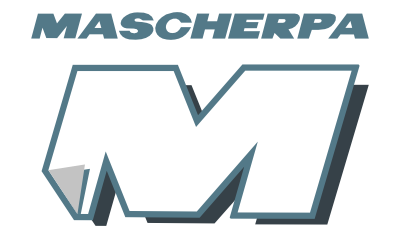
Rotational molding, or roto-molding, is a low-pressure, high-temperature production method for the manufacture of hollow articles that do not require subsequent welding and assembly steps.
The process can be used to make bodies of simple shapes (cylindrical containers or tanks) or more complex shapes (furniture accessories or automotive components) with wall thicknesses ranging from 2 to 15 millimeters
Modern machines equipped with multiple arms, which allow simultaneous production of different items and thus optimize productivity.
An important advantage of rotational molding is the absence of material waste: all the plastic loaded into the mold is used to manufacture the part.
With a properly designed mold and proper maintenance, it is possible to make complex components that are difficult if not impossible with any other technology. A proper mold and process control allow for the elimination of seam lines and welds, and also for a more uniform wall thickness than other technologies, a thickness that can be changed without making changes to the mold.
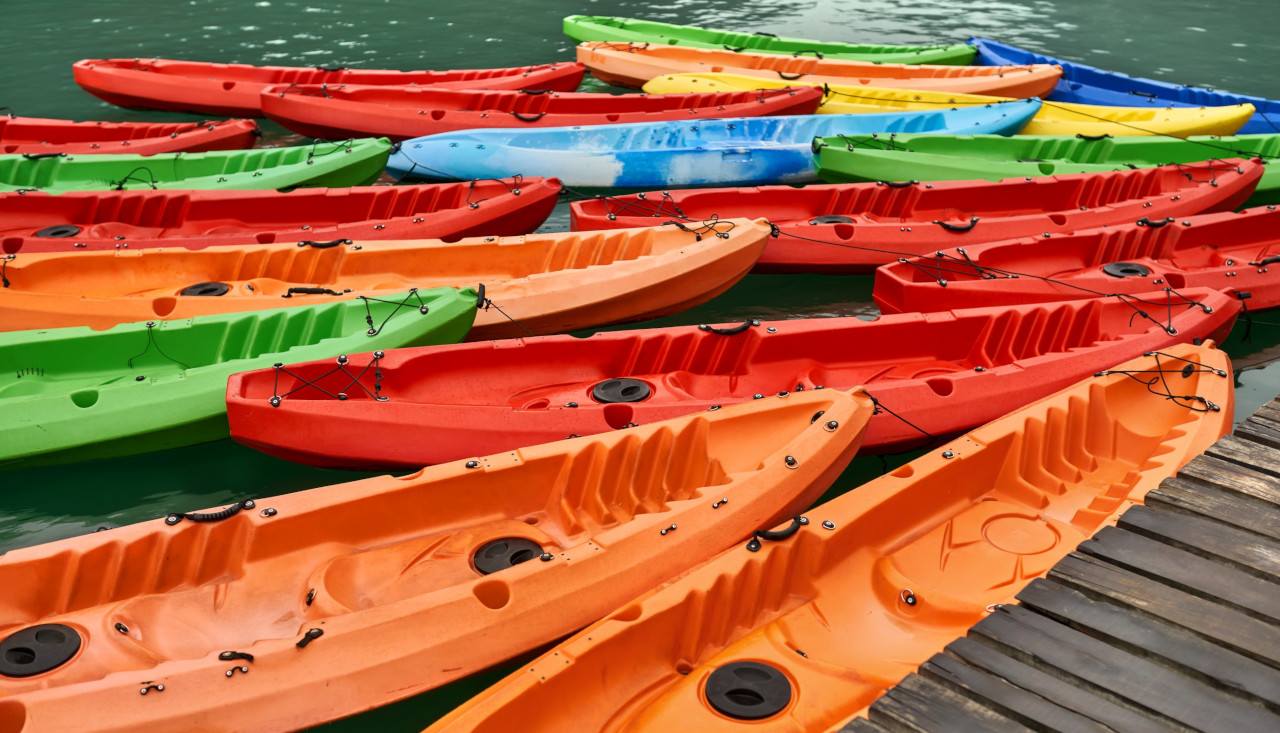
The rotational molding process
Rotational molding technology involves four steps: mold loading, mold heating, mold cooling and part extraction.
