Diathermic oils are essential, in industrial processes, to transfer thermal energy to or from a specific location. Each thermal energy transfer system is designed based on the properties of a thermal oil, so it is critical for operators to understand the impact of the oil on system efficiency. For example, how does fluid degradation affect system performance? And when does the heat transfer fluid need to be topped up or replaced?
These questions and answers explain everything professionals need to know about thermal oil and its maintenance.
Questions and answers from Diathermic Oil experts
What is the role of a thermal oil?
Thermal oil transports thermal energy from one heat source to another location. In most processes, the heat source is a furnace that runs on liquid fuel, natural gas or wood products, or submerged electrical elements that superheat the circulating fluid.
Not all uses, however, are so traditional. For example, in solar power plants the fluid is heated by sunlight and carries the heat to boil water, which in turn powers steam turbines. In waste heat recovery applications, the fluid is heated by hot pipes through which the recovered hot exhaust gas flows.
There are also cases where the chemical reaction or the fabricated part itself is the heat source, while fluid circulation transports heat to cool or maintain the temperature of the reaction.
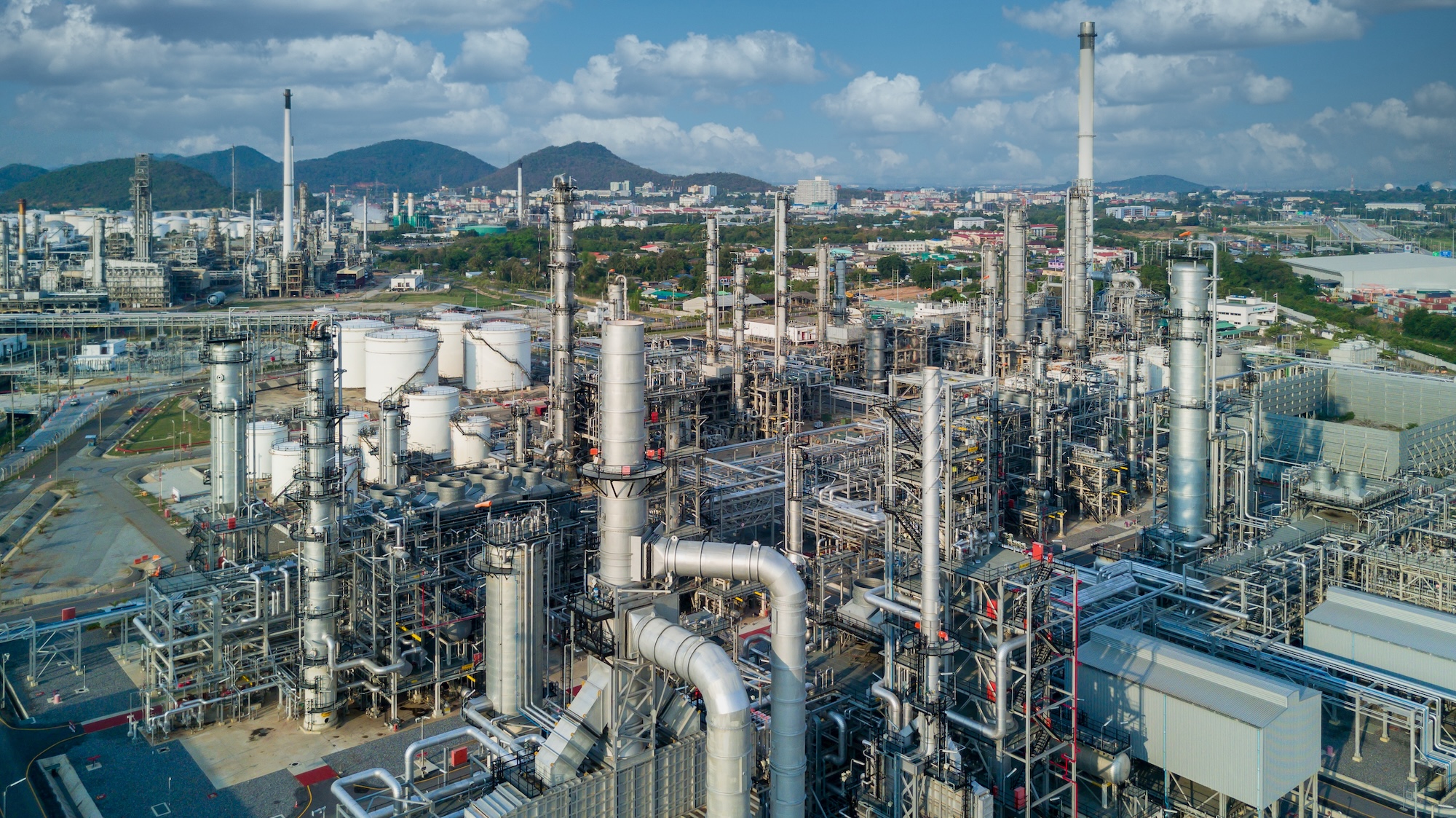
How are system efficiency and maintenance affected by thermal oil?
