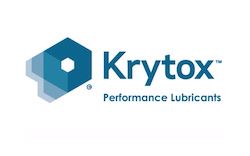
Krytox™ AUT U14
PFPE anti-noise oil on EPDM gaskets
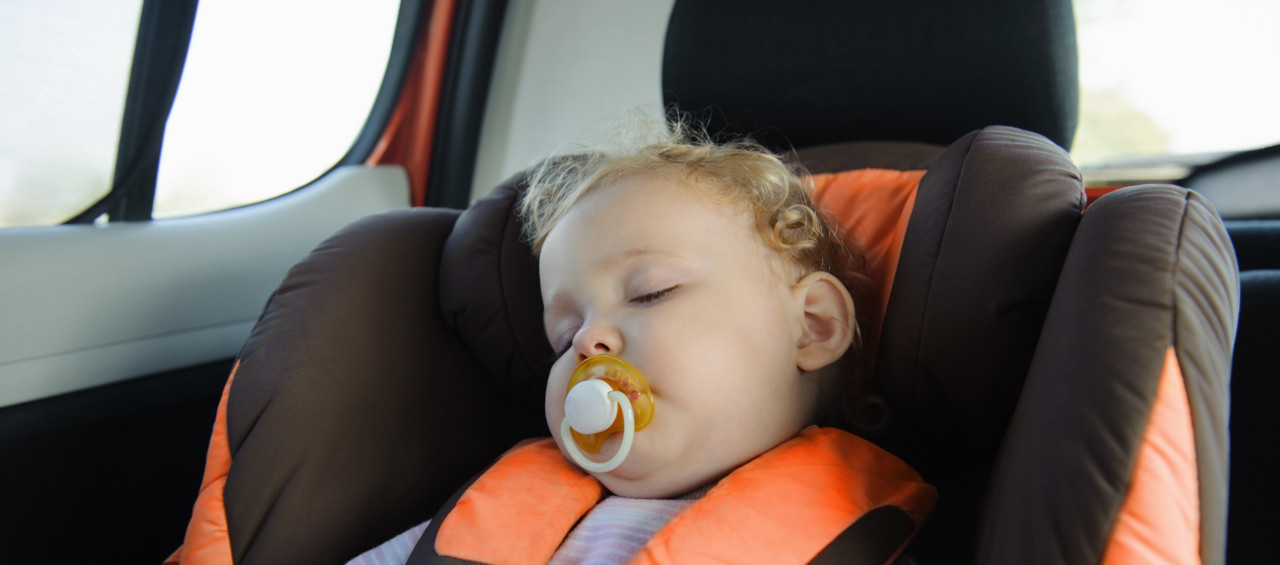
PRODUCT INFORMATION
Krytox™ AUT U14 is a high-performance perfluoropolyether (PFPE) oil formulated to meet the needs of the automotive industry. Designed to prevent noise, vibration, and ‘roughness of ride (NVH) over the life of the vehicle, Krytox™ AUT U14 has been used by automotive OEMs to solve elastomer sealing problems in sunroofs, doors, and windows. With excellent lubricity in the presence of contamination, extreme resistance to leaching from water and other common automotive solvents, and enhanced protection against harmful ultraviolet (UV) light, Krytox™ AUT U14 will maintain lubricity under the harshest conditions.
Additional advantages of Krytox™ AUT U14 include wide-range temperature performance and an added soluble UV dye that enables visualization of surface coverage.
