF DOWSIL™ 3-8259 RF
This sealing system enables hermetic properties as an alternative to die-cut gaskets, O-rings and other sealing systems, improving the quality and performance of seals in terms of protection against fluid, moisture and dust penetration. These gaskets do not just “fit” they are entirely made and designed to seal that particular component.
Assembly and subsequent maintenance is facilitated due to the perfect adhesion to the substrate to which the seal is applied.
Resistance
to weathering
The ease with which the proposed machines can be programmed also allows them to operate with great design freedom: in fact, gaskets of all shapes and sizes can be made, an opportunity particularly appreciated in situations where the use of traditional gaskets is unthinkable, such as some applications in lighting and automotive.
Indeed, the designer can devise geometries of all kinds without worrying about finding the correct seal later.
The possibility of depositing the gasket directly on the part makes it possible to correct any minor differences between the design and molding of the part, modulating different thicknesses or other technical devices.
Stability
to temperatures
The temperatures used range from -56° up to 177°C (204°C alternating).
INDUSTRIES AND APPLICATIONS
Our solutions for your applications
The performance requirements of a foam sealant vary depending on the industry, product application, and manufacturing process.
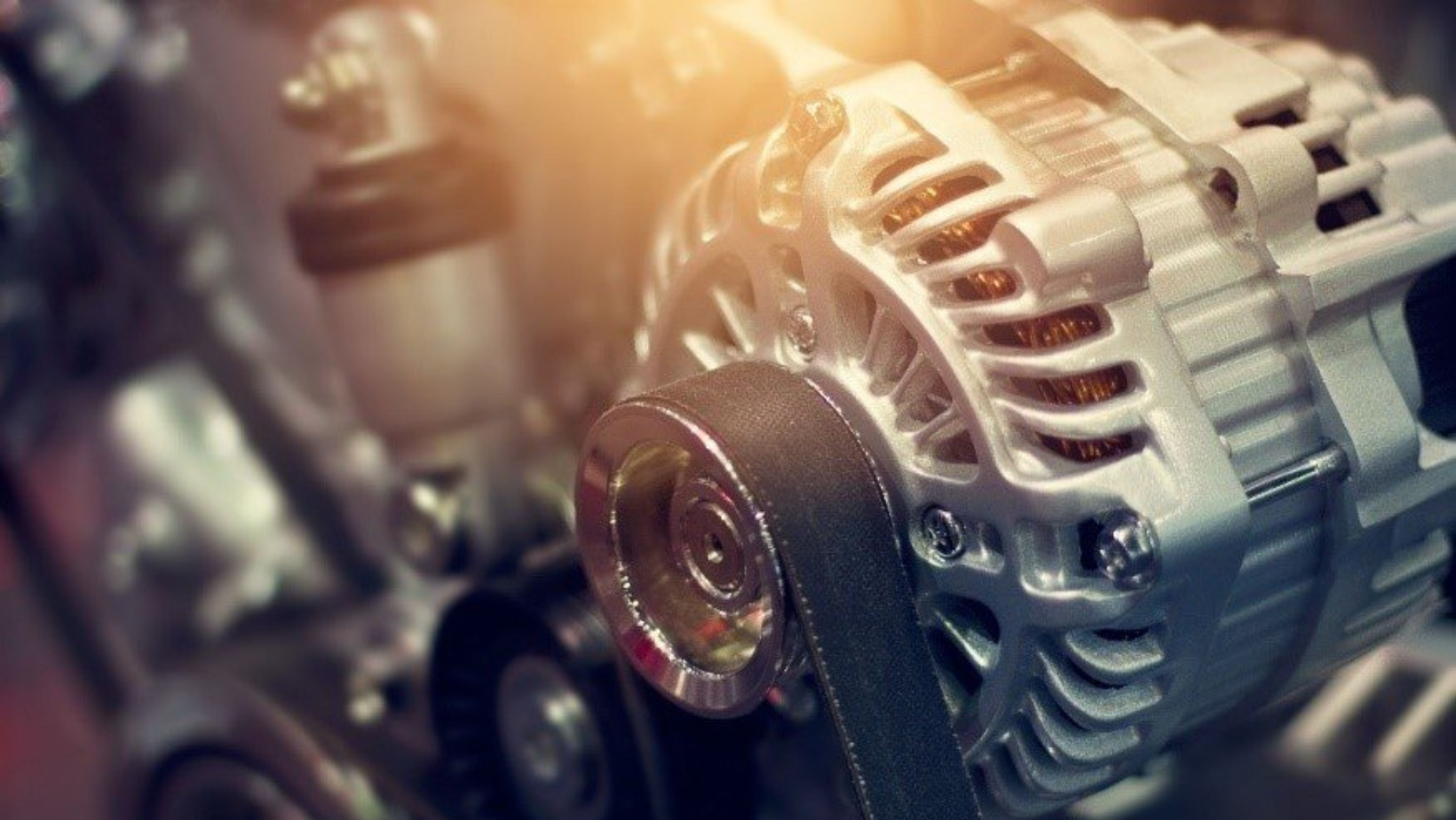
Automotive
Renowned automobile manufacturers already use DOW’s sealing systems. This is because sealing foams meet the stringent requirements of the automotive industry, such as emission standards, in combination with extremely short cycle times.
