How to choose the right gear lubricant
Why is it important to lubricate gears?
Gears and gearboxes have been a popular method of power transmission since the beginning of the Industrial Revolution. In general, gear drives are one of the most economical alternatives in applications where bothhigh load capacity and long life under high loads are required.
Mills, dryers, or shovels are just a few examples of industrial applications where these mechanisms are present. The amount and nature of sliding between teeth in contact with each other,have an important effect on the necessary requirements of the lubricant used.
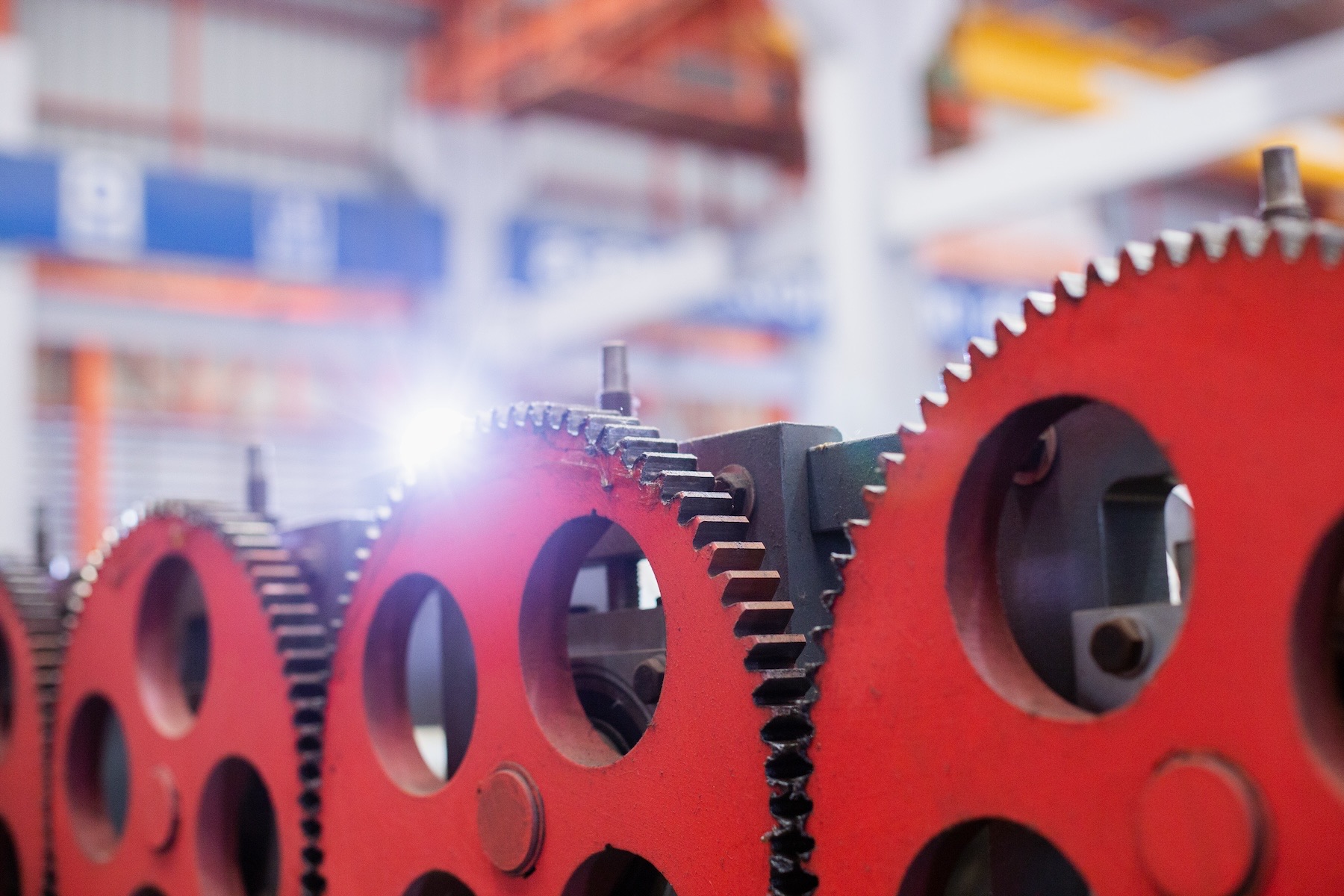
How a gear works
Sliding occurs more actively when the teeth first make contact. When they disengage, the tips of the respective elements develop a small scraping action on the sides of the adjacent teeth.
Both rubbing and compression can occur at this stage. When the teeth engage more, the rolling contact becomes more pronounced. Lubricant rubbing or scraping is less likely to occur under these conditions, but squeezing is still possible, especially since contact pressure is highest during the period when the teeth are engaged.
In addition,wear will occur more rapidly at the tips and roots of the teeth due to sliding friction, while the intermediate surface of the teeth adjacent to the pitch line, being subjected to rolling action, will resist wear more effectively.
Because of the low speeds, the very high torques to be transmitted, and the barely attainable hydrodynamic conditions, the tooth flanks of the gears are at serious risk of damage.
In addition, surface deformations related to high temperatures and loads, inaccuracies in the adjustment of parts within the mechanism,insufficient lubricant supply, or even a wrong choice of lubricant can often lead to the same results. The choice of an appropriate lubricant is therefore critical.
What parameters are important in choosing an appropriate lubricant?
Gear applications are strongly affected by the lubricant used. Typically, these mechanisms operate at low rotational speeds and/or heavy loads. However, newer designs of industrial equipment require gears to transmit higher and higher loads. Therefore, the following points are some of the most sought-after characteristics in a gear lubricant:
- Excellent adhesion properties
- High resistance to runoff and splashing water
- High load capacity, protection against wear and friction
- Protection againstwear and corrosion
- Noise and vibration reduction properties
- Sprayability and/or ease of distribution
- Additional properties, such as drainability or fling-off resistance.
What lubrication options does the market offer?
Currently, pastes and greases offer the best solutions to the most common problems encountered in this type of application. The pastes contain mineral base or synthetic oils of medium to high viscosity.
They may also contain a thickener, solid lubricants (such as MoS2 or graphite), rust inhibitors, and extreme pressure agents. In particular, extreme pressure agents prevent the welding of metal surfaces. In addition, the pastes produce a thick semi-dry working film that separates the gears during gearing and does not accumulate in the gear roots except under high temperature conditions.
In addition, the paste can be used in moderately dirty and dusty environments without fear of the formation of abrasive compounds. Greases, on the other hand, are sometimes preferred when high-temperature conditions prevail or when leakage of a thinner lubricant could contaminate materials being processed. Mascherpa offers a wide range of products
lubricants for closed and open gears
, offering major brands internationally.