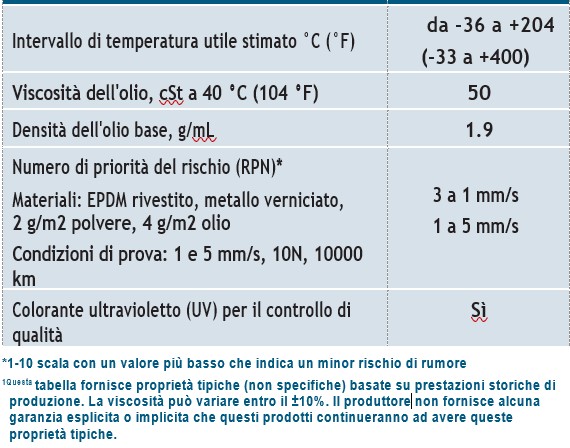
APPLICATIONS
Krytox™ AUT U14 is designed the dynamic EPDM seals. These seals, commonly used on vehicle doors and windows, often have NVH problems from buzzing, squeaking, and knocking (BSR) noises. Because of the high-friction contact of the rubber elastomer against glass or painted metal, they are susceptible to a noise-generating phenomenon called stick-slip. To reduce stick-slip, elastomer seal manufacturers apply a dry slip coat, which is often only moderately effective and rarely maintains lubrication in the presence of common dust or dirt contamination.
Krytox™ AUT U14 is specially formulated to protect against NVH problems related to stick-slip on coated EPDM gaskets, even in the presence of contamination. With only a small amount (4 g/m2) of oil applied to the elastomer surface, Krytox™ AUT U14 brings several advantages:
- Reduce the risk of stick-slip noise with uniform surface coating
- Protect against cracking, shrinkage and swelling of elastomer
- Minimize mechanical wear from high surface friction
- Improve application quality control with UV-detectable additive
The PFPE chemistry of Krytox™ AUT U14 is ideal for the needs of sealing and watertight applications in the automotive industry. Key properties include:
- Compatibility with metals, plastics, elastomers and paints
- Resistance to washing from all non-fluorinated solvents, including water, fuel and alcohol
- Performance at wide temperature range
- Extended lubricant life due to low volatility and outgassing
- Non-oxidant
PERFORMANCE TESTING
Reduced risk of noise in the presence of surface contamination
Zins Ziegler (ZZ) is an automotive industry standard test apparatus for measuring the noise potential of different pairs of materials.
