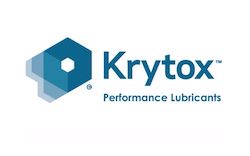
HOW TO CLEAN AND GREASE BEARINGS WITH KRYTOX™
How to clean the bearings
Dirt is one of the biggest problems that can affect bearings. A buildup of dirt on a bearing can lead to slower operations, reduced efficiency, and a greater potential for permanent damage to a machine.
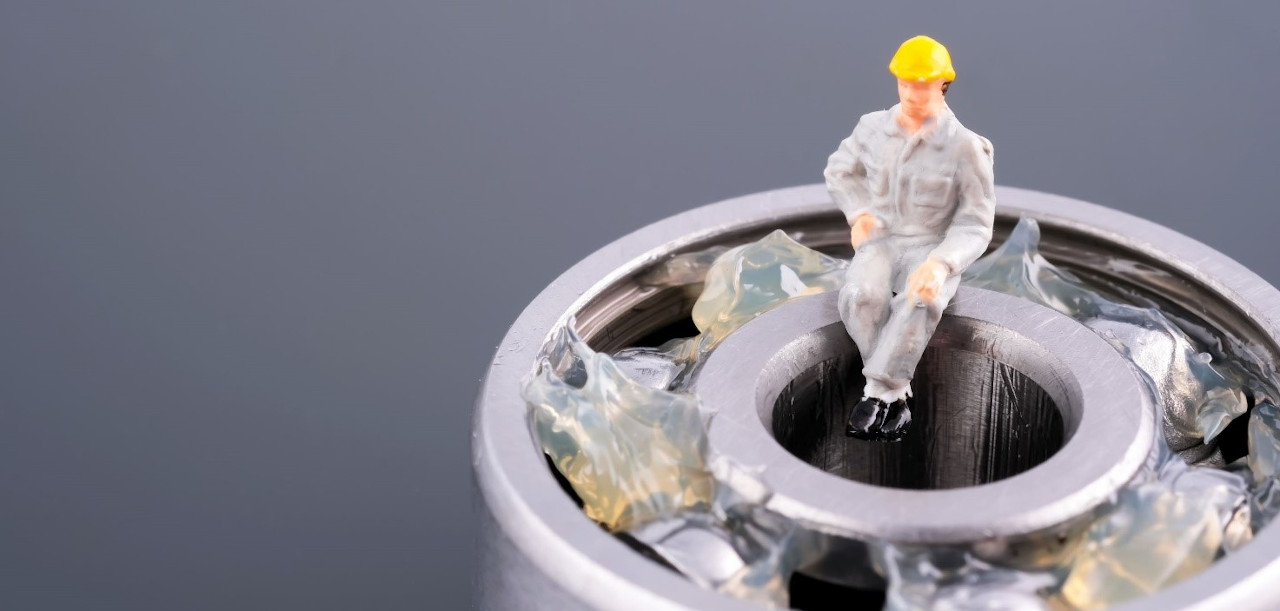
Below are some preventive measures you can take to prevent dirt from settling on the bearings during handling, before you start cleaning and greasing the bearings:
- Wear clean elastomeric gloves.
- Use clean, lint-free bags.
- If using compressed air, use filtered and dry air,
- All traces of existing grease on the bearings must be cleaned before applying Krytox ™ greases, as otherwise carbon deposits may form that could lead to failure or ‘premature wear.
