Electrolube
Conformal coating
5 ways to simplify the ‘application of conformal coating electrolube early in the design phase
Mascherpa works alongside its customers and technicians Electrolube to provide solutions as early as the design phase, we believe strongly in co-engineering and believe that this approach allows for shortening development time by reducing costs, bringing greater integration between all stages of the process, and ensuring better product quality.
In this article, Phil Kinner, technical director of Electrolube for Conformal Coatings, takes a closer look at manufacturing issues, particularly those faced by circuit designers in the early stages of a project, and will provide you with some indicators that will help you avoid some common mistakes when applying the
conformal coating
.
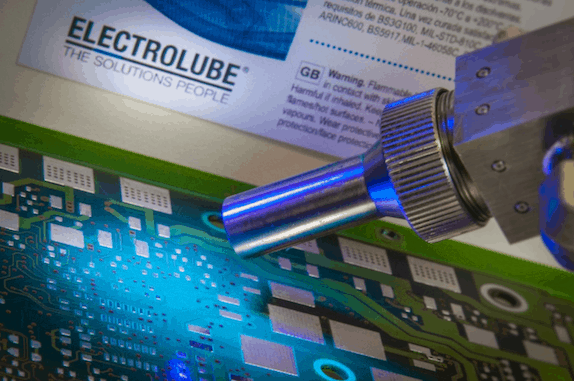