One question we are constantly asked is, “How can I best protect my PCB, with conformal coating or with a resin?”
One question we are constantly asked is, “How can I best protect my PCB, with conformal coating or with a resin?”
The first thing to consider is the design of the ‘housing within which the PCB will be enclosed. If an assembly is enclosed in a housing designed to be the primary environmental protection, conformal coating is often used to provide additional support. Where housing cannot provide the primary protection from its operating environment, most of the time a resin might be a better choice.
The next question should be “What do a coating and a resin have in common?” Both are generally organic polymers, which can form an electrically insulating layer with some degree of chemical and thermal resistance.
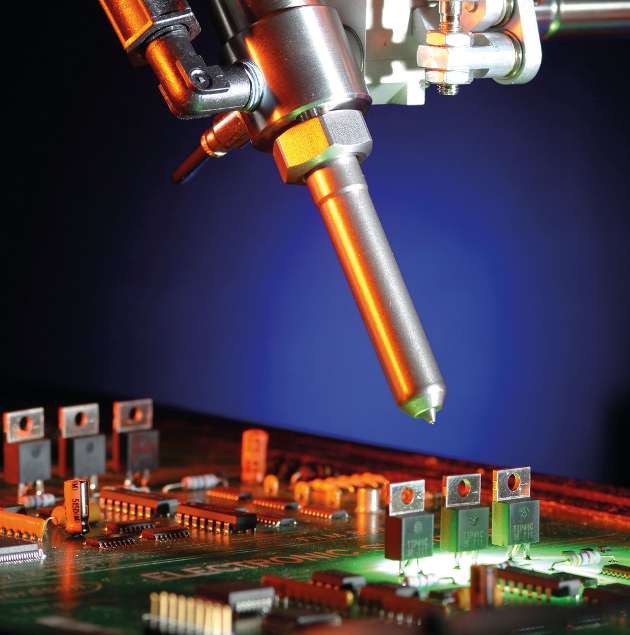
Conformal Coatings
Generally, these coatings are thin films applied in the thickness range of 25 to 100 microns, leading to minimal weight gain. Coated components are easy to identify, and the coating can be easily reworked and components replaced as needed. The chemical and thermal resistance of conformal coatings is generally good for short exposures. A coating applies relatively little stress on components; this is an advantage when a component has many raised details.
Encapsulation resins
Resins can be applied with a minimum thickness of 0.5 millimeters. The increase in thickness results in a significant increase in weight. However, it means that the PCB is far better protected from chemical attack, particularly in cases of prolonged immersion. In addition, a resin may provide superior protection against physical shock (depending on the formulation). A layer of dark-colored resin can completely hide the PCB, which allows for some design security; it should be added that removal of the resin can often result in destruction of the PCB.
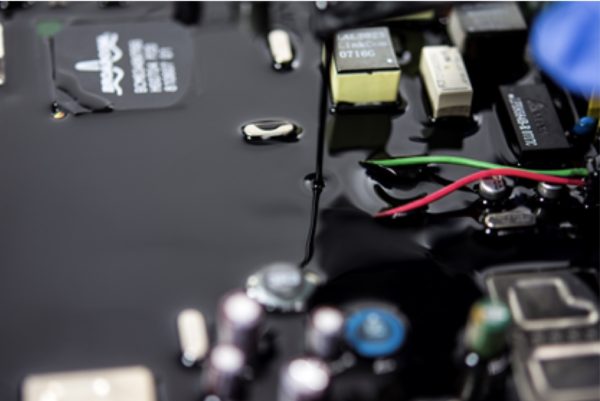
So how do I choose which one is best for my application?
PCB design, housing, and end-use environment are all important factors in the decision.
As mentioned earlier, if the housing provides adequate primary protection against the environment, the use of conformal coating provides a back-up that can provide protection to the board if the primary protection is damaged, as well as provide protection against high humidity and condensation inside the housing.
Often, resins are used to form part of the housing itself and are therefore an integral part of the primary protection of the system, and as such are required to resist all potential contaminants in the end-use environment.
A well-designed PCB and housing will make applying the coating or resin a quick and efficient process
And just to make things more interesting, Electrolube has recently launched a conformal coating range, based on two-component chemistry similar to resins, but designed to be applied with selective coating equipment in the 200-400 micron range, thus combining many of the advantages of both technologies and minimizing many of the drawbacks of each.
In fact, these new
2K conformal coatings
have demonstrated excellent performance in wet environments. In environmental chamber tests simulating highly condensing conditions, 2K conformal coating achieved the same results as resin with one-tenth the thickness. 2K conformal coatings can be applied thicker than previous coatings without risk of cracking. They can also be applied by selective coating techniques to provide greater thickness a significantly more precise coverage.
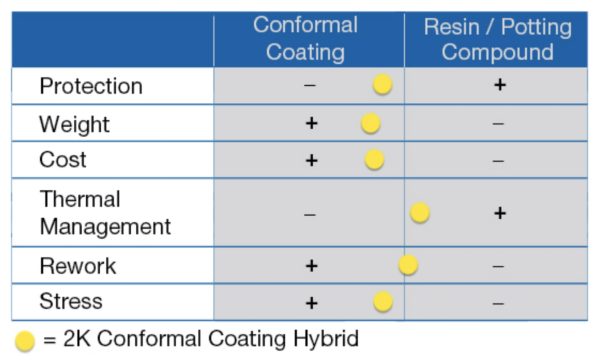