1. A hollow metal mold is loaded with a predetermined amount of powdered plastic material, equivalent to the weight of the desired product.
MOLD LUBRICATION
Molykote® D321R spray.
: Dry coating based on molybdenum disulfide for application on mold clamps without problems of soiling contact surfaces.
Molykote P-74
: Metal-free coupling paste for high-temperature applications
Molykote Separator spray
: Silicone lubricant indicated as a release agent in particularly complex places
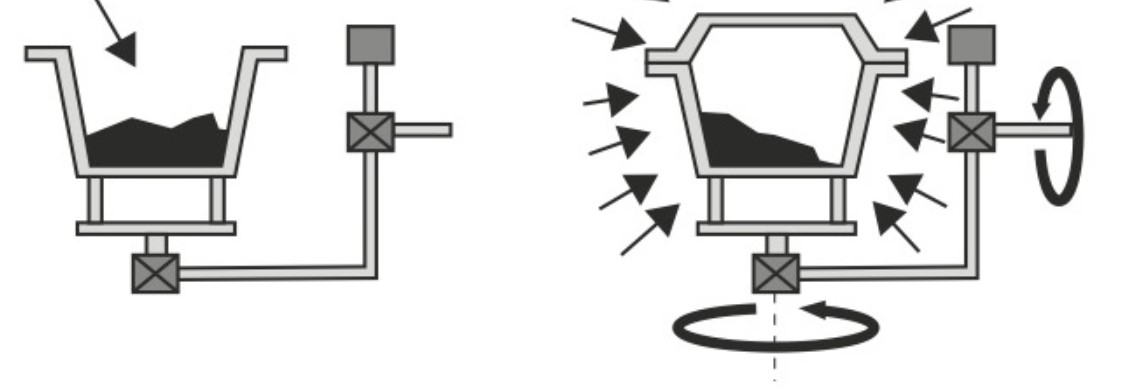
2. The mold begins to rotate in an oven, when rotation is started the entire surface of the heated mold comes into contact with the powder and becomes coated with plastic melt
ARM LUBRICATION
Krytox 227 CORRUGATOR
: special infusible grease based on PFPE/PTFE technology for use in very high temperatures (above 200°C) and very long relubrication intervals.
Petrocanada Peerless LLG
: special mineral grease with calcium sulfur complex thickener for use at high temperatures (up to 200°C).
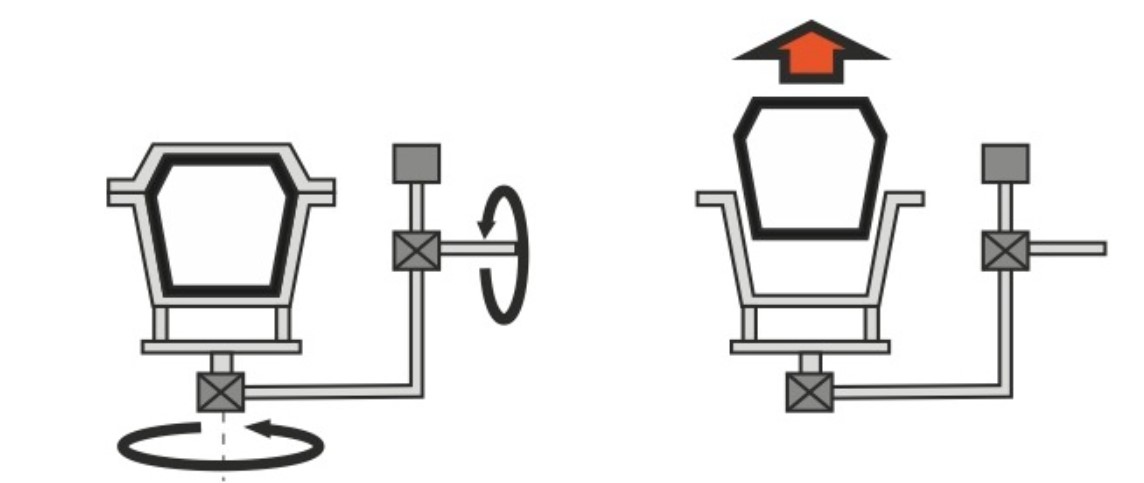
3. The hot mold is taken out of the oven and the cooling cycle begins. The mold continues to rotate even during this phase, during which it is usually exposed to high-speed jets of air and, in some cases, water spray.
