The weight of the battery in electric vehicles requires stronger body structures, including the lower part of the chassis (sill). In electric vehicles, this part has a higher specific mass than in combustion vehicles because of functional and design requirements, including supporting the weight of the battery pack.
The frame is usually made of a multilayer structure that is bonded with structural adhesives to increase its strength and durability.
Structural adhesives require specific heating times, typically in the hot paint process, to gain adhesion and mechanical strength.
Below we present a case study applied to the world of Mercedes electric vehicles.
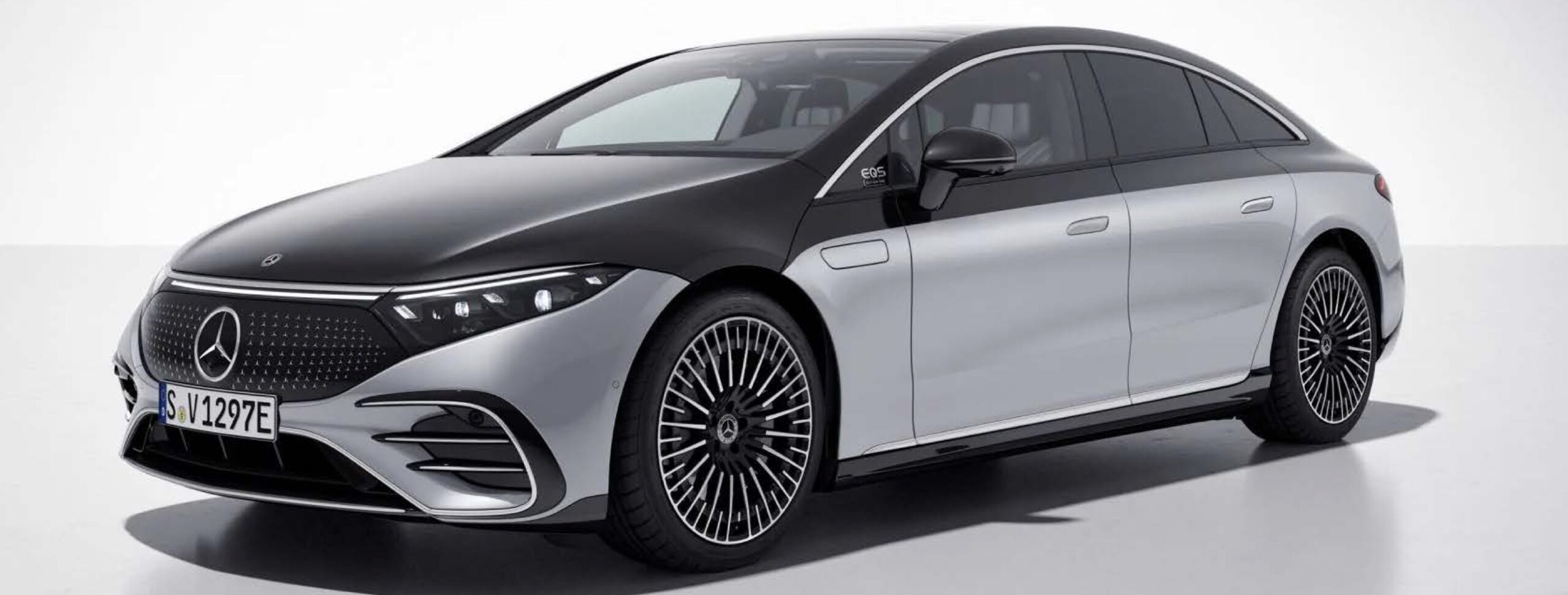
The challenge
For the next-generation electric vehicles, Mercedes used a multi-layer structure of steel and extruded aluminum adhesively bonded for the chassis. This structure had an insulating effect that adversely affected the adhesive strength and curing properties when applied in body shop and subjected to the processes of e-coating.
Mercedes turned to DuPont, a longtime supplier of adhesives, to develop a new structural adhesive with a lower cure temperature window.
The solution
DuPont has responded to the challenge with its newest development, the broad-bake adhesive BETAMATE™ 1650. More than sixty years of experience in adhesive technology enabled DuPont to be first to market with the new solution quickly.
Structural adhesives generally have a curing window between 165°C and 200°C. Mercedes requested a wider window with a specification of 150°C for 15 minutes. BETAMATE™ 1650 has been tested and validated to operate between 150°C and 200°C, easily meeting the demands of Mercedes.