For any thermal energy transfer system, the components, line sizes, pump sizing, and heat transfer calculations are all based on the properties of thermal oil to ensure operation at maximum efficiency.
But as the fluid degrades, its viscosity may increase or even decrease under severe thermal cracking, and it may begin to carry solids or gases resulting from degradation or contamination.
It is important for equipment operators to know the three modes of degradation:
- Contamination-both external, such as rain or dust entering the system when a bolted cover is missing, and internal, such as a leak from a hole that allows process material to enter the hot oil stream, or wear and tear on components.
- Oxidation-hot fluid reacts with oxygen from the air. It starts with browning and thickening of the fluid, but if left untreated it leads to sludge formation and accumulation of acidic residues in low-flow, low-disturbance areas such as the bottom of tanks or expansion tanks.
- Thermal cracking – typically occurs when fluid molecules receive more heat energy than they can absorb and transport. It can lead to reduction of the flash point (and boiling point) of the fluid and fouling of heat-receiving surfaces. The deposited carbon layer acts as an insulator, forcing operators to increase heat flow to maintain the same operating temperature.
Once degradation occurs, the original heat transfer calculations become less accurate and the system will have to be used more severely to compensate and produce similar results. This will have a direct impact on company finances, as the need to raise temperatures due to oxidized fluids affects fuel and electricity costs, while insoluble materials that collect in low-disturbance areas increase the need for costly maintenance.
How often and when should diathermic oil be replaced?
Two key elements must be considered when determining the frequency of diathermic oil replacement.
- The first is the type of application: for example, in plastic extrusion, engineers can expect the oil to last between 4,000 and 6,000 hours, while in asphalt storage, operators can use the same oil change for up to 25 years if properly maintained.
- Second, attention paid to maintenance and testing will inevitably play a role in the longevity of a thermal oil. Companies that regularly analyze fluids and use the expertise of their fluid supplier will understand the rate of degradation and can act accordingly to reduce or eliminate the need for a total system shutdown just to replace fluids. For example, regularly replacing only 10% of the fluid can extend the service life of the system fluid without the need for complete fluid replacement.
On the other hand, those who forgo regular inspections act reactively when production is compromised, at which point maintenance becomes much more time-consuming and expensive. For example, if a system traditionally operates at 550°F (290°C), operators may see the thermostat rise to 580°F (305°C) over the years as the system is forced to work harder due to fouling of heat transfer surfaces or increased fluid viscosity.
In the worst-case degradation scenario, the thermal oil will not circulate well enough to maintain production, or cracking will cause the fluid boiling point to drop dangerously close to operating temperature, causing the pump to cavitate and creating a significant safety problem. Once the point of no return is reached, a total unplanned shutdown is required to drain, clean, flush, and recharge the system with new thermal oil. This has a direct negative impact on the company’s profits, with a loss of production of up to four days added to expensive repair costs.
Should operators implement a used thermal oil testing program?
Two key elements must be considered when determining the frequency of diathermic oil replacement.
Used thermal oil analysis programs are critical to maintaining its efficiency and effectiveness. For operators considering incorporating used thermal oil analysis into their maintenance program, or extending their normal industrial oil analysis program to heat transfer fluid, it is important to examine the tests offered, as unfortunately some of the tests performed on conventional industrial lubricants are irrelevant or absent for heat energy transfer fluids.
For example, ISO particle counting is useful for gear and hydraulic oils, but completely useless for diathermic oils because of the browning that usually occurs during use. On the other hand, gas chromatography, flash point testing and solids content measurement are not normally part of the regular testing regimen, but they provide a useful indication of fluid condition.
It is also important to note that the results of common analysis methods may change depending on the mode of fluid degradation. For example, oxidation thickens the oil while thermal cracking thins it, so it is plausible that the oil appears to have normal viscosity while the system suffers from both problems simultaneously. To prevent these problems from being overlooked, a gas chromatographic analysis can provide a clear and accurate picture of the thermal oil.
What should be considered when choosing thermal oil?
When choosing a thermal oil, one of the most common misconceptions is that the more expensive it is, the higher the quality of the fluid will be. Although this is true up to a point, it does not tell the whole story. Some diathermic oils, while expensive by their very nature, oxidize rapidly due to the lack of antioxidant protection. Data sheets can be useful and provide information on the properties of the fluid, but they offer little information on its resistance to degradation, which is the aspect that provides the longest service life.
To avoid confusion or choosing the wrong fluid, operators should work with a lubricant expert who has a unique insight into fluid formulation and shares technical support.
In addition to this, it is important to look for customer testimonials that offer an honest view of fluid use experiences. Operations, maintenance, and safety departments should also be involved in discussions along with procurement to find a supplier eager to provide a product that meets the company’s specific needs with minimal impact on the environment and worker health. Industry best practices also include a dedicated diathermic fluid testing program and readily available, local technical support to help increase or maintain productivity and reduce the likelihood of costly shutdowns and unplanned downtime.