4. Once sufficiently cooled, the mold can be opened and the artifact removed (last step). At this point, the powder can again be placed in the mold and the cycle repeated.
Stoner’s TraSys® provides the rotational molding plastic industry with the best in water-based release coatings. Free of alcohol and solvents, these coatings meet all existing and planned environmental regulations.
- TraSys® coatings produce a consistent, controlled release for maximum performance.
- Their long life can reduce the need for frequent spraying by the operator.
- They are safe, easy to use and work with LLDPE, LDPE, MDPE, HDPE, XLPE, PP, plastisol and nylon.
- They present minimal transfer of release materials to the printed product.They produce consistent parts without warping or sticking, allowing your production to run smoothly.
Trasys ™ 414
: strong release power for medium or small parts
Trasys ™ 715
: low release power, perfect for large surfaces
Rotoflow™
Improves the quality and consistency of polyolefin and nylon parts.
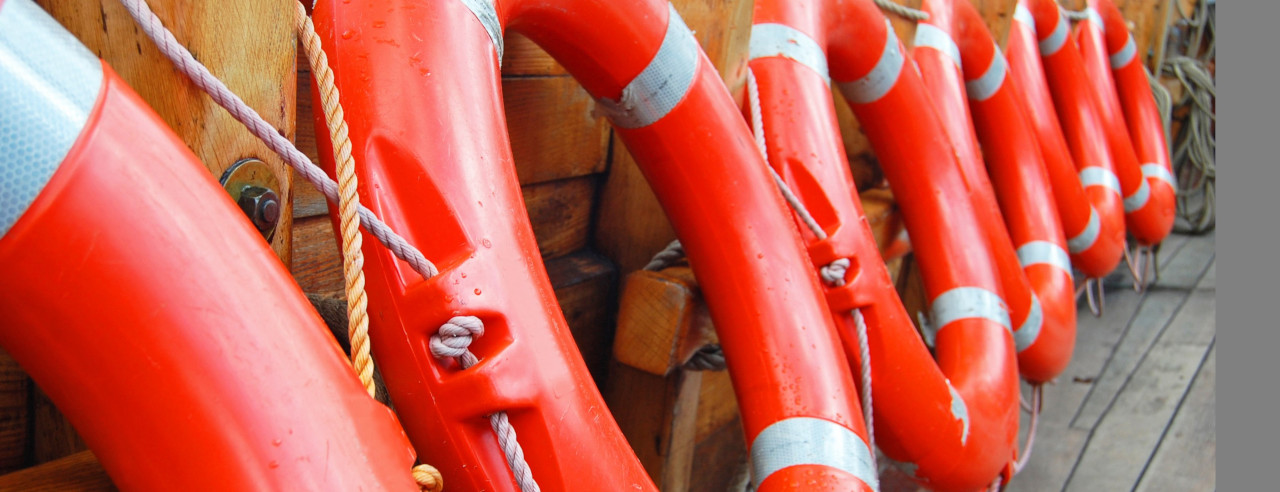
Processing conditions
Through proper process control, a defect-free artifact can be achieved. The parameters are oven temperature, heating time, and cooling rate, because each of these variables significantly affects the properties of the final product; but not only that, to make products efficiently and safely, it is necessary to use special lubricants and release agents designed for this sector and its critical issues APPROVED by top mold and plant manufacturers.