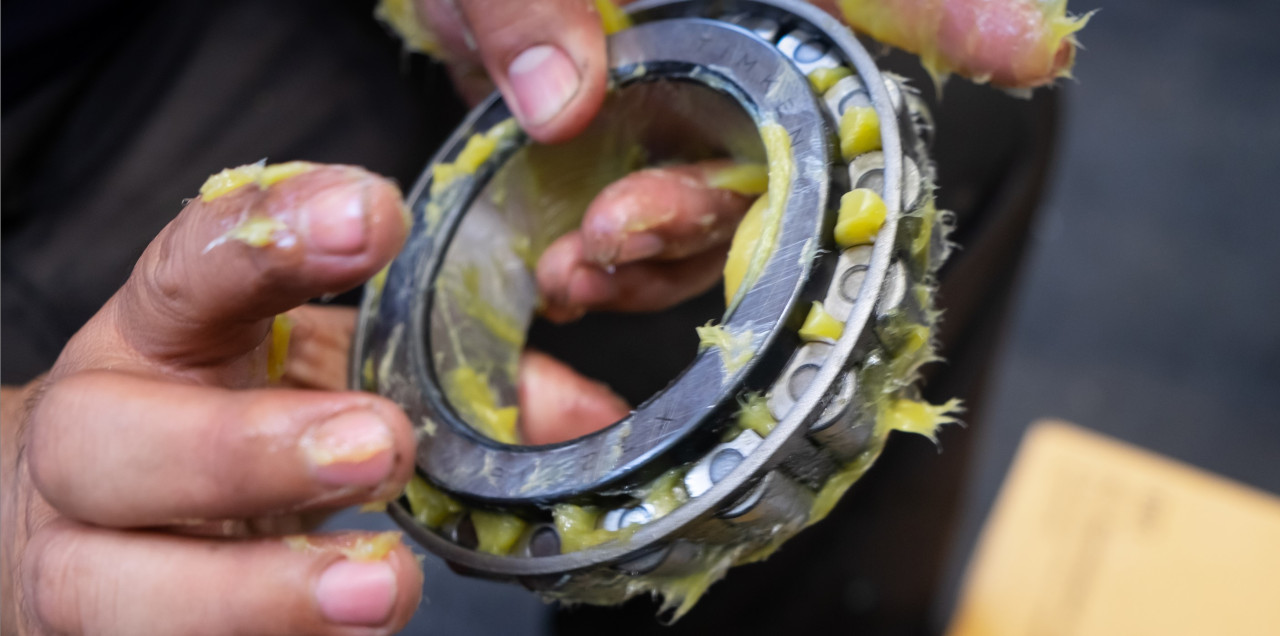
Bearing cleaning can be broken down into 4 simple steps:
- Use a pry tool to carefully remove the seal, prying between it and the inner ring, without touching other parts of the bearing.
- Place the pads in a clean basket, then carefully lower the basket into a clean solvent container. Use an appropriate solvent for the type of lubricant on the bearing. Avoid chlorinated solvents as they can cause corrosion. Usually fluorinated solvents are not needed for hydrocarbon-based lubricants.
- Physically shake the parts or pump cleaning fluid through the bearing. Keep the temperature of the solvent below the flash point. An ultrasonic cleaner can also be used.
- Dry the pads by blowing hot air through them or heating them for 10 minutes. Allow to cool to room temperature.
How to grease bearings
Once cleaned, the bearings should be lubricated immediately, by hand, with a Krytox™ lubricant
Bearing greasing can be divided into 4 simple steps:
- Weigh the correct amount of fat on a scale in grams and transfer it to a syringe (to calculate the amount of fat to put in a pad, see the next section).
- Inject half of the grease into the cavities between the rolling elements; one half on both sides of the bearing.
- Carefully rotate the bearing, manually, to distribute the grease on the rolling elements.
- Replace screens or gaskets carefully, preventing grease from leaking out prematurely.