ZZ performance data in Figure. show the benefit of Krytox™ AUT U14 in preventing stick-slip-related noise. This ZZ test was performed on EPDM, in the presence of environmental dust contamination, with and without Krytox™ AUT U14 and they compared performance on different combinations of speed and force. Samples treated with Krytox™ oil had a lower RPN, meaning a lower risk of noise in more than 90% of the speed and force combinations tested.
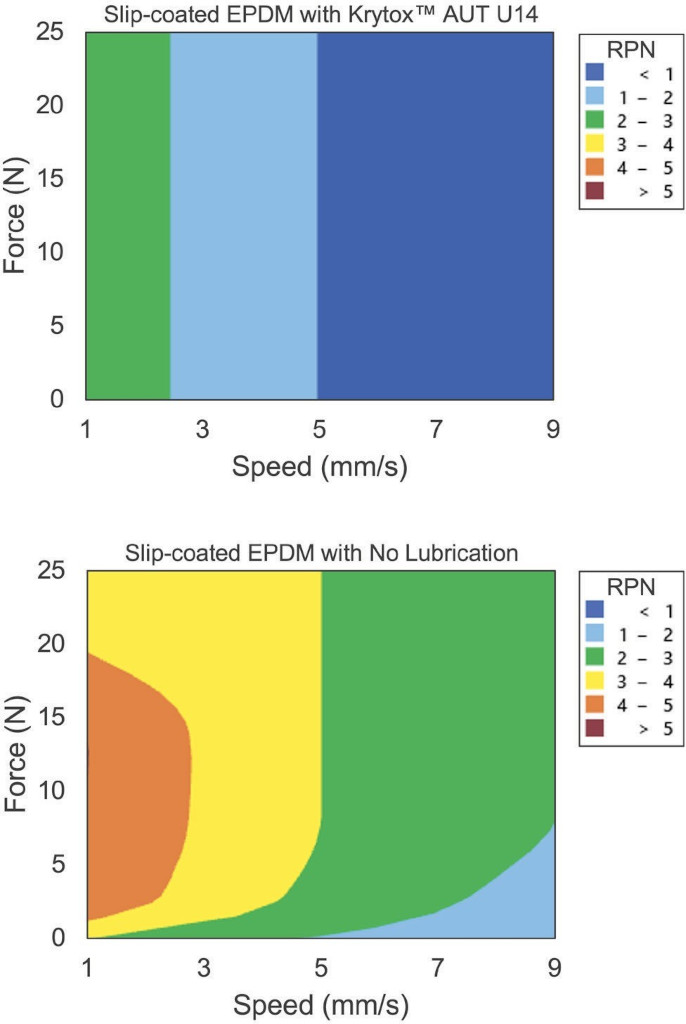
Minimize noise with an ‘even application of the surface
Uniform lubricant coverage is critical for consistent stick-slip performance. Microscopic images of an untreated EPDM surface (Figure a), treated with a standard PFPE oil (Figure 3) and treated with Krytox™ AUT U14 (Figure c) illustrates how AUT U14 coats automotive seals more uniformly than other offerings. This comprehensive coverage ensures a consistent friction profile across the entire surface, reducing the risk of stick-slip generated noise.
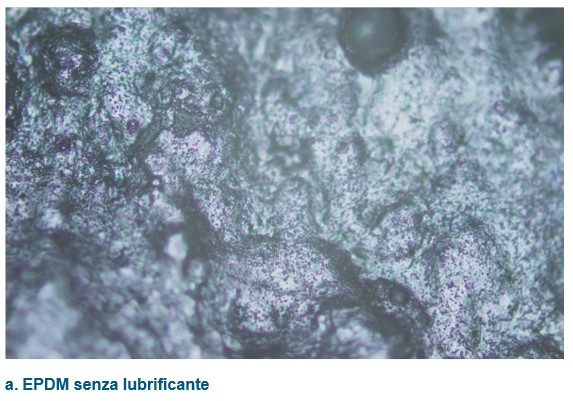
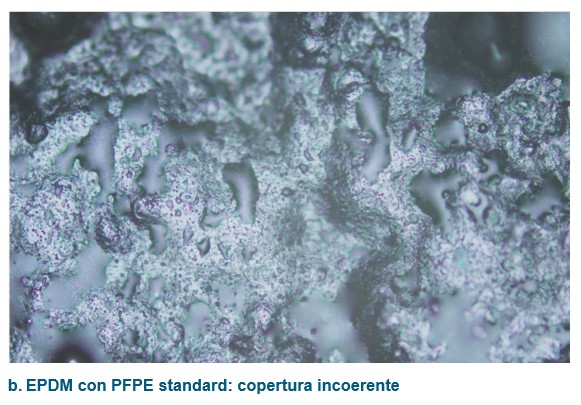
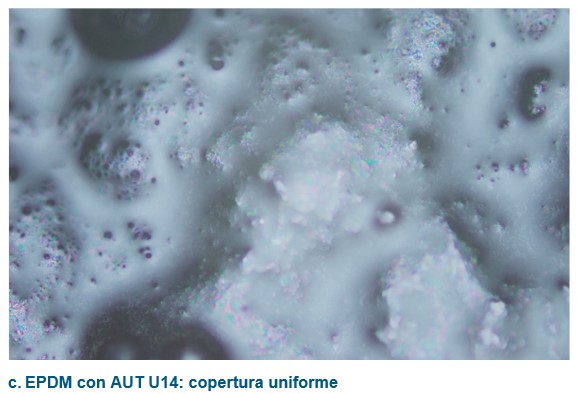
Extreme resistance to runoff keeps the lubricant in place
Krytox™ PFPE oils have a chemically inert, fluorinated polymer structure that is extremely resistant to moisture, so the oil stays in place during cleaning or exposure to rain. This resistance to runoff was confirmed by an independent laboratory that measured the coefficient of friction (COF) between EPDM rubber and a metal plate. COF was measured without lubrication, after lubricating the EPDM with Krytox™, and after washing the lubricated surface with fuel, alcohol, heptane and soapy water. Figure 4 shows that initial lubrication resulted in a 90% reduction in COF, and almost all of this improvement in COF was maintained after aggressive washing.
