Hydrogenation process of base oils
The process of hydrogenating lubricant base oils is accomplished through a series of steps designed to improve certain properties. For paraffinic oils, these include viscosity index, oxidation resistance, thermal stability and low temperature fluidity.
Basic oil production process
Starting with crude oil, the typical process for producing a base oil is as follows:
- Separation of low-boiling materials, such as gasoline, diesel, etc.
- Distillation to isolate desired viscosity grades of base oil
- Selective removal of impurities, such as aromatic and polar compounds
- Purification to improve fluidity at low temperature
- Finishing to improve oxidation resistance and thermal stability
In general, both solvent-refined and hydrogenated base oils are produced in this way, but they differ in the type and severity of processes used.
Classification of base oils
Before examining how base oil is produced, it is important to know the American Petroleum Institute (API) base oil classification system. As shown below, API classifies base oils into five main groups. Although these groups were originally intended for the formulation of motor oils, their use has expanded widely beyond this area.
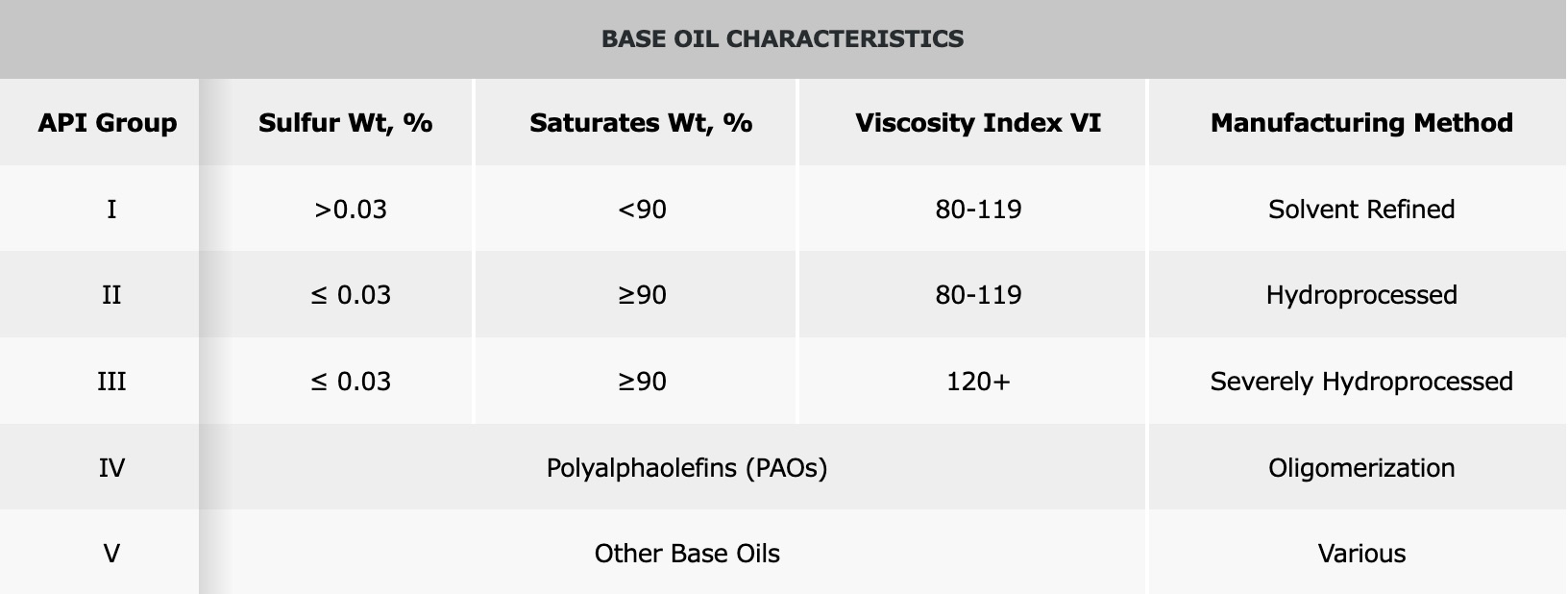
Although not officially recognized by the API, the following additional terms are often used in the industry.
