Huntsman Araldite® Industrial Adhesives: From Design to Application
Industrial adhesives are successfully used in demanding applications, including aerospace, automotive, wind, sports, rail, construction, and medical equipment. Designers in almost every industry say that bonding with the
Huntsman Araldite® adhesives
can provide aneffective solution against the new design challenges of new production methods .
Mascherpa is the exclusive distributor of Huntsman Araldite® industrial adhesives, which are efficient and easy to use. It is essential to strictly follow the instructions provided by the manufacturers themselves to achieve the best performance.
Key instructions for successful bonding:
- Resin and hardener components should be carefully measured and thoroughly mixed together
- Joint surfaces should be degreased and, if necessary, pretreated
- The minimum curing temperature and curing time must be met
- Fasteners should be used to prevent the bonding surfaces from moving during the curing process
- Although only light pressure is needed, it should be applied as evenly as possible over the entire bonding area. Excessive pressure can leave the joint with an insufficient amount of product
Computer simulations for improved bonding performance
At Mascherpa, we understand that in order to get the best performance from an adhesive bond, it is important to pay special attention to the design phase, in which adhesive application and assembly methods are considered. These characteristics, together with curing conditions, determine the choice of industrial adhesive to be used.
Computer simulation is an increasingly used technique for designing adhesive structural joints. The simulation gives engineers a well-detailed estimate of the deformation and strength of bonded parts.
For example, templates are available for the Huntsman Araldite® range of industrial adhesives composed according to the materials used in the laboratory.
The models provide a wealth of information on the physical, mechanical and thermal behavior of our products, including detailed experimental data of the mechanical properties of the adhesive (tensile and fracture), adhesion properties (lap shear, peel) and curing phenomena (glass transition temperature shrinkage, density, hardness). Using Araldite® models allows engineers to obtain truthful simulation regarding adhesive joints, reducing the number of physical tests required for the design process.
The advantages of using Araldite® industrial adhesives: stiffening effect
Bonding with Araldite® industrial adhesives, such as withAraldite® 2012 adhesive, can offer not only simplified design, but also reduced stress, increased stiffness and improved appearance.
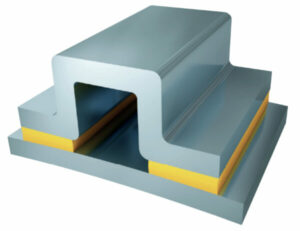
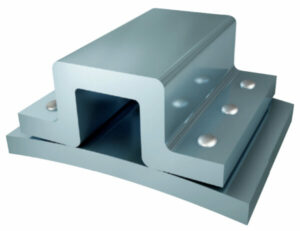
Stiffening effect with bonding:
The diagram shows how a joint can be designed to take advantage of the stiffening effect of bonding. The adhesive in this way forms a continuous bond between the surfaces.
Stiffening effect with riveting:
Rivets and spot welds only secure surfaces in specific areas. Bonded structures are consequently much stiffer, and the load can be increased (up to 30 to 100 percent) before deformation occurs.
Here are some qualities of industrial adhesives in the applications shown:
- Continuous bond: stress is evenly distributed over the entire bond area when a load is applied, and is highly concentrated in a few areas when rivet welding is used. Bonded assemblies therefore generally have a longer service life under load.
- Improved appearance: bonding gives the parts a smooth and homogeneous appearance. There are no protruding fasteners, such as screws or rivets, and no signs of spot welding.
- Stiffer structures: the continuity of a bonded assembly produces stiffer structures. Alternatively, if greater rigidity is not needed, the weight of the structure can be decreased.
- Complex assemblies: complex assemblies often cannot be implemented with any other fastening technique. Composite sandwich panels are a typical example.
The advantages of using industrial adhesives: stress distribution
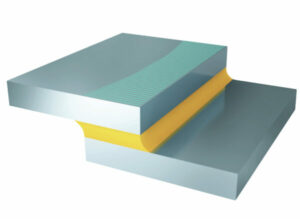
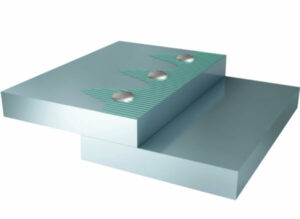
Stress distribution in bonded loaded joints:
The glued joint shown here is uniformly stressed. In this case, a welded joint would also show good stress distribution, but the heat of welding can reduce the properties of the metal near the weld, reducing the overall strength
Stress distribution in rivet-loaded joints:
The riveted joint is highly stressed near the rivets. Failure tends to start in these areas of maximum stress. A similar stress distribution occurs with spot welds and bolts.
Huntsman Araldite® industrial adhesives can be used in a variety of application conditions, for example, in situations such as:
- Dissimilar materials: adhesives can join together materials of different composition, stiffness, thickness and coefficients of thermal expansion.
- Heat-sensitive materials: bonding does not require high temperatures, making it particularly suitable for bonding heat-sensitive materials that are prone to distortion and subject to changes in their properties.
- Reduced corrosion: the continuous adhesive bond forms a seal. The joint is consequently leak-proof and less prone to corrosion.
- Electrical conductivity: some Araldite® adhesives are specifically formulated to offer high electrical conductivity.
- Dielectric insulation: the adhesive bond can form an electrically insulating barrier between components
- Vibration damping: adhesive bonds have good damping properties that can be useful in reducing sound transmission or vibration.
- Reduced stress concentration: A bonded joint can lead to an inherently safer structure because the reduced stress concentration makes it less likely to fail.