Born2Bond™ Light Lock HV: 10 tips on light-curing adhesives.
The light-curing adhesives
Born2Bond
, especially Born2Bond™ Light Lock HV, are the most popular products in assembly processes. Their speed of cure and bond strength are some of the reasons why manufacturers choose them over other adhesive options. To facilitate processing, some dosage variables must be taken into account. Product substrates, light source, light exposure, and other variables can add complexities that can inhibit the adhesive’s ability to form effective bonds.
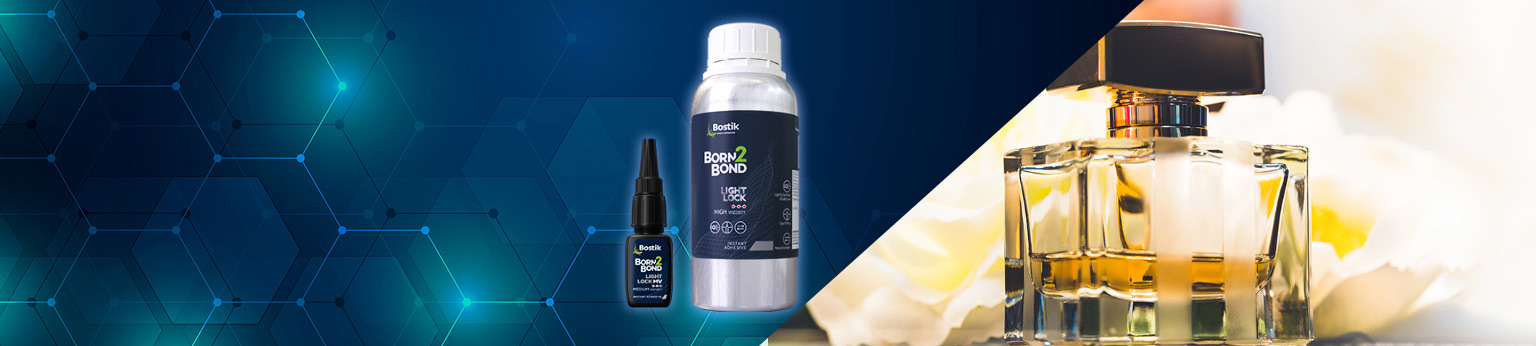
To help reduce the probability of error and easily achieve production goals, it is helpful to follow these 10 tips we propose:
- Use appropriate personal protective equipment: Light-curing adhesives sometimes use light from the UV spectrum to cure. To ensure adequate protection from this type of light, it is a good idea to wear gloves when handling the adhesive. When using UV light, it is also good to wear safety glasses with UV protection for the eyes.
-
Compatibility between adhesive and application type:
Not all assembly applications are compatible with light-curing adhesives, such as Born2Bond™ Light Lock HV. Some opaque or colored substrates do not transmit UV light, and many types of clear plastic contain additives (such as UV inhibitors) that can prevent the product from curing. Working with Mascherpa, this problem is easily solved because we will be able to recommend the right adhesive for each type of intended application.
- Compatibility between dispensing equipment and light-curing adhesives: Investigate in equipment with dispensing nozzles compatible with light-curing adhesives. All production equipment should be opaque and UV-resistant to avoid premature curing. If a dual-cure system is used, attention should be paid to the size of the nozzle orifice. If the orifice is too small, the adhesive may cure inside it, causing unexpected downtime to resolve the problem.
- Examine the production environment for unwanted light exposure: Manufacturers often underestimate the extent to which light exposure can cause problems in the dispensing process. Take Born2Bond™ Light Lock HV as an example, such adhesive may have premature curing due to light from windows or ceiling lamps. This can result in wasted material and increased downtime. Consider using opaque and UV-resistant equipment. Properly seal sticker containers to prevent unwanted light. Also, make sure the UV light is far enough away from the dispensing nozzle; if the light is too close, the adhesive may cure inside the nozzle.
- Complete the substrate preparation: Make sure the substrate is clean and free of any dirt. These contaminants interfere with the adhesive’s ability to properly wet the surface. In addition, some substrates may require additional steps before a light-curing adhesive can be applied; for example, low surface energy substrates such as polyethylene may require a primer or other preparation. Contact us directly to ensure that you properly prepare the substrate with any primers or other techniques. In this way, adhesive application will be easy and safe, and the performance of the adhesive will be optimal.
- Reduce exposure to shade during curing: For best results, the light-curing adhesive must be fully exposed to light. If some areas of the adhesive will be shadowed, manufacturers should consider a dual-cure adhesive. These solutions can be fixed by light and fully cured by moisture or other activation methods.
- Beware of air bubbles: Air bubbles can affect the bond strength of Born2Bond™ Light Lock HV adhesive, reducing the expected weight of the application. To reduce the likelihood of air bubbles, lines should be flushed after filling or replacing adhesive containers. In addition, a dispensing pressure appropriate to the viscosity of the adhesive should be used. For low viscosity adhesives, pour-in or drop-in pressure cookers are the most effective, while for higher viscosity adhesives, metering pumps are recommended. Born2Bond™ Light Lock HV for example is a very versatile product in this respect because it is available with different viscosity ranges.
- Match the wavelength of light to the adhesive: Adhesives have a specific wavelength for fast and strong curing. These wavelengths can range from 365 nm to 450 nm. Although the adhesive will continue to cure at slightly different wavelengths, for best results it is a good idea to match the wavelength of the UV or LED light to that of the photoinitiators in the adhesive.
- Use appropriate light intensity: The intensity of the light source can also affect the curing speed of the adhesive. Higher intensity can help reduce the curing time. However, each adhesive has a maximum intensity. When the maximum limit is reached, the curing process either does not accelerate or accelerates too much, reducing residual tack.
- Provide constant exposure to light for uniform curing: If the light source is not fixedly positioned, it can cause inconsistent curing between different applications. This problem can be easily solved by incorporating light into the automation process. In this way, products can pass under the light set at a constant distance and brightness.
Mascherpa offers precise, high-performance light-curing adhesives suitable for a wide range of assembly applications. An Exemplary Product is Born2Bond™ Light Lock HV, a nearly odorless, limited blooming effect instant adhesive specially designed to bond most substrates, including plastic and rubber. The formulation is designed to have high bond strength, even in areas subject to bending, and in addition, careful selection of ingredients in the formulation ensures that the product does not stain areas near the bond line.