E-mobility
The cars of the future will be electric, quiet and with low emissions. The essential component of an electric car is the electric motor with its battery.
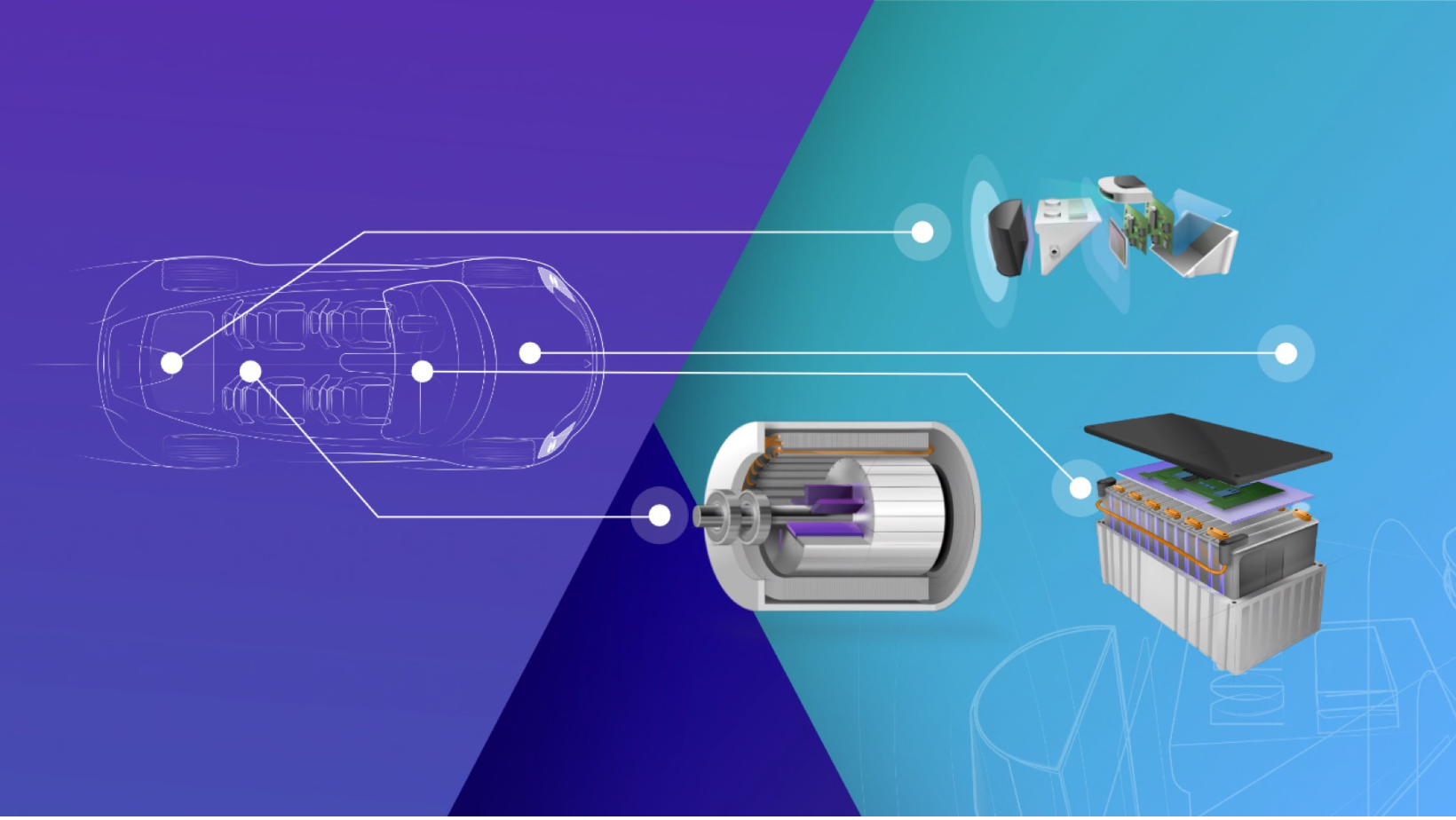
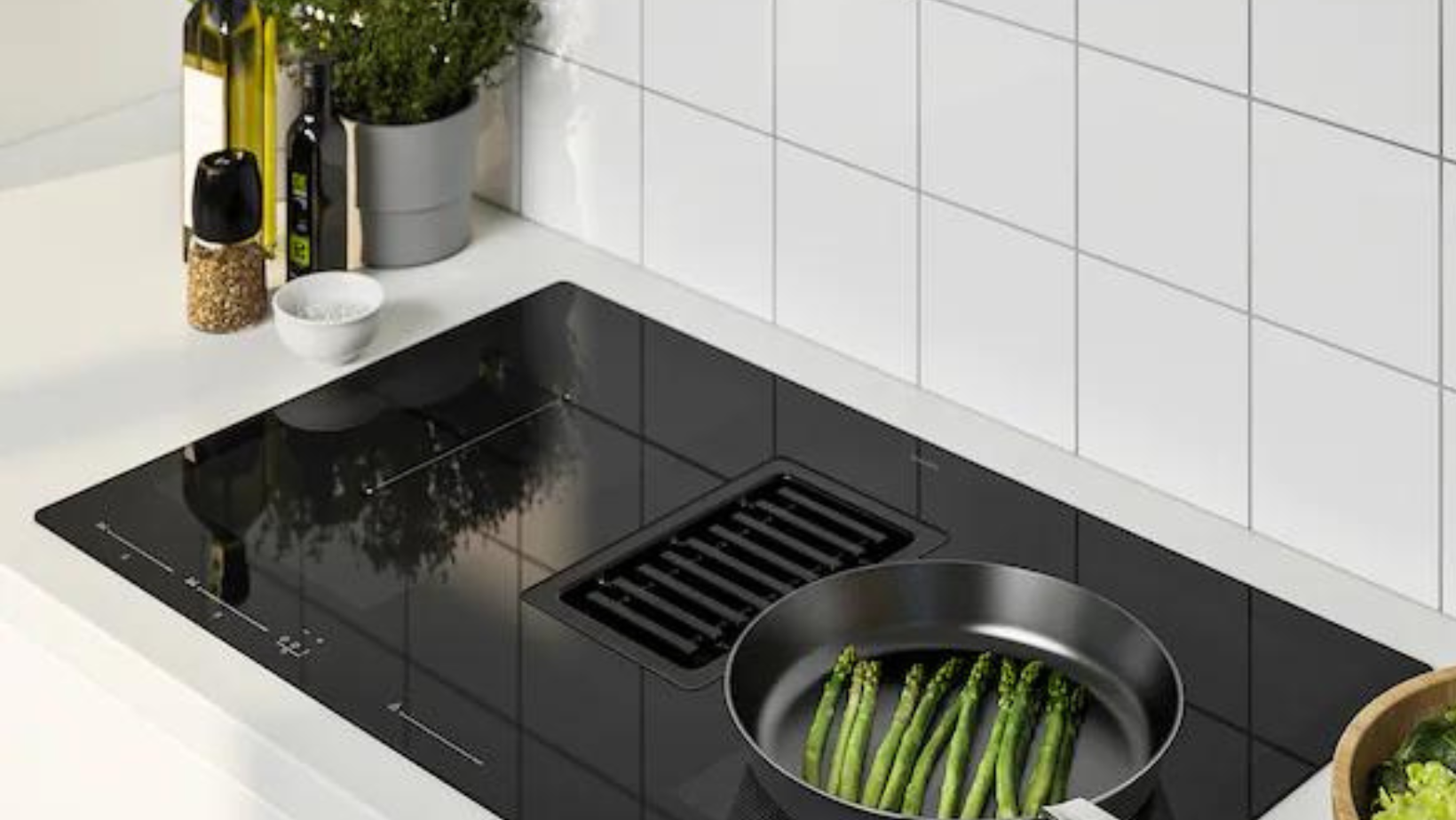
Home appliances
High volumes, fully automated production processes, extremely fast cycle times, low costs and top quality: The home appliance industry is a global business with strong competition.
Lighting
DOW foams protect illuminated components from dust, dirt and liquids. Gaskets are applied to the body of the device and seal the space between the body and the diffuser.