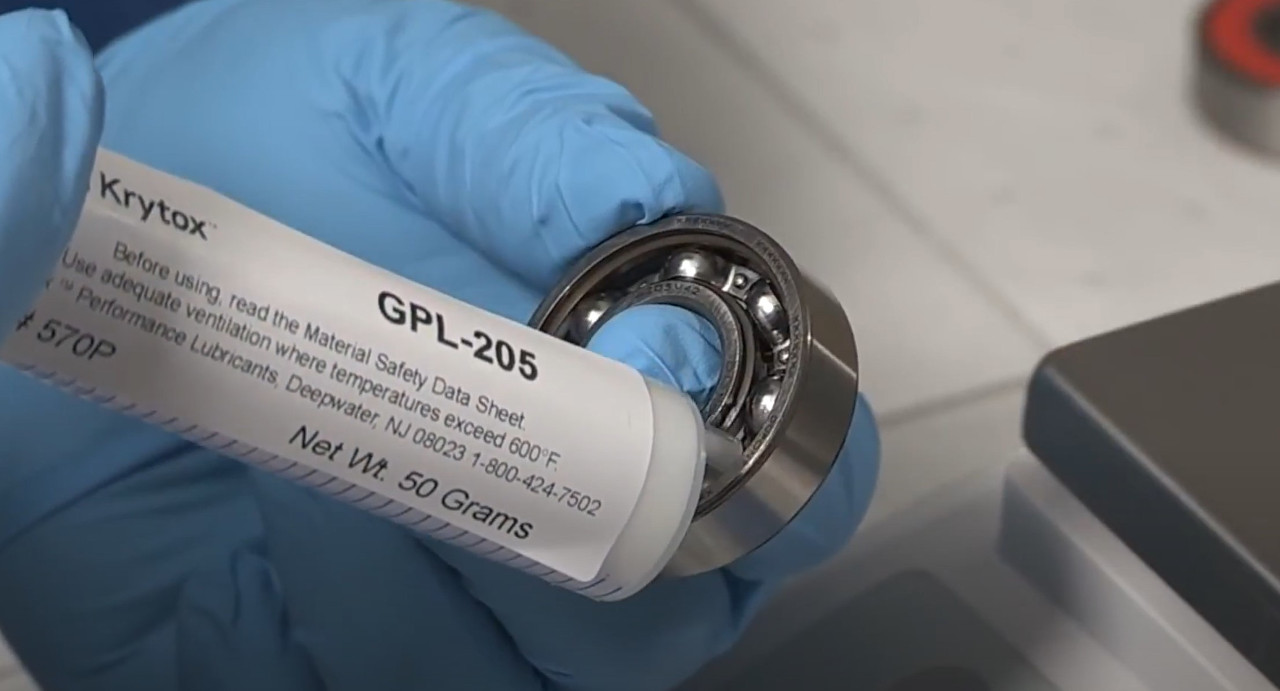
How much fat to use
It is important to use a sufficient amount of grease in the bearings, as too little grease could lead to premature failure while too much grease could lead to overheating of the bearings.
The application and operating speed of the bearing determine the amount of grease applied, as described below.
Conveyors and low-speed machines with DN values below 50,000 use 60-75% of the free volume.
Medium speed applications with DN values between 50,000-200,000 use 35-50% of the free volume.
High-speed applications, uses 25-35% of the free volume.
Extreme speed applications, uses 10-15% of the free volume.
Remember to consider the high density of Krytox™ fat when determining the amount of filler by weight. The specific gravity of Krytox™ fat is about 2.0 mg/L.
Contact the bearing manufacturer for the capacity of the specific bearing you are using.
Also, be sure to use a dedicated grease gun. Grease nipples need to be changed to prevent other types of grease from accidentally getting inside the bearing.
Velocity factor (DN)
The speed factor (DN) of a bearing determines the speed range available for grease within a bearing. The DN value is calculated by multiplying the inner track i.d. (in millimeters) by the rpm. Think DN values of 100,000-400,000 and higher have been achieved at temperatures between 204°C and 260°C using Krytox™ greases. At these speeds special break-in runs may be needed to further distribute the grease to prevent overheating.
The speed factor is ultimately a measure of the internal friction of the lubricant, dependent on the type of bearing, its load, speed, precision, and lubrication system, and is a key factor in determining how to clean and grease bearings