From smartphones to tablets, from battery chargers to vehicle electronics, printed circuit boards (PCBs) contain electronic components that are getting smaller, more sensitive and closer together. However, it is not only the PCB design rules that are changing.
High humidity, thermal cycling, airborne contaminants, and physical stresses that were once primarily associated with military and industrial electronics are now also a challenge for consumer and automotive electronics. Whether it is a cell phone inside a backpack or a PCB assembly inside a car, electronics can be at risk.
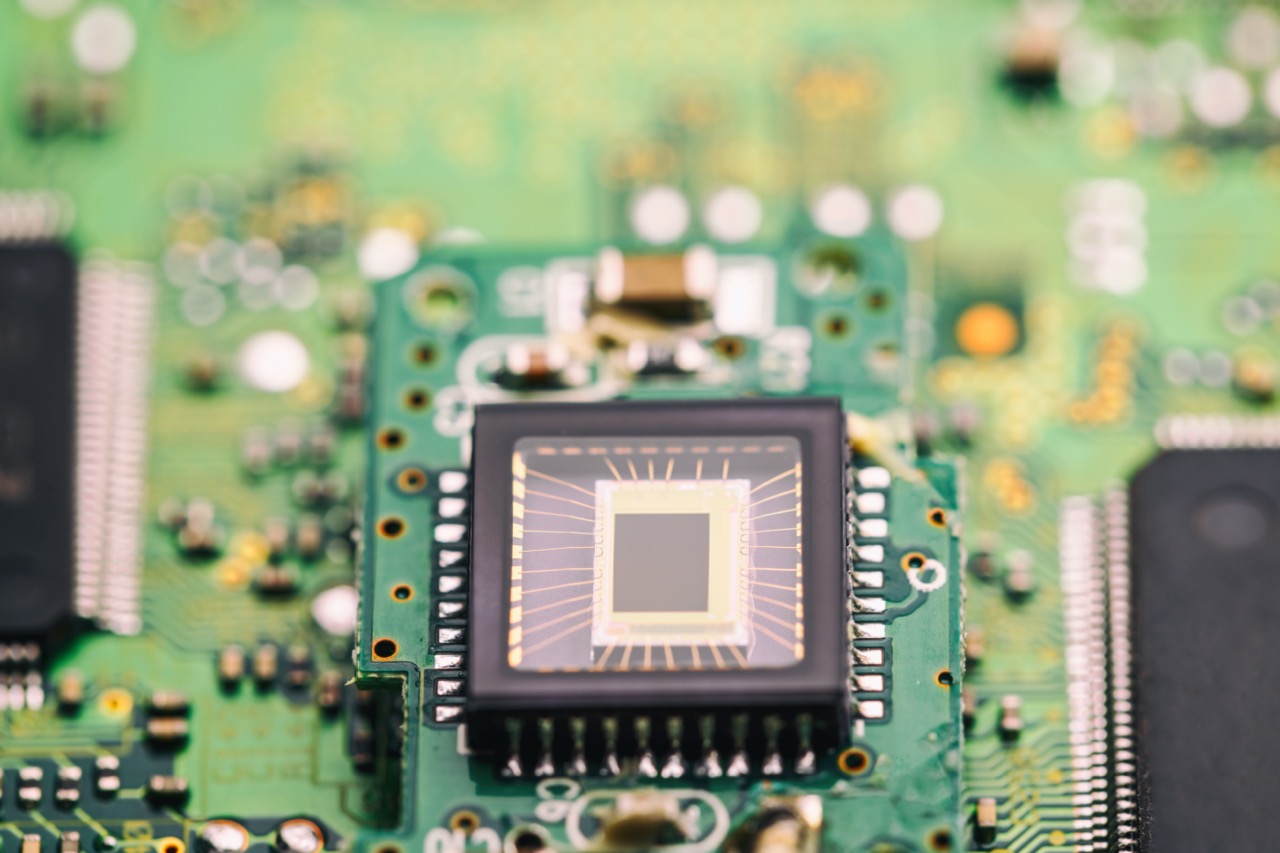
Conformal silicone coatings: innovation and performance
In today’s scenario, where electronics are becoming increasingly miniaturized and complex, printed circuit board (PCB) protection assumes a critical role in ensuring the durability and functionality of devices. Silicone conformal coatings are an advanced solution to address this challenge, offering superior protection against moisture, contaminants, and thermal changes.
Silicone conformal coatings are distinguished by their ability to conform perfectly to the surface of PCBs, forming a protective barrier that extends into even the hardest-to-reach areas. This makes them ideal for small electronic components or those with complex configurations. Their solvent-free formula not only speeds up the manufacturing process, but also supports environmental sustainability initiatives by eliminating harmful emissions and fire hazards associated with the use of flammable solvents.
Efficient application and automation
The low viscosity of conformal silicone coating facilitates application through automated methods such as spraying and needle dispensing, significantly increasing production speed. In addition, the ability to use innovative curing techniques, such as ultraviolet (UV) curing, which takes less than a minute to cure the material, further improves production efficiency. These coatings are ideal for high-volume manufacturing environments, such as those in the automotive and consumer device industries.
Protection and durability of silicone conformal coatings
Silicone conformal coating solutions not only protect PCBs from moisture and contaminants, but also offer exceptional resistance to high temperatures, a critical advantage for applications in areas such as automotive and mobile devices. Their elasticity allows them to absorb stresses due to temperature changes, reducing the risk of damage to sensitive components.
Compliance and safety
Meeting rigorous standards such as UL-746E for materials used in PCBs and UL-94 for fire resistance, silicone conformal coatings ensure extensive compliance that is vital for market acceptance and device safety. In addition, being solvent-free, these coatings are in line with the strictest environmental regulations, supporting companies’ sustainability policies.
In conclusion
Innovative solvent-free silicone conformal coating solutions are the frontier of protection for PCBs. With their ability to improve production efficiency, ensure device durability and support environmental sustainability, they are an excellent choice for manufacturers who wish to stay one step ahead in technology and environmental protection. Choosing the right coating can significantly affect the quality and reliability of the final product, making silicone conformal coatings a crucial component in modern manufacturing strategies.