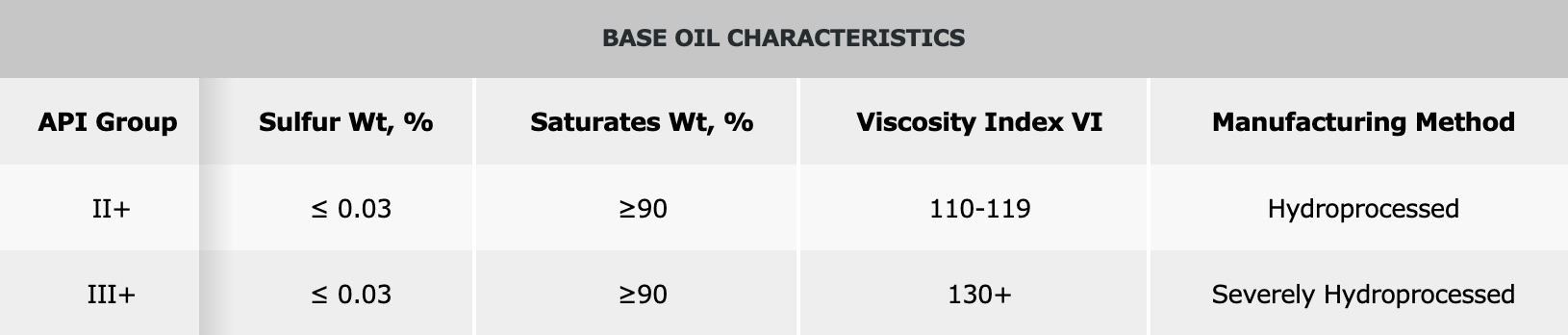
Group I, or conventional, base oils are produced by refining with solvents that contain more than 0.03 percent sulfur by weight and/or less than 90 percent saturates. Group I oils continue to be used in numerous applications because of their solvency and performance characteristics.
Group II and III base oils are produced by what API calls hydro-processing or severe hydro-processing. With a sulfur content less than or equal to 0.03 percent by weight and a saturate content greater than or equal to 90 percent by weight, they are purer than Group I base oils. Many of Petro-Canada Lubricants’ products are produced using a special high severity version of hydrotreating, called severe hydrotreating, to produce Group II, II+, III and III+ base oils.
Solvent refining process
Initially, lighter products such as gasoline, diesel, etc. are separated from crude oil by atmospheric distillation. The heavier material is then loaded into a vacuum distillation tower, where fractions of lubricant with specific viscosity ranges are taken. These fractions are then treated individually in a solvent extraction tower.
The solvent-extracted lubricant fraction is then dewaxed by low-temperature cooling. This improves the fluidity of the product at low temperature. Finally, dewaxed lubricant fractions can be finished to improve their color and stability, depending on the application requirements. A common method of finishing is light hydrofinishing.

Hydrotreatment process
The hydrotreating process removes aromatic and polar compounds by reacting the raw material with hydrogen in the presence of a catalyst at high temperatures and pressures.
Several reactions take place in this process, the main ones of which are:
- Removal of unwanted or undesirable polar compounds containing sulfur, nitrogen, and oxygen.
- Conversion of aromatic hydrocarbons to saturated cyclic hydrocarbons
- Breakdown of heavy polycyclo paraffins into lighter saturated hydrocarbons.
These reactions occur at temperatures up to 400 C/752 F, at pressures around 3000 psi and in the presence of a catalyst. The hydrocarbon molecules formed are very stable, making them ideal for base oils used in mixing lubricants. These are classified by API as Group II base oils.
The hydrotreatment process involves two steps. The first step removes unwanted polar compounds and converts aromatic components to saturated hydrocarbons. After separation into desired viscosity grades by vacuum distillation, batches of waxy lubricating base oil are cooled and dewaxed. These are then passed through a second stage of high-pressure hydrotreatment for further saturation. This final step maximizes stability by removing the last traces of aromatic and polar molecules, producing a base oil that is as white as water and 99.9 percent pure.
