The adhesive joint
The long-term performance of an adhesive joint depends on the properties of the adhesive and the materials to be joined. The adhesive can be affected by high temperatures or exposure to water or chemicals. The durability of the joint will also depend on the effects of these agents on the substrates to be joined. Above all, it will depend on the condition of the joint surfaces at the time of bonding. The best joints are obtained when the surfaces are absolutely clean and completely wet from the adhesive.
The control of surfaces
The durability of glued joints (remove) requires the control of surface pretreatment. A poor surface condition usually results in relatively low initial strength and reduced durability. A thick bond line results in lower initial strength (Figure 4). With most types of reactive adhesives, applying heat to complete the curing process improves both initial strength and durability. The user will need to assess the level of control required for these factors in order to produce a bonded joint suitable for the expected service conditions. For many applications, sufficient durability is achieved with easily achievable levels of surface pretreatment, control of bond line thickness, and monitoring of the curing schedule.
The thickness of the joint
Shear strength decreases if the joint line is too thick. The diagram (Figure 4) shows the effect of increasing joint line thickness in simple joints made with cured epoxy adhesives. The optimum joint line thickness is between 0.1 and 0.5 mm. With very thin bond lines, there is a risk of incomplete filling of the joint due to contact between the high points of the joint surfaces. Bonded joints (lever) may have to withstand sustained, static or cyclic loads. Joint designs where peeling stresses are minimized offer the best durability. Cyclic fatigue tests of simple shear joints made with epoxy adhesives often yield failure values of about 30 percent of the static failure load (Figure 5).
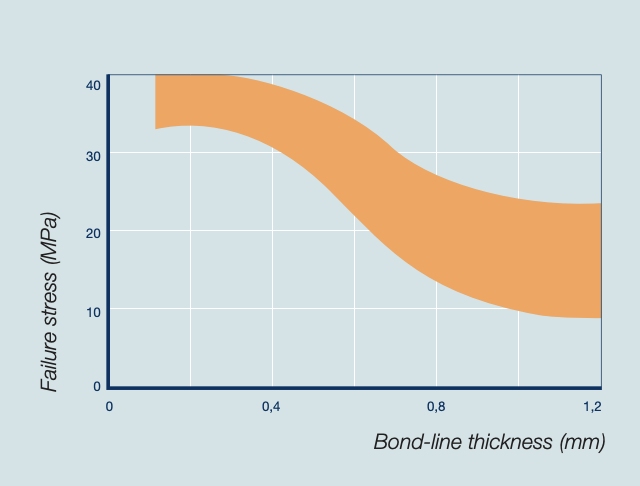
FIG.4 BOND LINE THICKNESS VERSUS SHEAR FORCE
The adhesive force at the interface is inherently greater than the cohesive force within the adhesive. The diagram shows that in this adhesive, the drop in strength occurs in the range of 0.4 to 1.0 mm. In thicknesses above 1.0 mm, the shear strength is approximately constant. The exact shape of the curve depends on the characteristics of the adhesive. Hardened adhesives will maintain higher values in thicker bond lines, while stiffer adhesives will decrease more rapidly.
FIG.5 FATIGUE (TENSILE) STRENGTH OF LAP JOINTS
Adhesives are often used in applications where they are subject to dynamic and static stresses. Small repeated loads can lead to fatigue cracks. Over the course of many load cycles, these cracks can propagate and lead to joint failure. Cyclic lap shear tests can be used to determine the fatigue strength of an adhesive joint. A repeated load is applied and the number of cycles until failure is recorded. The load can be varied to obtain a complete picture of fatigue performance.
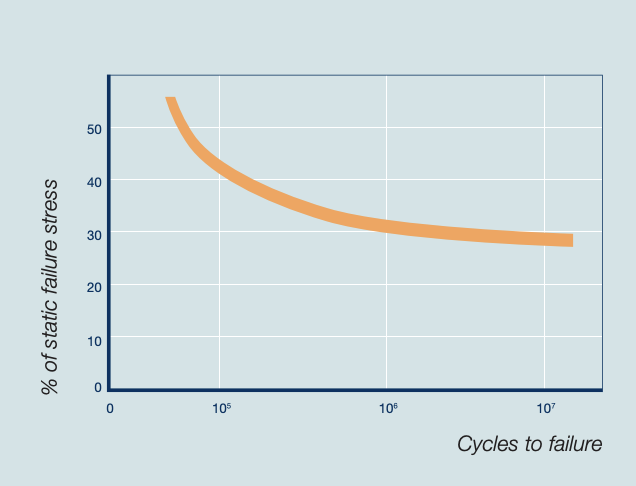
Always remember
Mascherpa technicians will give you usage tips, and support you in your application validation processes
Accession is a special process in that its validity cannot be assessed through final measurements on the product or the process itself, and therefore it must be subjected to planning, control and qualification methodologies.