SAERflow®: Products for improved production and environmental performance in the marine industry.
As a result of steady growth in the marine industry, the need to make large composite parts quickly and without waste using the infusion process requires constant attention to molding methods, the quality of materials to be used, and environmental protection.
With this in mind, SAERTEX® has created a product that meets all these objectives: the SAERflow®. It is a biaxial fabric (+/-45°), made of fiberglass and to which a synthetic material is added; the latter makes the product incompressible in the vacuum stage. Being draining, SAERflow® allows excellent resin flow during infusion and replaces traditional drainage nets. When placed in the center of the fabric layering and not on an outer face, it also avoids the creation of preferential resin diffusion pathways.
One layer of SAERflow® allows resin diffusion at a standard rate (equivalent to a drainage net) in parts with thicknesses of 8 to 10 mm. The use of multiple layers of SAERflow® in the same lay-up allows for optimal infusion and faster resin diffusion in thick monolithic parts such as deck or hull molds.
While a conventional infusion process requires the use of an outer drainage mesh, a microperforated film, and a peel ply underneath the film for vacuum, the innovation of SAERTEX® is to use only the SAERflow®, which remains in the final part. Eliminating the vast majority of peripherals and consumables, the boat builder drastically reduces its own waste and environmental impact: in fact, it achieves a purchase cost savings e storage of consumables, on the time it takes to remove them from the layer and their disposal cost.
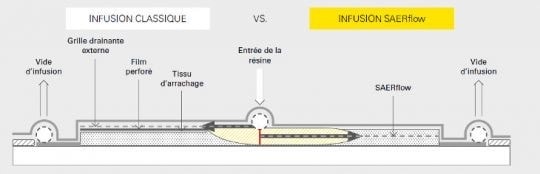
SAERflow®: A double structural and ecological advantage
Consisting of a 300 g/m2 biaxial, SAERflow® can be taken directly into account when calculating the structure of the boat. SAERTEX® also offers SAERflow® as a combination with NCF of various weights and fibers such as carbon or aramid fiber. For example, combining SAERflow® with a 600 g/m2 0/90 yields a standard four-axial product of about 900 g/m2 self-draining, which fully meets the needs of the marine market compared to a more traditional 800 g/m2 QX.
Boats produced faster and more economically
SAERflow® enables the boatyard to save money by implementing the infusion process. Beyond the savings in time and money achieved by eliminating the removal and disposal of consumables, the drapability of the material allows for increased productivity. With a shape-fitting ability comparable to normal tissue, SAERflow® is easier to place than infusion drainage nets, achieving time savings of up to 50 percent.
Not only that, SAERflow® is a very useful tool for boat builders who want to make the transition from the manual layering process to the closed mold process.
Other solutions
SAERTEX®’s activities aimed at improving production and environmental performance are not limited only to the SAERflow® proposal: other SAERTEX® solutions meet these ends.
SAERfix® is an adhesive that makes any SAERTEX® fabric self-adhesive, eliminating the storage, use and disposal of spray cans. Easy to handle, it enables quick and accurate deposition of fabric, preventing it from slipping on the mold. The adhesive, which is soluble in resin, allows in case of error, removal of the fabric and its correct repositioning. The time savings are obvious. But SAERfix® is also environmentally friendly: not only does it avoid polluting the working environment due to the use of canisters, but as far as water pollution is concerned, it is considered absolutely harmless.
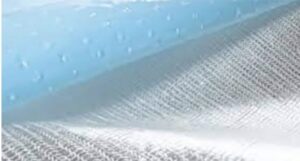
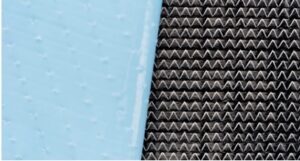
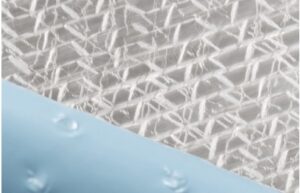
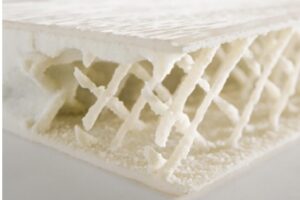

SAERfoam®, core material with a three-dimensional structure, as it features a PU/PE/PIR core combined with 3D glass fiber reinforcements, absorbs less resin than PET foam, is easier to cut and can be supplied in KITs (all products in the SAERTEX® range can be supplied in kits), by eliminating i disposal costs Of scraps. SAERcore® is SAERTEX®’s range of patented products for closed mold injection processes such as RTM (Resin Transfer Moulding) and RTM light, together with infusion processes.
SAERcore® is a complex sewn (optionally glued) sandwich that, in its basic version, consists of one or two layers of short-fiber mat CSM) and a core of PP (resin flow zone). Initially, the resin flows horizontally into the core material and then impregnates the outer reinforcements through vertical injection. This “two-stage impregnation” process saves a considerable amount of time, as the flow optimizer causes extreme acceleration of horizontal injection along the entire width of the component. External reinforcements can be freely adapted and optionally include one or two layers of mat. Again, CSM fibers are freely selectable. SAERTEX® multiaxial technology is integrated into the SAERcore MAX® product, which means that the sandwich complex is further reinforced by combining multi-axial textiles.
SAERcore® and SAERcore MAX® not only save time in terms of resin flow rate: both product variants are available in combination with SAERfix® or an additional nonwoven coating to achieve an optimal surface appearance for the finished component. Both products feature excellent drapability, which saves tremendous time (labor and cycle time) as a single layer. Finally, SAERTEX®, in addition to weaving NCF fabrics in glass, carbon, aramid and basalt fibers, is creating a range of linen fiber fabrics to meet the increasing market demand for natural fiber fabrics. Lighter boats that consume less fuel and create less waste during their manufacture: these are the reasons for SAERTEX® for innovation in composites and environmental protection, to not only make production more efficient and faster, but to achieve economic benefits and to increase environmental sustainability in the marine industry.