The corrugatedindustry plays a vital role in the modern world, supporting multiple economic sectors and employing a wide range of products.
With decades of experience in sales
Krytox
for the lubrication of corrugator cylinders, a package of lubricant products (greases, oils, and coatings) has been developed that allows production lines to achieve them maximum performance, with the best quality, and significantly reduce overall maintenance costs.
1. Preheaters – Ondulators.
The corrugator unit (or backhoe) in corrugated board production is definitely the component that presents the most critical issue on the selection of the suitable lubricant, as the high operating temperature combined with the presence of steam means that special lubricants suitable for continuously sustaining such harsh conditions for a long time. The same argument can be made for preheaters although under less critical operating conditions.
The product that has been used in this industry for more than twenty years is undoubtedly the fat
KRYTOX CORR 226 FG
which, by the way, is approved by most of the world manufacturers in the industry. This aspect is certainly a guarantee of optimal performance on any type of corrugator.
The special chemical nature of the product makes it compatible only with products having the same PFPE/PTFE composition.
Finally upon completion, the product is approved by the U.S. NSF class H1 for incidental contact with food, so it can be used indifferently for cardboard for common use and for cardboard intended for food.
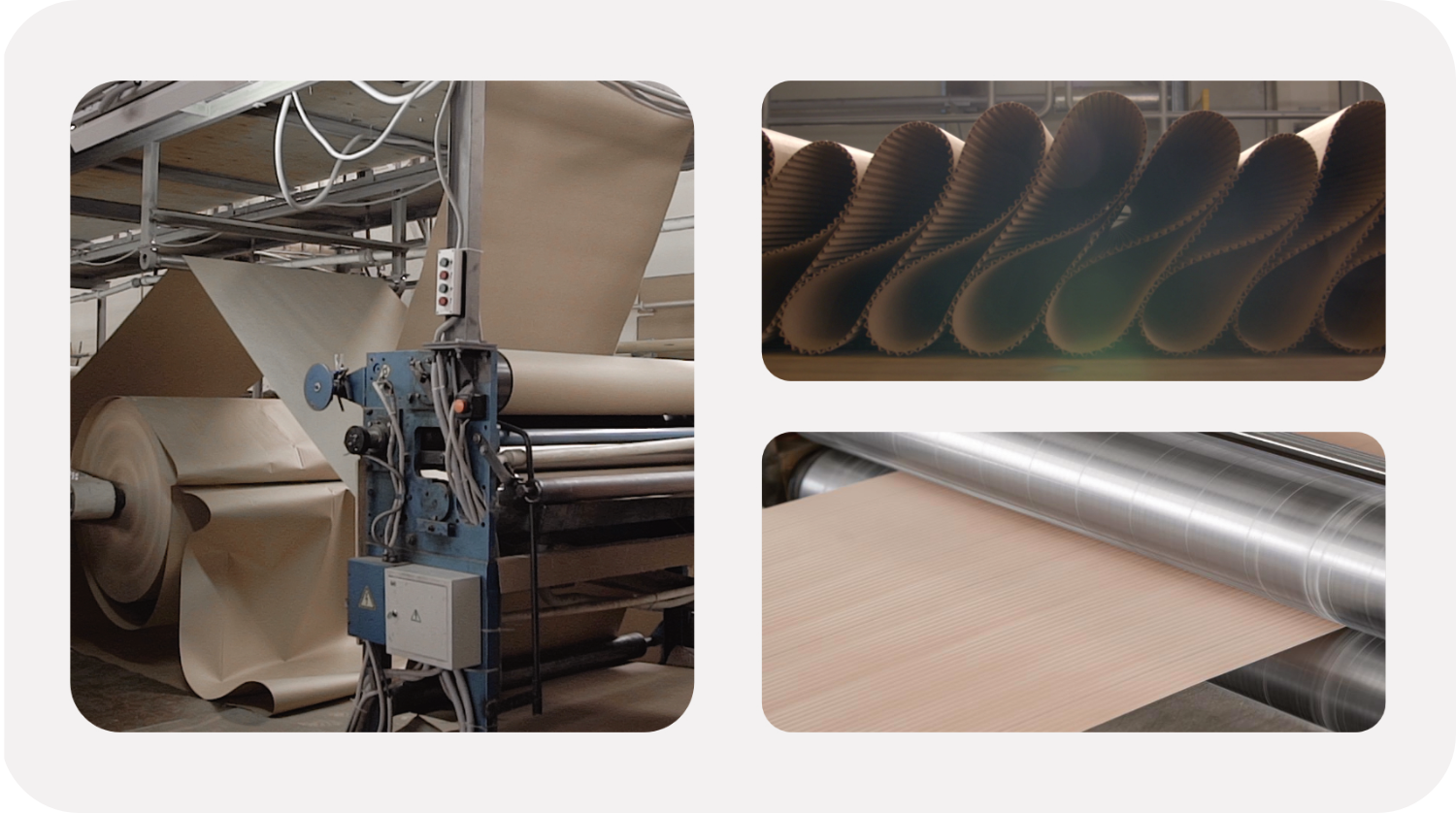
2. Warm Plans
The lubrication of the hot plates is related to the presence of rolling elements that regulate the movement of the corrugated board.
