Heat transfer fluids, such as thermal oil, inevitably undergo degradation over time. However, it is possible to delay deterioration and extend its useful life through proper management. This article will provide some practical advice on how to keep the heat transfer fluid in good condition and maximize system efficiency.
The heat transfer system is designed to remove thermal energy from a heat source using a heat transfer fluid. The system and its components are sized according to the physical properties of a new, uncontaminated fluid. Therefore, the ability of the system to maintain high performance depends on keeping the fluid in good condition.
The challenge for system operators is to keep the heat transfer fluid, which is the beating heart of the system, as close to its initial condition as possible. Without proper care, heat exchange surfaces can become dirty, increasing the amount of energy required to maintain the desired temperature and thus reducing system efficiency.
As the heat transfer fluid degrades, its initial properties change and continue to change as the severity of degradation increases. So, the question becomes: how to keep the system as efficient and productive as when first filled, despite the gradual deterioration of the fluid over time?
In this article, we will try to answer this question. Although no expert can keep diathermic fluid in perfect condition forever, system operators can certainly extend its useful life by avoiding common threats of degradation and selecting the most suitable fluid for the application.
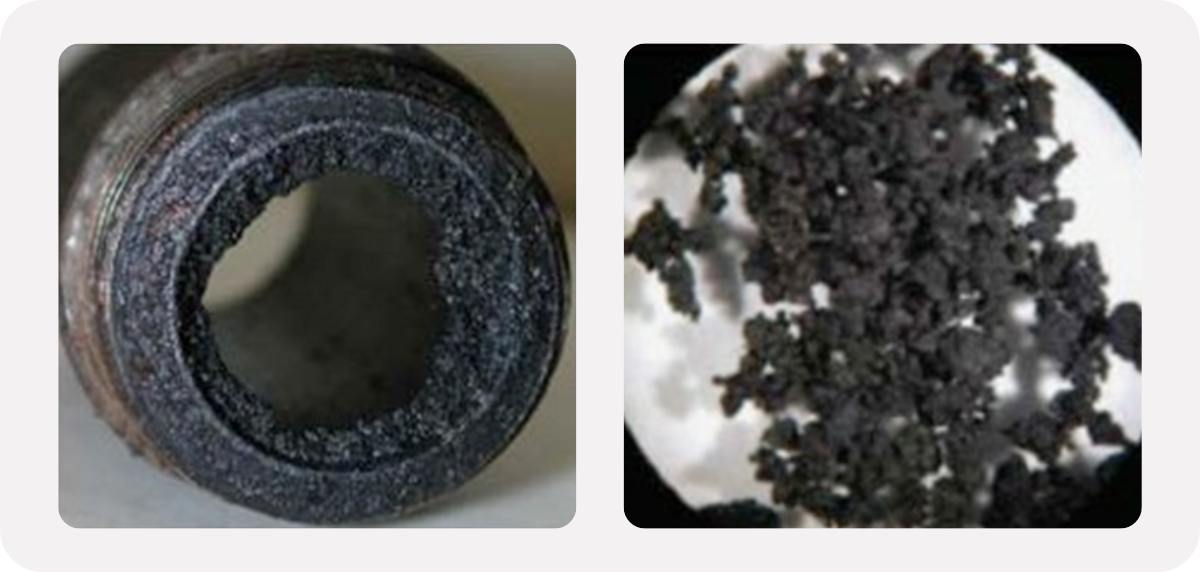
The most common causes of heat transfer fluid degradation
Before examining strategies to extend the useful life of the fluid, it is important to understand the main causes of its degradation. The three main causes are:
Thermal degradation or cracking
This phenomenon occurs when fluid molecules receive more heat energy than they can absorb. In organic-based fluids, such as mineral oils or chemical aromatic compounds, thermal cracking causes the breaking of chemical bonds within fluid molecules. This leads to the formation of carbon-like residue that can clog the system and cause damage to seals and electrical elements. Some strategies to extend the useful life of the heat transfer fluid are:
- Selection of the appropriate heat transfer fluid: It is important to select a fluid with high thermal stability and resistance to degradation. Mineral fluids formulated with hydro-treated white oils are known for their higher thermal stability than conventional mineral oils.
- Proper venting: To avoid residue accumulation, proper venting of the system is necessary to release light, volatile hydrocarbons formed during thermal degradation.
- Proper startup and shutdown procedures: It is important to follow proper procedures for starting and shutting down the heat transfer system. Starting up too quickly or shutting down improperly can drastically reduce fluid life and affect system efficiency.
- Heat flow monitoring and control: It is essential to monitor and control the heat flow in the system to detect any abnormalities that might indicate ongoing degradation. In this way, early action can be taken to prevent greater damage to the fluid.
- Regular maintenance of pumps and filters: Proper maintenance of pumps and filters helps prevent the accumulation of debris and ensures efficient operation of the system.
- Use of fluid analysis: Monitor fluid regularly through laboratory analysis to detect early signs of degradation and take prompt action to correct any problems.
Oxidative degradation
This type of degradation occurs when the heat transfer fluid reacts with oxygen in the air. Oxidation is mainly affected by temperature, and an increase of 10°C doubles the oxidation rate. Oxidation causes discoloration of the fluid, increased viscosity, and formation of insoluble compounds and dirt.
Addressing oxidative degradation requires specific measures:
- Cover with inert gas: In closed systems, inert gas such as nitrogen can be introduced into the expansion tank to eliminate oxygen and prevent fluid oxidation.
- Selection of fluid with oxidation inhibitors: It is advisable to select a heat transfer fluid that contains oxidation inhibitors. Oxidation inhibitors react with free radicals and oxygen compounds to prevent fluid degradation.
External contamination
External contamination can result from such things as condensation, foreign liquids, and air entering the system. These contaminants can impair fluid efficiency and cause problems with corrosion and dirt accumulation.
To prevent external contamination, the following measures can be taken:
- Investigation and resolution of contamination cases: It is important to investigate and resolve contamination cases by reporting the problem to the fluid supplier for advice on management and possible impacts on oil and additives.
- Use of oil filters: Installing oil filters helps collect solids and monitor deposits to detect problems in the system.
In conclusion, choosing the correct heat transfer fluid and adopting good maintenance and monitoring practices can help to significantly extend the useful life of heat transfer fluids. Preservation of fluid properties and system efficiency depend on the attention given to preventing thermal and oxidative degradation and managing external contamination.