These were the other requirements that DuPont had to meet:
- Membership
- Mechanical strength (lap shear, T-Peel, and dynamic impact)
- Corrosion protection (loss of strength ≤30% after aging)
- Washing resistance
- Resistance to open weather/moisture
- Application with existing technology/equipment existing equipment
- Shelf life of 6 months
BETAMATE™ 1650 broad-bake adhesive exhibits lap shear strength within 150°C at 15 minutes.
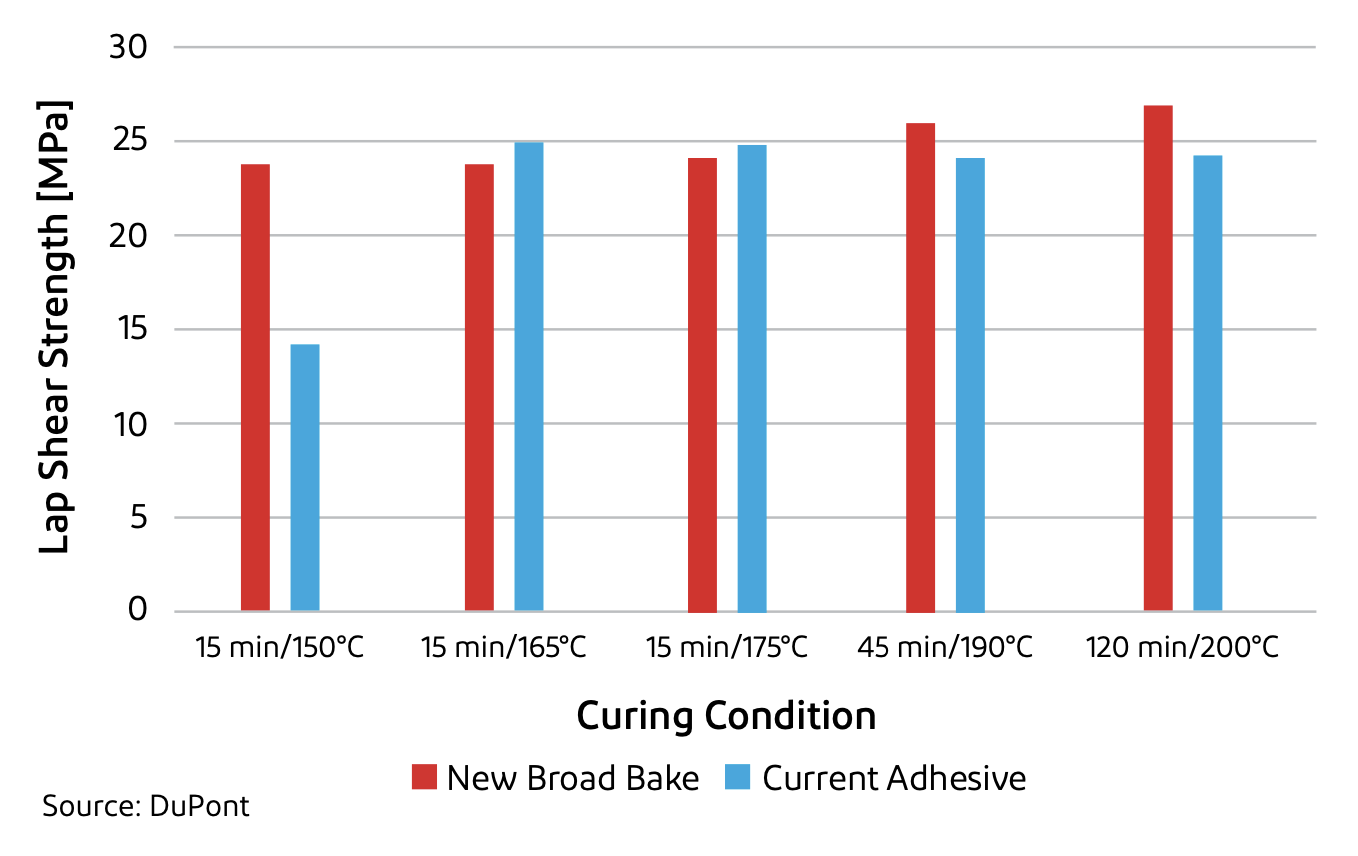
Result
The new adhesive achieved the desired curing condition, which enabled mechanical performance in shear, impact, and T-peel strength, and demonstrated 20% longer fatigue life than other structural adhesives.