The presence of heat and steam, albeit in smaller quantities than in the corrugator unit, requires the use of lubricants that are stable not only to the temperatures but also to the moisture that is created during the drying of the board.
Very common is the use of lubricants that absorb moisture and thus become damaged and ineffective; this situation makes rolling elements particularly weak.
The products we offer for this application are specially designed to withstand loads, high humidity and high temperatures.
Finally, it is also possible to supply for the same application products approved by the American NSF class H1 for incidental food contact.
3. Coupler – Gluer
One of the major lubrication issues of the bonding and coupler assembly is to ensure frequent and regular lubrication to the rolling elements.
The choice of suitable lubricant, while very important, plays a secondary role to that of ensuring the continuous supply of grease to the bearings. In this way, any damage to the bearing due to excess or defective lubricant to the bearing can be avoided, the latter condition being particularly dangerous if the grease is unable to withstand well the moisture present. Products approved by the US NSF class H1 for incidental food contact can also be supplied for the same application.
4. Corrugator Roller Cleaning
During the production of corrugated cardboard, starch residues, glue and cardboard dust are deposited on the corrugator roller; dirt is also deposited on all rollers (including non-operational rollers). All of this results in the need for roller cleaning at the “wave change.” The technologies currently used for cleaning the corrugator roller can be many: from standard industrial oil to solvents of various kinds.
Such lubricants/solvents have as their main disadvantage that they create considerable smoke when applied to surfaces at high temperature, as well as leaving deposits or sludge from carbon residues.
In addition, if cardboard intended for food contact is produced, it is mandatory to use lubricants that are certified for accidental contact with food ( NSF class H1 standard), and industrial oils/solvents certainly do not meet it.
The product we propose for this application is an extremely pure product that allows for no fumes and unwanted odors during use, along with a high detaching and cleaning effect. It is also certified for both accidental (NSF H1) and prolonged (NSF 3H) food contact.
5.1 Axes Translation Cut Cordon
A particularly acute problem is the deposition of cardboard dust on the translation axles of the cord cutters. Currently, unblockers are used that solve this problem to a limited extent. The product we propose is called Emax AS 103 and has a low viscosity perfluoropolyether base and prevents, due to its dry release characteristics, the formation of cardboard dust deposits, promoting smooth displacement.
5.2 Scrap Transport Chains
The suitable lubricant for scrap transport chains in corrugated board production should avoid the following classic problems:
- Paper dust soiling
- Poor resistance to loads
- Poor penetration
The right product is MOLYKOTE OMNIGLISS, based on mineral oil with detergent additives, adhesives and solid lubricants to promote load resistance.
6. Cut Cordona
During the production of corrugated cardboard, starch residues, glue and cardboard dust are deposited, which can affect the perfect functioning and durability of the cutters. There are different solutions to this problem through the use of lubricating oils as release agents.
Whether mineral, synthetic or silicone based these oils must be chosen appropriately so as not to smear the board or create the opposite effect of being a receptacle for all impurities in the environment.
In addition, in the case of board intended for use with food, it is preferable to use lubricants certified for food use by the U.S. NSF class H1.
