Adhesives for composites: BETAFORCE for multi-material light vehicles.
For high-performance bonding in multi-material lightweight vehicles, DuPont’s BETAFORCE composite adhesive enables significant weight reduction, maintenance of acoustic performance flexibility, and achievement of processing performance and sustainability goals.
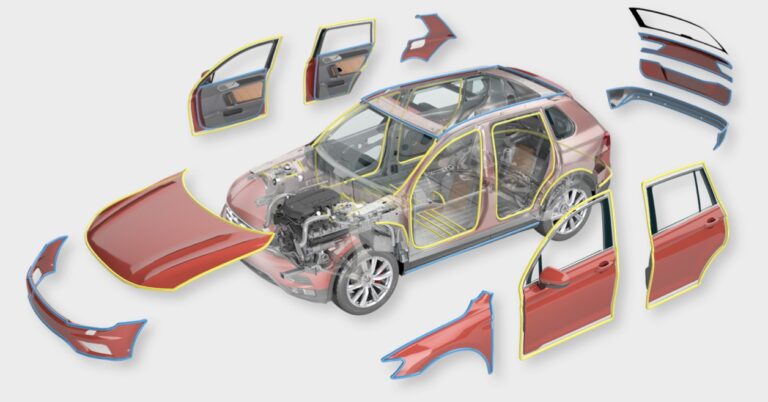
BETAFORCE: The ideal choice for various applications
BETAFORCE is perfect for joining carbon fiber and fiberglass composites and other dissimilar materials in a variety of projects involving lightweight materials, including modular assemblies. This composite adhesive can be used to join coated metals such as steel to aluminum, carbon fiber panels to steel or aluminum, and sheet molding compounds (SMC) to aluminum.
Composite adhesives: in the automotive world.
Composites are gaining ground in automotive manufacturing because of their weight-saving potential, but they remain difficult to bond with other materials. Composite adhesives offer a reliablealternative to traditional mechanical and thermal processes that cannot be applied to these lightweight materials. Advanced bonding solutions, such as Dupont’s BETAFORCE composite adhesives, provide a continuous bond line and cohesively join surfaces. Recent formulations of BETAFORCE offer a cycle time of about one minute and are currently used for mass production. Open times can be adjusted to suit specific mounting requirements in the implant, such as faster curing time by infrared treatment, and initial adhesion does not require additional fastening tools.
Advantages in processing and performance:
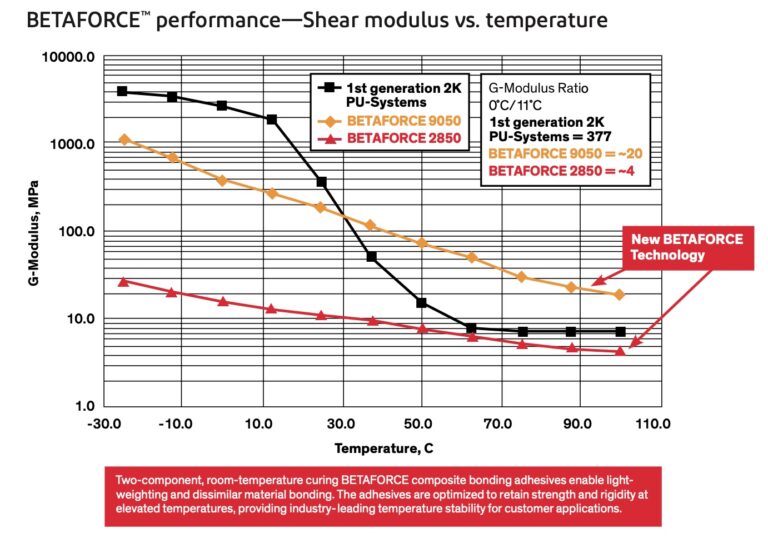
- Enables wall thickness reduction due to the structural mechanical properties of the adhesive
- Enables optimization of substrates and adhesive structure
- Excellent temperature resistance and module retention throughout the working temperature range
- Reduces process time and saves investment due to very fast acceleration capability
- Reduces process complexity through primerless adhesion performance
- Provides a corrosion barrier between dissimilar materials
- Reduces noise, vibration, and harshness, and improves accident performance
- Demonstrates variable curing rates
- Has a wide range of mechanical and product properties
- It has excellent bead stability during application
- Allows for general bonding after coating and painting.
- Demonstrates resistance to handling in minutes with accelerated thermal curing due to customized chemistry
- Combines high modulus, high strength, and high elongation in one system to effectively handle differential CLTE (e.g., carbon fiber and aluminum composite) even on long bond lines
- Provides effective sealing against water intrusion
- Improves durability through optimized load distribution
- Optimal mixture ratios at 1:1 by volume
- Available in large or small packages