The combination of honeycomb and polypropylene makes it possible to lighten materials while increasing their mechanical properties. Nidaplast, offers a range of core materials, all of which feature a similar structure: hexagonal honeycomb with an 8-mm diameter made of polypropylene, closed by a protective plastic film and a nonwoven polyester fabric. Both the film and nonwoven fabric are heat-sealed to the honeycomb, ensuring an airtight seal between honeycombs.
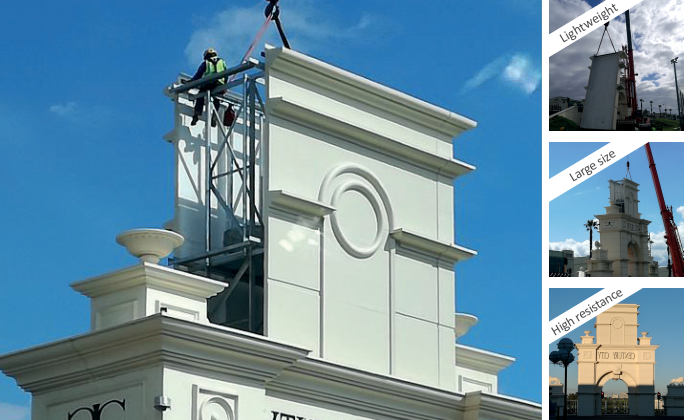
All Nidaplast materials are:
- light
- imputrescible
- impact resistant
- With good thermal and acoustic insulation characteristics
- recyclable (thus also enabling a sustainable choice).
There are many variations in the range, which may concern product density, thickness of the protective film, and even finishes.
Sandwich panels
Nidaplast cores enable the fabrication of structural and lightweight sandwich panels. The principle of the sandwich structure is similar to that of metal beams used in construction. The idea is to separate the applied skins so as to take advantage of the moment of inertia; this separation is intended to minimize added weight (a goal that is achieved by using the lightweight honeycomb structure) while increasing the stiffness of the finished panel.
Sandwich panels made with Nidaplast cores are used in many industries; not only in transportation and marine, but also in construction and different application areas.
Facade coatings
Aesthetic facade cladding, including ventilated facades, can be made, first of all. By applying reduced layers of fiberglass, aluminum, or marble (or other materials), the aesthetics of a building can be modified, with load-bearing or self-supporting structures, ensuring Extensive design possibilities for designers, offering high structural rigidity and weather resistance (wind, rain, temperature changes) and a large ease of installation.
Such a beautification operation avoids making buildings structurally heavier and allows for the recovery of pre-existing buildings, giving them a new image and aesthetic character, without affecting their solidity, thanks to the lightness of Nidaplast polypropylene honeycomb.
Panels can also be made with dimensions greater than 3.5 m2 and, in the event of rain, have greater sound insulation power than panels made with foam. The external insulation determined by ventilated facades makes it possible to create a second waterproof skin around the building, protecting it from external hazards from thermal and acoustic changes. Sandwich panels with Nidaplast effectively treat thermal bridges, protect the building from weather and moisture, and limit condensation problems; in addition, the ventilated facade reduces CO2 and heat loss.
The growing need for safety in construction, especially in the area of fire/fumes, does not limit the use of cores from the Nidaplast range. In fact, there is also a Fire Retardant version that, with the appropriate skins, enables compliance with relevant regulations.
Roofs
Roofs can also be made with Nidaplast, coupled with fiberglass and resin. The freedom of imagination for architects and designers is wide; in association with its light weight as well as its impact and weather resistance, Nidaplast is a good solution for making large self-supporting surfaces by limiting supports and allowing, thanks to the ease of shaping, to create roofs and roofing with a new and refined design.
Doors
The Nidaplast range is not only applied to the exterior of buildings but can be used in a variety of ways. Both exterior and interior doors can be made with Nidaplast used as the core material. Especially for the external ones, not only does it improve the weather resistance (or at any rate to water and humidity: think of sports centers), but it also reduces the bilamin effect, which occurs when there is a large temperature difference between the inner and outer frame (due to intense solar radiation).
