Thermal protection for today’s and tomorrow’s electronics
Electronic devices in order for them to function generate heat; unfortunately, this is the enemy of reliable electronics. The increased data rates in today’s electronic devices and the growing number of electronic components require even higher levels of thermal protection, in fact for engineers designing 5G products, reliable thermal protection is a top priority to avoid device failures.
5G base stations and optical interconnects require more data transfers at higher speeds, which is challenging electromagnetic compatibility experts. One solution is electrically conductive adhesives that provide reliable shielding against electromagnetic interference (EMI) while preserving their other properties.
Thermal protection: heat-conductive silicones
Thermally conductive silicones are helping engineers improve reliability and extend the life of various services required by customers. These thermal interface materials absorb significant amounts of heat from electronic components, are stable at high temperatures, and maintain their properties over time. In addition to adhesives, thermally conductive silicones include gap fillers, thermal greases/encapsulants, and gels. All these products consist of a silicone base and an insulating agent. Aluminum oxide (AL2O3), an electrical insulator with high thermal conductivity, is often used as a coating material.
There are several characteristics to consider:
- Thermal conductivity, or the transport of energy in the form of heat from one body to another
- Thermal resistance, the ability of a material to resist a flow of heat.
- Modulus, the measure of elongation of a material.
The thickness of the bond determines which property dominates the heat. If the bond line thickness is greater than 100 microns, thermal conductivity dominates. If the bond line thickness is less than 100 microns, thermal resistance dominates.
The modulus is generally lower in silicones than in most other thermal management materials. The low module provides stress relief and protects against shock and vibration.
It is also important to note that silicones offer strong hydrolytic stability, for resistance to degradation by moisture. and are available in non-toxic formulations compared to competing non-silicone products to help support sustainability, health and environmental safety initiatives.
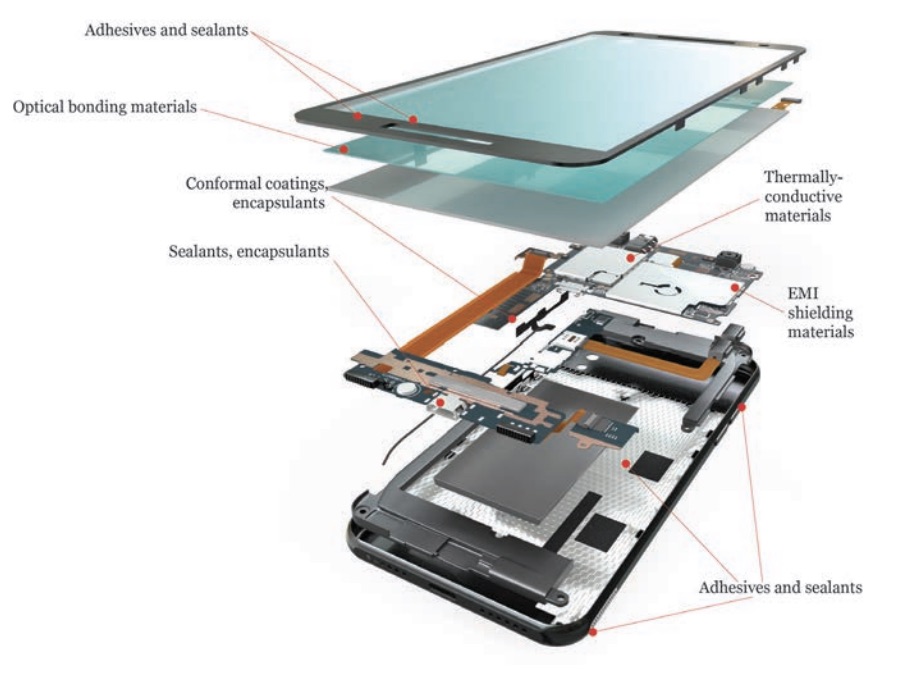
Thermal protection: silicones vs. thermal management products
In terms of device reliability as requirements become more demanding, silicones tend to outperform other materials for thermal management. The advantages of heat-conductive silicones are obvious. In particular, silicones are better in hydrolytic stability, modulus, stress, bond line thickness and exotherm of cure. Advanced silicone technologies also address several challenges specific to thermal greases. Hydrolytic stability is critical for today’s electronics because 5G requires more towers, base stations, and transmitters continuously exposed to outdoor weather conditions, including humidity and rain.