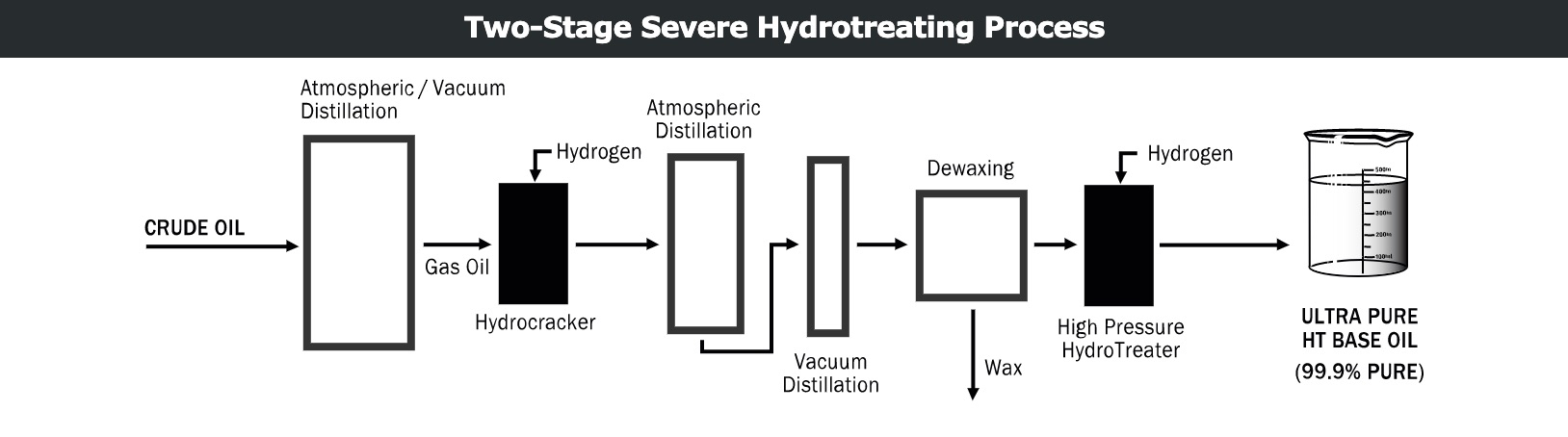
Hydroisomerization
In addition to severe hydrotreatment, the hydroisomerization process employs a specialized catalyst to selectively isomerize the wax (mixture of long-chain n-paraffins) into isoparaffinic base oil with high VI and low pour point. The process produces base oils with higher VIs and better yields than previous conventional dewaxing techniques. The process is capable of producing base oil with a VI above 130. More often, it is set to produce high viscosity index base fluids (Group II+ and III) with VI between 115 and 127. An additional feature of the process is the flexibility it offers to produce base oils with pour points below -25 C/-13 F.
Hydroisomerization is used in combination with severe hydrotreatment to produce superior base oils that have:
- High viscosity index (VI)
- Low volatility
- Excellent resistance to oxidation
- High thermal stability
- Excellent fluidity at low temperature
- Low toxicity
These characteristics give very similar performance to lubricants formulated with polyalphaolefin (PAO), the most common type of synthetic.
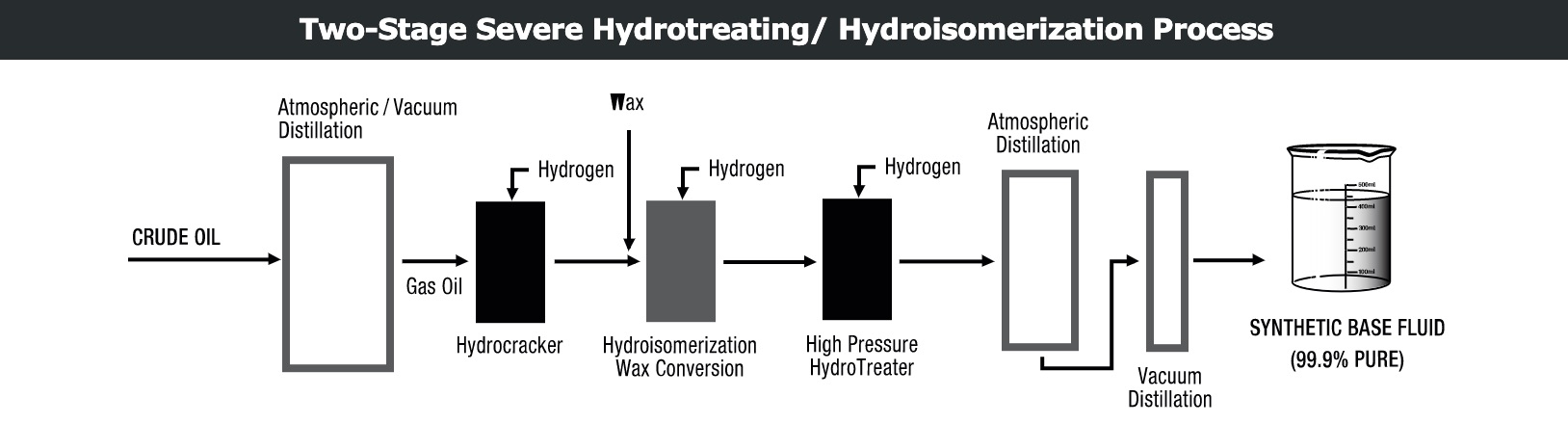
The basic properties of base oils
Base oils are critical for finished lubricants. Their composition and physical properties are influenced by the refining technology used. Formulators choose base oils with characteristics suitable for the final application and combine them with specially selected additives to optimize the performance of the finished products.
