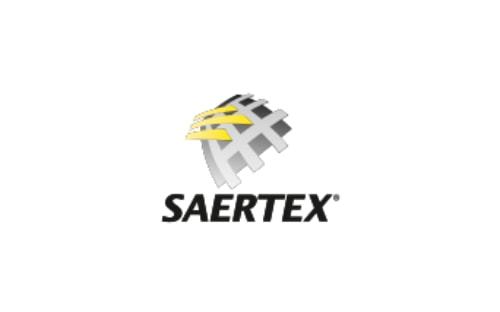
The SAERflow fiberglass drainage fabric.
SAERflow, a draining reinforcement fabric to spread resin to the core of the composite
SAERflow is a biaxial (+/- 45°), glass fiber fabric to which a synthetic material is added. The latter makes the combined incompressible during vacuum realization. Draining, the SAERflow thus allows excellent resin flow during infusion and replaces traditional drainage nets. Placed in the center of the layering and not just on an outer face, it also avoids the creation of preferential diffusion paths.

One layer of SAERflow allows resin to be distributed at a standard rate (equivalent to a drainage net) in parts between 8 and 10 mm thick. The use of multiple layers of SAERflow in the same layering allows optimal infusion and accelerated resin flow in thick monolithic parts such as bridge molds or hulls.

A mechanical and ecological saving
By incorporating a biaxial type BX 300, the SAERflow can be taken directly into account when calculating the boat structure. SAERTEX also offers SAERflow in the form of combinations with other fabrics and other materials such as carbon or aramid. “By combining it with a BD 600, we offer in a standardized way a self-draining QX900 four-axial that fully satisfies the marine market in front of the traditional QX 800,” explains Lionel Tourtour, sales director for Southern Europe, Maghreb and Turkey at SAERTEX.
While a conventional infusion process requires the use of an external drainage net, a perforated film, and a peel ply under the film for vacuum, SAERTEX’s innovation is to use only the SAERflow chi remains in the final piece. By eliminating most peripherals, consumables, the boat builder drastically reduces its waste and environmental impact. Lighter vessels that consume less fuel and create less waste during production. These are SAERTEX’s reasons for innovation and environmental protection.

Make hulls faster and cheaper
SAERflow enables shipyards to economize during infusion deployment. In addition to the savings in time and money associated with the elimination of consumables, the drapability of the material provides productivity gains. With drapability comparable to regular fabric, it is easier to deposit than traditional infusion nets. “We have recorded time savings of up to 50 percent,” says Lionel Tourtour.