Silicones allow water vapor to pass quickly; however, it is not water vapor but liquid water that causes corrosion. Over time, thermal materials containing epoxies absorb more water than silicones, increasing the risk of corrosion. When the modulus and its relationship to stresses are taken into account, silicones are a more than viable choice for thermal management of devices.
Consider the example of a stack with a substrate, a chip and other layers of electronics. Each layer has a different coefficient of thermal expansion and, therefore, expands and contracts at a different rate. Due to their low modulus, silicones can absorb some of the stresses and convert them into motion. Epoxies, on the other hand, are strong, but their mechanical strength does not relieve stresses that can cause cracking over time. All thermal management materials are designed to be reliable, but the long-term reliability of silicones is what sets them apart.
Adhesives
Heat-conducting silicone adhesives eliminate the need to use mechanical fasteners. Silicones provide reliable protection of sensitive components and systems.
They are available in one-part (1-part, 1K) formulations that require cold storage and two-part (2-part, 2K, A&B) formulations that require mixing.
To support different dosing needs and dispensing requirements, heat-conductive adhesives are available in a range of rheologies:
- Fluid adhesives, which support rapid filling of channels and cover larger surfaces.
- The low-power products that allow controlled dispensing to cover the desired area.
- The highly thixotropic products, which allow for rapid dispensing and precise placement without overloading or sagging.
- The heat-conductive silicone adhesives.
All provide long-lasting performance and bond lines that resist high temperatures and moisture. The curing time of one-component adhesives
depends on many factors, ambient temperature, relative humidity, and the depth of moisture and air penetration. Advanced formulations ensure reliable adhesion to most substrates.
Gap filler
Thermally conductive silicone gap fillers.
are replacing traditional elastomers, which can fail to protect joints and conduits. The heat-conductive silicone plates fully accommodate the irregular side-to-side distances that create problems for dimensionally constrained pitches. For added reliability, they offer excellent mechanical and elastomeric stability during thermal aging. Thermally conductive silicone gap fillers can dissipate heat from critical automotive components, such as the engine or transmission control unit, or braking and stability sensors.
Thermal greases
Thermal greases are one-component materials
which provide a medium between a heat sink and an air heat source to maximize heat transfer and dissipation. Thermal greases are applied in thin layers, usually less than 100 microns. Given this limited thickness, thermal resistance (rather than thermal conductivity) is the dominant property of heat. In particular, thermal greases have particularly low resistance compared with other types of heat-conductive silicones. Historically, thermal greases were used in microprocessors with a chip and a relatively narrow temperature range. Automotive applications have expanded the required temperature range and placed the electronics vertically. In turn, gravity has contributed to several problems:
- “Bleed-out” which occurs when the liquid polymer migrates past the bond line and interferes with the soldering or bonding of wires. Compared with other chemical greases, advanced silicones exhibit lower bleed-out for greater assembly reliability.
- There is also the phenomenon of “dry-out,” resistance to which is important because harder materials are unable to adequately wet surfaces, and this is where thermal greases act.
- “Pump-out,” or the unrecoverable loss of thermally conductive materials between substrates. Pump-out occurs when repeated compressions of the bond line occur, which thermal conductive fats can prevent.
Encapsulants and gels
Encapsulants and gels are heat-conductive silicones that combine thermal and physical protection. They can offer protection against mechanical and thermal shock, chemical attack, dust and moisture. The gels have a remarkably low modulus and can protect the most sensitive and delicate components. Encapsulants and gels support rapid curing with moderate heat. These materials are available in a varied range of viscosities and have high thermal conductivity. Advanced silicones used in today’s encapsulants and gels can also achieve good adhesion without the use of a primer, which helps reduce cycle times. They have fast cure times and harden into rubber-like elastomers for reliable protection. Finally, they also have excellent dielectric properties, adhere to many substrates, and are a good choice for the automotive industry.
Thermal protection: advanced silicone solutions
Engineers need reliable and long-lasting protection provided by advanced formulations of heat-conductive silicones. It is important to choose materials that meet requirements and work with an experienced supplier capable of technical support when and where it is needed. Thermal protection is critical not only for today’s electronic devices, but also for future technology trends that promise faster data rates by generating more and more heat.