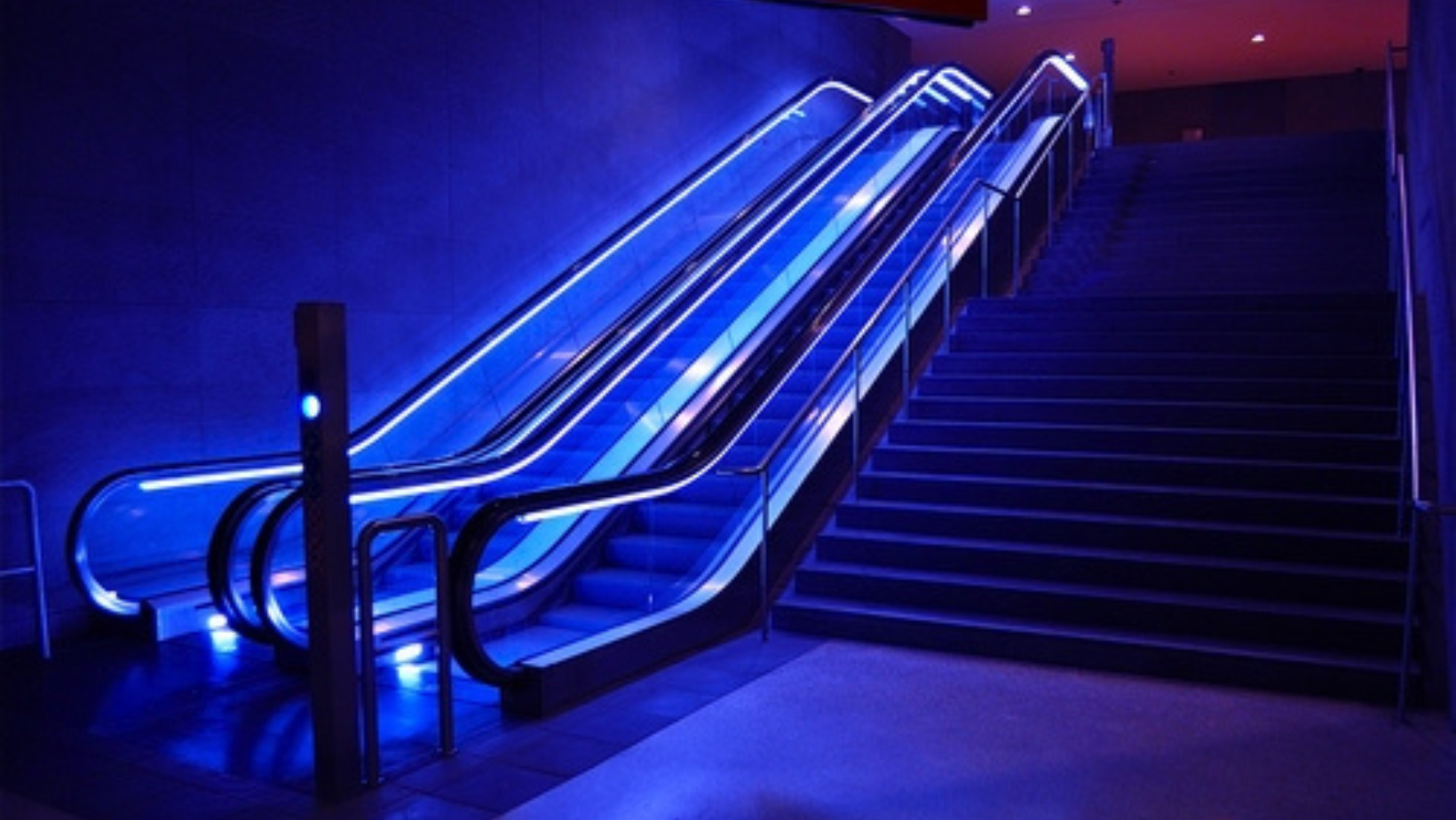
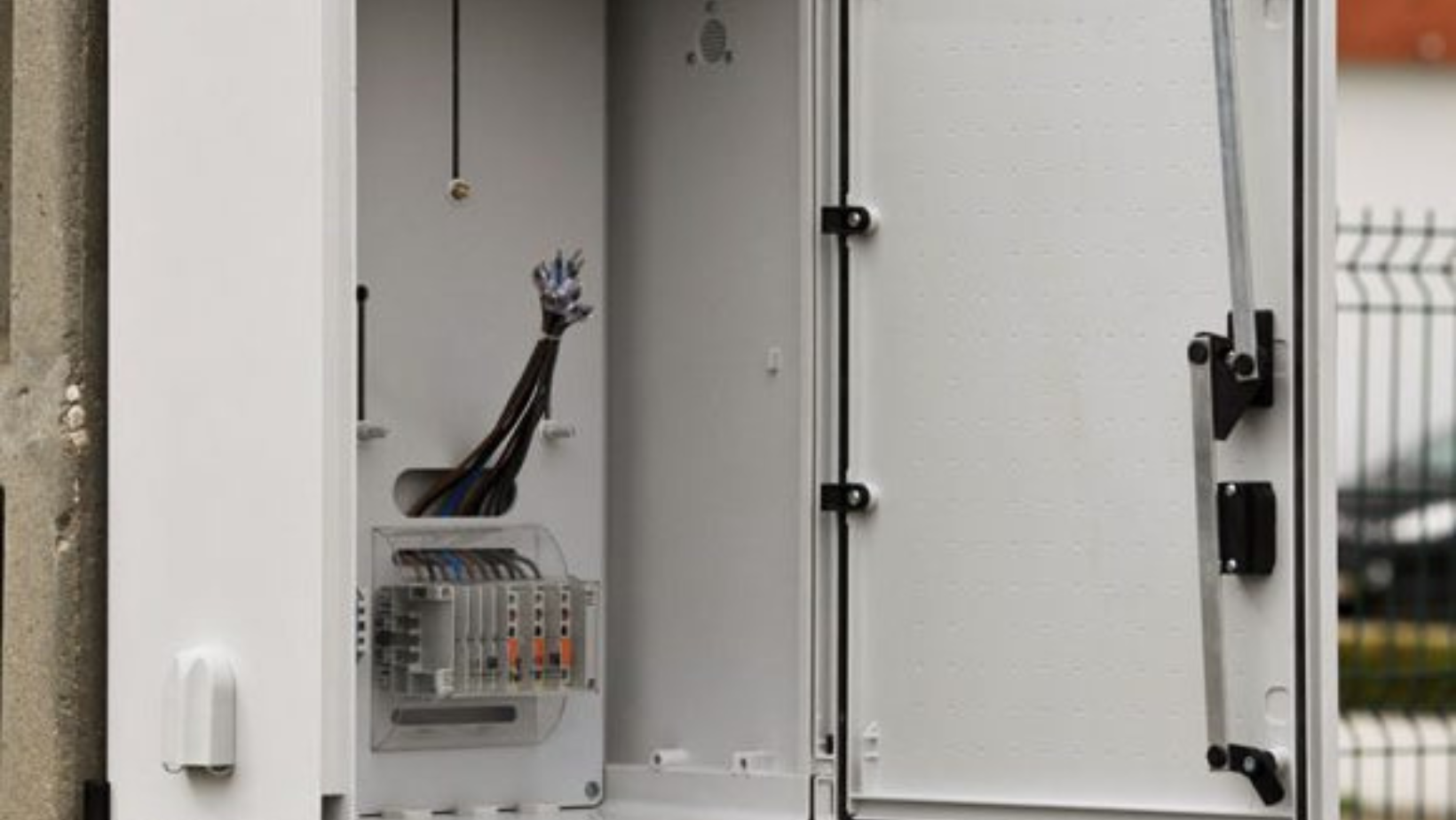
Electrical cabinets
In the control cabinet industry, tolerance