7. Transverse Cutter / Cut-Off
Medium-viscosity lubricating products, either mineral-based or synthetic, are generally used in the cross cutter.
Lubrication is carried out to reduce the high friction present in the cutting zone.
By using low-purity or reclaimed products, oily mists can also form due to the friction caused by the blades against the cardboard, which are harmful to operators.
One of the main issues is the contamination of paperboard intended for food contact where the use of unsuitable products is a potential cause of rejection of the article itself.
In addition, in the case of board intended for use with food, it is preferable to use lubricants certified for food use by the U.S. NSF class H1.
We offer different solutions for this application in terms of lubricant, but all based on high purity of base oil and incidental food contact certification (NSF class H1).
Download the informational PDF
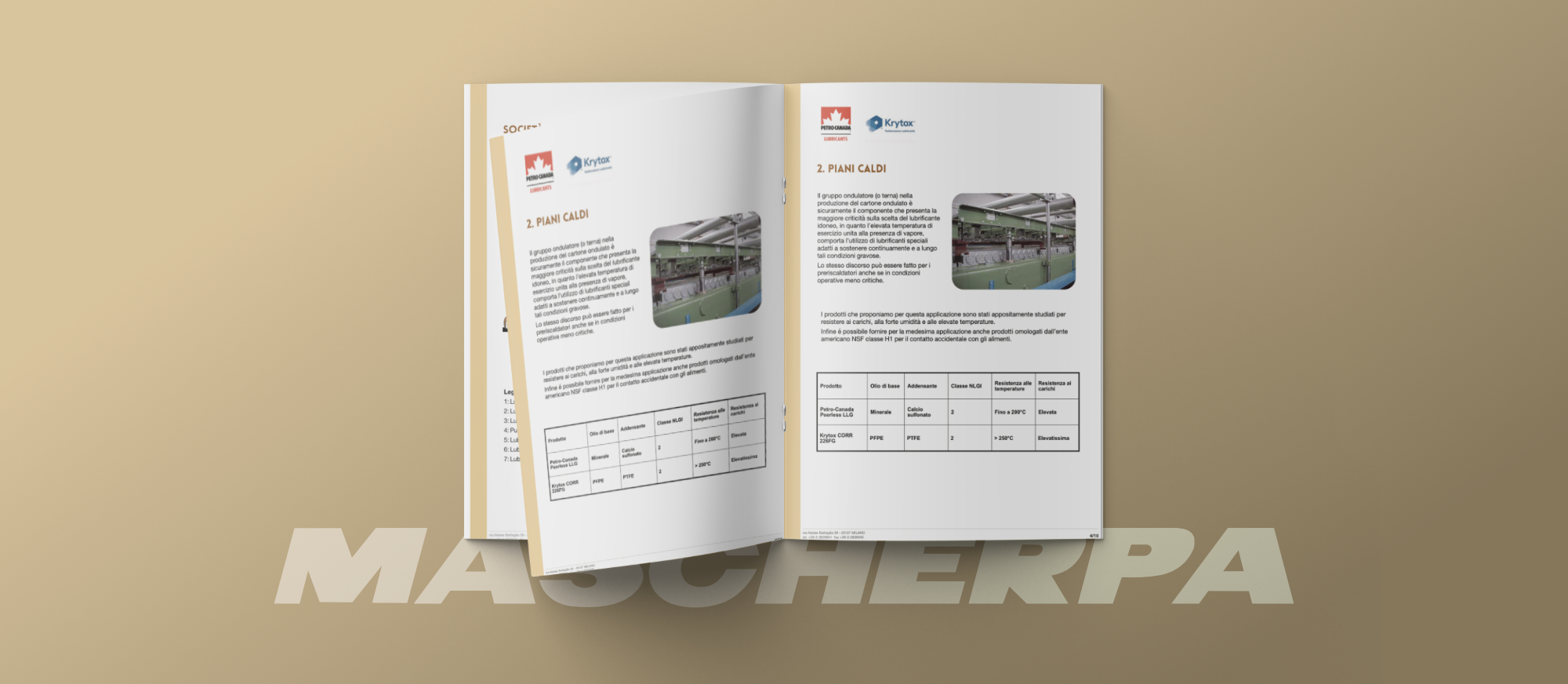