Materials used: EPMD rubber, metal plate, Kytox™ GPL 105. Test conditions: Rubber pulled on the metal plate at 50 mm/min. Cleaning method: Washing with fuel, heptane, alcohol and soapy water.
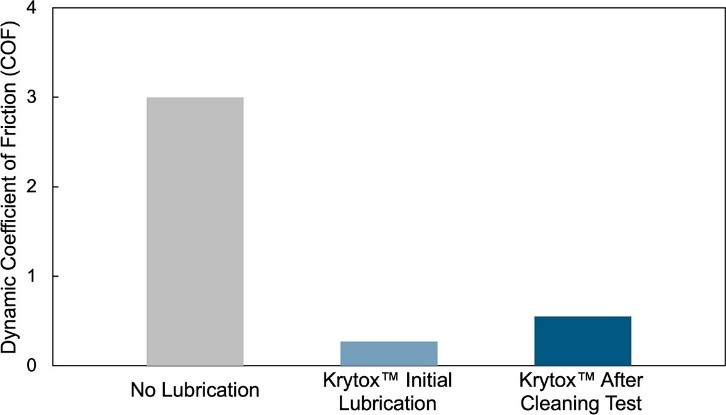
Figure. EPDM dynamic coefficient of friction (COF)
Increased protection against ultraviolet (UV) light
Exposure to ultraviolet (UV) light can cause degradation of EPDM seals, but application of Krytox™ PFPE oil to EPDM can provide additional protection against this mechanism. The impact of this UV protection is observed in Figure , which shows, after 3,000 hours of UV exposure, that specimens coated with Krytox™ AUT U14 base oil maintained greater elongation than those with slip-coat alone.
Materials tested: EPDM without lubrication and with Krytox™ AUT U14. Test conditions: SAE J1960 3000 hours accelerated exposure to xenon arc
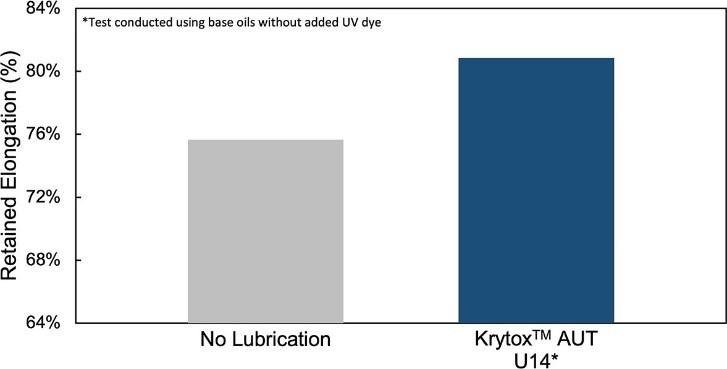
Figure . Impact of surface coating on the retained elongation rate of EPDM
Compatibility
Krytox™ lubricants are chemically inert and compatible with most materials of used in auto manufacturing, including paints, sealing materials, glass, plastics and metals. Krytox™ oils are non-reactive, have a different chemistry from standard lubricants, and should not be mixed with other non-PFPE lubricants. They are non-flammable and contain no hazardous volatile organic compounds (VOCs).
Using Krytox™ Performance lubricants.
Krytox™ lubricants do not migrate or degrade. When you choose Krytox™ oils and fats, you are choosing the confidence that comes from a first-class supplier and industry leader for more than 50 years. With access to our team of experts, you can feel confident knowing that we are ready to meet your lubrication needs.