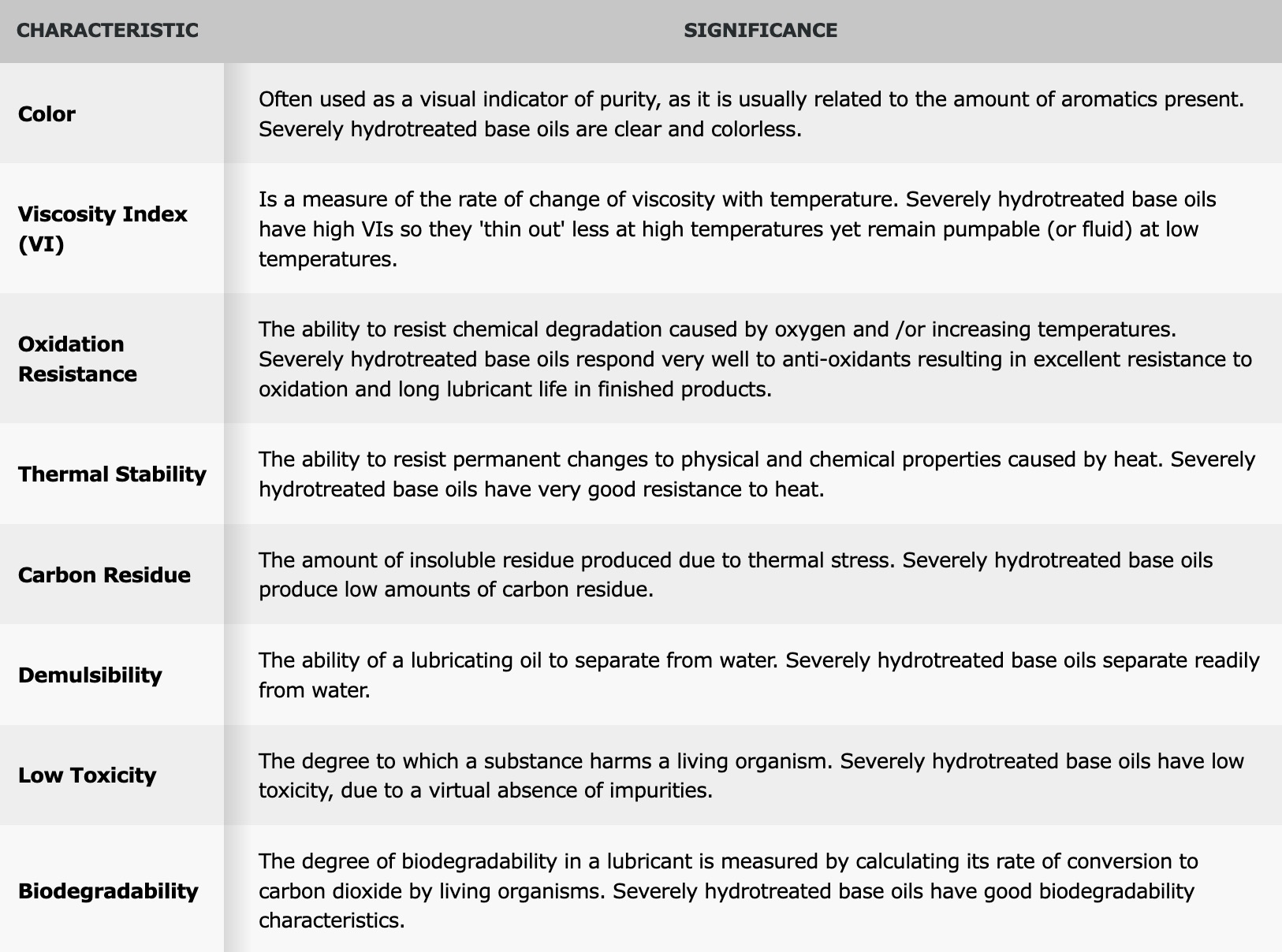