In this case, the frame expands and may cause distortion of the door or difficulty in closing and opening. The light weight of the door avoids stress problems at the hinges and frame, and the presence of Nidaplast on the outer side contributes to greater resistance to impact and vandalism. Although covered with a skin (wood, aluminum, plywood), doors made with Nidaplast cores are lighter and easier to move; they also provide additional functions such as vibration damping and good thermal and acoustic comfort.
Interior
Nidaplast sandwich panels find application as interior partitions, whether for toilet and locker room partitions, which require water and moisture resistance, fixed walls, which must stand the test of time, or removable or movable walls, which are easy to move and dismantle.
Elevators
Elevators are necessary in buildings: the Nidaplast honeycomb core sandwich panel is an ideal product that enters the process of their manufacture and renovation, responding to technical and mechanical problems. Its low weight increases the number of authorized users in the elevator and reduces the energy requirements for system operation. IIts self-supporting character allows mechanical reinforcements to be contained as much as possible. The sandwich panel offers light weight, water and moisture resistance, acoustic and thermal insulation, and mechanical performance.
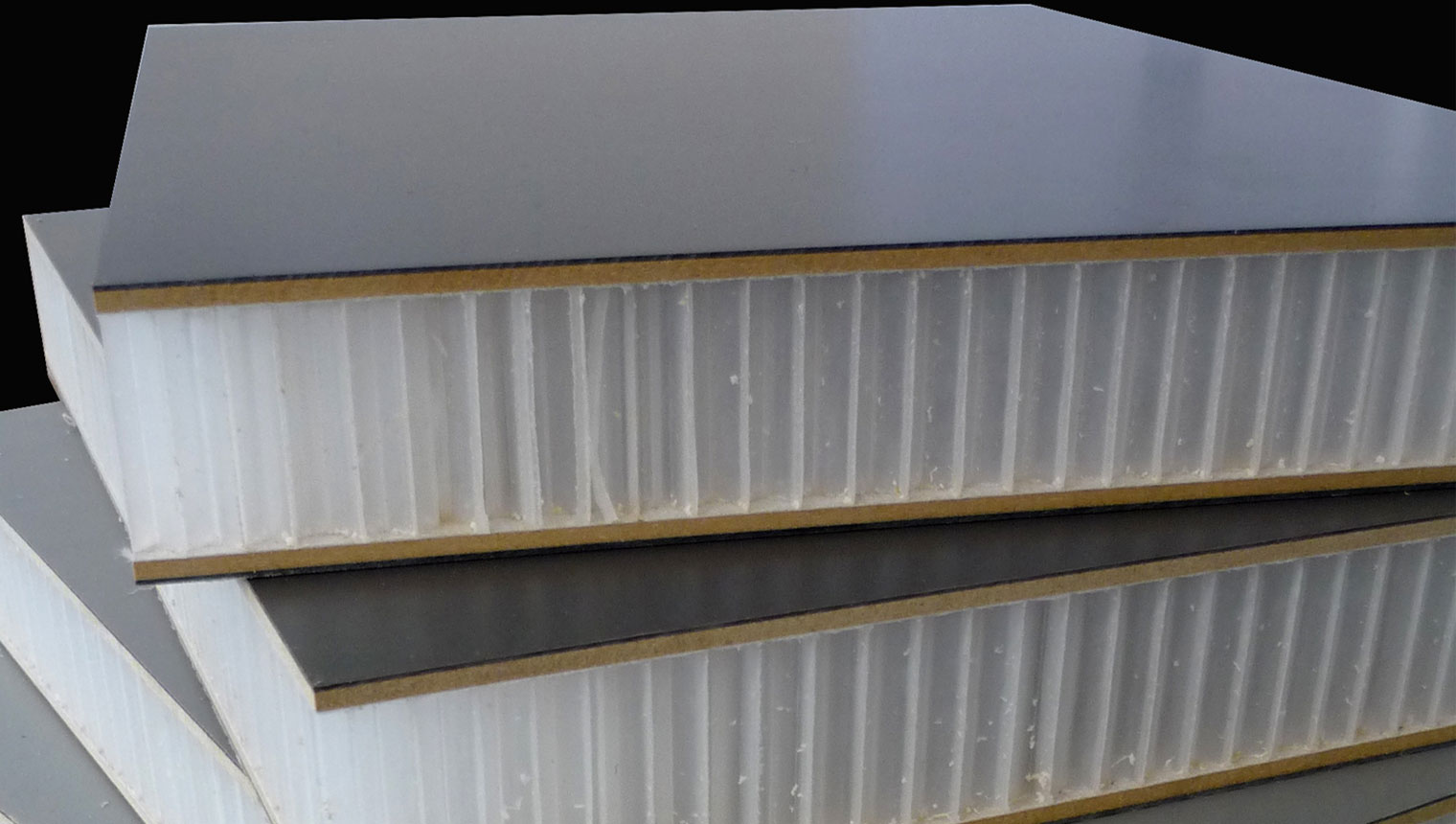
Flooring
Considering flooring, Nidaplast can be used as a substrate equipped with acoustic insulation or as a shock absorber for flooring in buildings under construction or renovation by applying, for example, lightened marble. This allows for an aesthetically perfect result, avoiding the waste of stone material.