compensation plays an important role in addition to optimal component protection.
Download the technical brochure
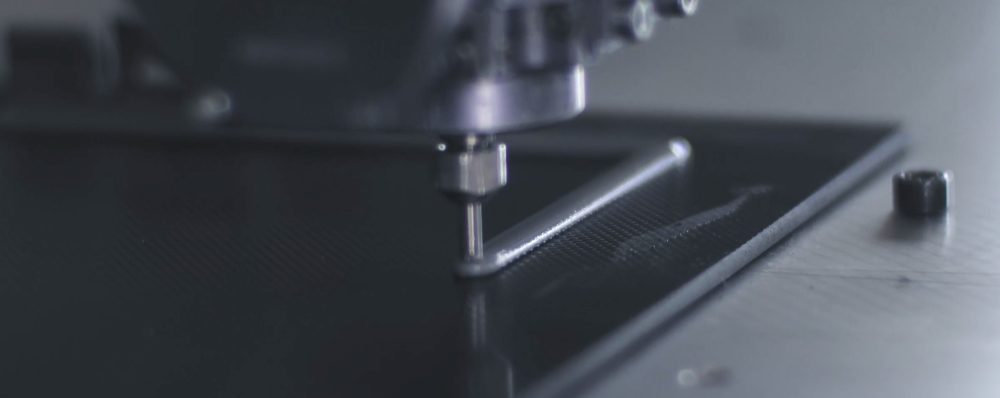