BETAMATE™ 1650 also met moisture resistance requirements even after 10 weeks of VDA 621-415 corrosion test. In addition, in response to a secondary requirement for long shelf life, DuPont also provided a shelf life of six months from the time the product leaves the warehouse.
The newly developed BETAMATE™ 1650 broad-bake adhesive offers significantly greater shelf stability than six months at 30°C. The slow increase in viscosity at nozzle temperature allows for a robust application process.
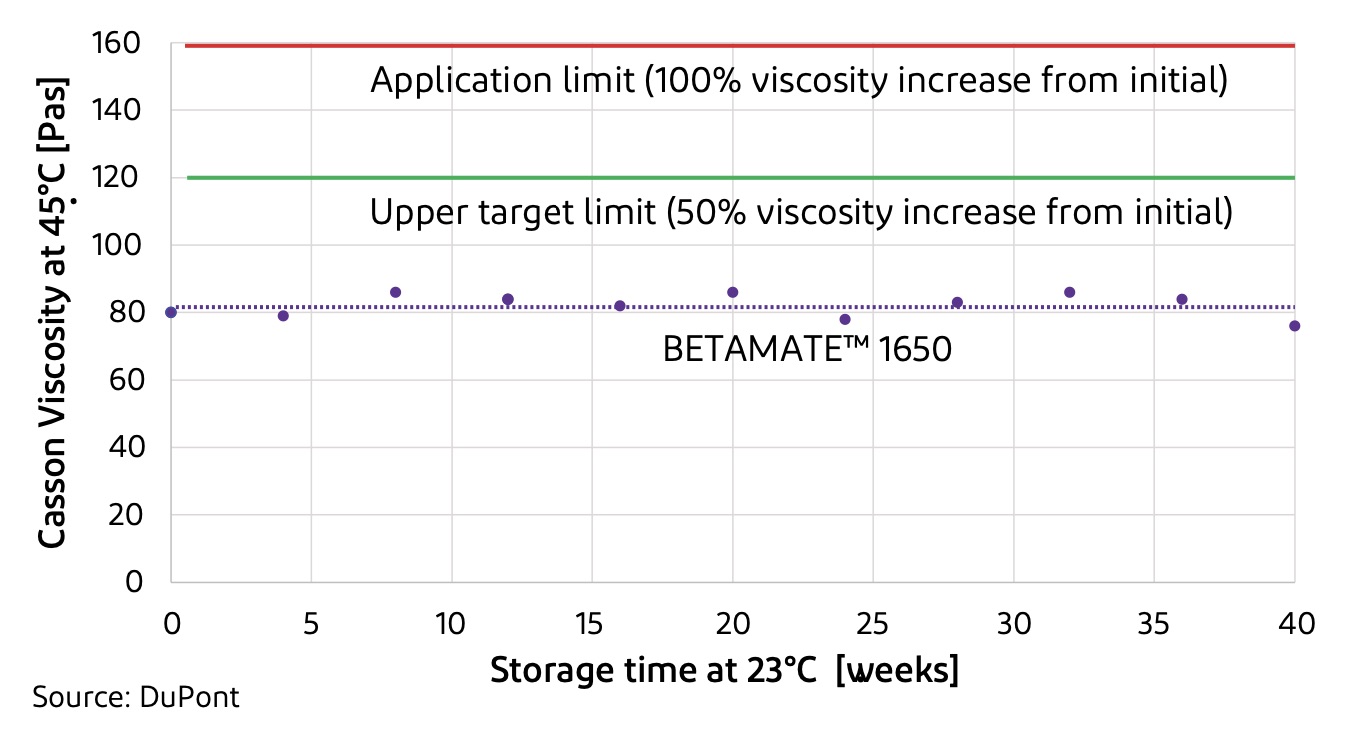
Sustainability benefits of BETAMATE™ 1650 broad-bake adhesive.
New broad-bake adhesive technology enables automotive manufacturers to durably bond electric vehicle body structures using a one-component body adhesive that withstands a wider curing window. This includes temperatures that can be reduced by 20°C from the current standard (160°C). The current minimum curing temperature is 12 minutes at 160°C (object temperature and holding time), while the released curing window ranges from 15 minutes at 150°C to 45 minutes at 190°C.
This technology reduces the need for sustained oven temperatures for e-coat, thus saving energy. This adhesive technology-which has a shelf life of at least six months-also demonstrates excellent resistance to environmental exposure and offers a high elastic modulus and tensile strength that help improve passenger safety while maintaining the quality and durability of the bonding throughout the life of the vehicle.