Nidaplast is translucent, when backlit, with most marbles: this allows designers to create even sophisticated interiors with distinctive aesthetic effects. Nidaplast polypropylene honeycomb panels are often used to set up sports flooring suitable for multipurpose halls (basketball, handball, volleyball, badminton, table tennis, skating, dance). In combination with other materials (foam, wooden floor), they contribute to good shock absorption (balls, falls, jumps). In addition, depending on the condition of the supporting soils, the honeycomb will allow soil defects to be erased.
A classic application of core is the floating floor, which consists of a series of panels or tiles placed on uprights, which in turn rest on a floor placed at a lower level. The height of these supports is generally adjustable. This type of floor system is very common in offices, businesses and any space under which there are multiple electrical cables, pipes, heating and air conditioning ducts, crawl spaces, etc.
Prefabricated bathrooms
If we consider the need for the presence of electrical cables and pipes, but in a vertical direction, Nidaplast is often used in the construction of prefabricated bathrooms. Tiles are applied in an industrial manner on Nidaplast panels, with the necessary finishing touches. The four walls, along with the floor, are delivered stacked on top of each other, so as to set up a bathroom in short time, with excellent results at the aesthetic level but, more importantly, at the maintenance level; in case of problems (water leakage, for example), not only will the panel resist contact preventing the formation of mold, but will avoid the need for masonry work: simply remove the panel and perform the pipe repair. Many hotel chains have chosen this solution.
Furniture
When it comes to building furnishings, Nidaplast panels are often used as supports, to reduce the weight of natural or artificial stone kitchen countertops, while maintaining the characteristics of strength and rigidity. Home, office or store furniture can be made. The good mechanical properties, excellent dimensional stability of sandwich panels, made with the Nidaplast honeycomb core, can be combined with decorative laminates of all kinds to set designers free in the realization of their creations. In the already finished version with the skins previously glued to the core (Nidaskin), or in the single core version (Nidaplast, Nidapan), all possibilities are available. It is also possible to make designer furniture from concrete, for a lighter, more portable but equally solid version of the same.
Swimming pools
Finally, in the most elegant buildings in cities but also in country or seaside homes, the demand for swimming pools is growing. To ensure the strength of bottoms and walls, which are stressed by very high internal and external pressures, as well as by stratum pressure, Nidaplast cores can be used as vertical and horizontal support reinforcements.
The honeycomb sheets combined with the polyester structure of the pool will play their role as levers or compensating arms as soon as the pool is filled with water, also eliminating the drum-skin effect at the bottom. In fact, with the help of the water pressure exerted on the bottom, the walls, maintained by these reinforcing structures, tend to push inward, creating a counterthrust that cancels the lateral pressure of the contained water. Horizontal reinforcements provide a rigid connection between each vertical reinforcement element and thus prevent any horizontal bending. Thanks to the stiffened bottom, which makes the final product less fragile, it is also possible for the pools, during construction, to be stacked, facilitating logistics.