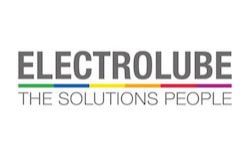
THE ROLE OF ELECTRONIC PROTECTION IN RENEWABLE ENERGY SOURCES
Renewable energy is defined as that energy obtained from renewable resources that are naturally replenished on a human time scale. These are expected to account for more than 50 percent of global electricity production by 2035. In other words, it is energy obtained from non-depletable resources in the Earth rather than from finite and finite sources such as fossil fuels.
According to * Allied Market Research, the renewable energy market is expected to grow to over $1.5 trillion by 2025 with biomass representing the main form of energy within this market. Looking at the possible applications in more detail, however, it is possible to see that the various forms of renewable energy may have an even wider potential use.
HYDROPOWER AND MARINE ENERGY
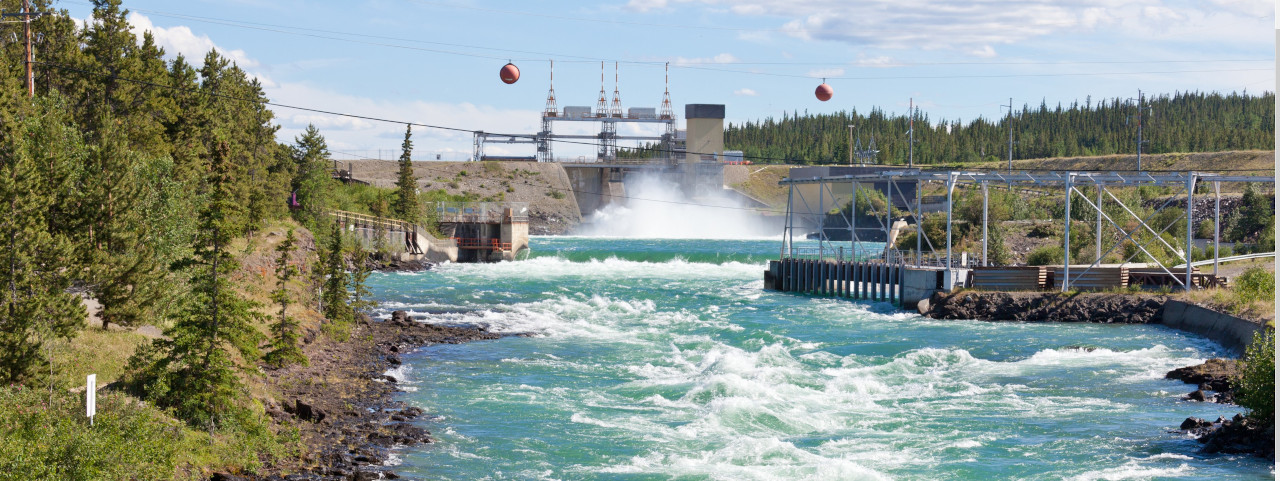
Our discussion begins with water, which is universally regarded as the most traditional of renewable energy sources. Hydropower, tidal energy and current energy are all based on exploiting the hydrokinetic potential generated by the movement of water masses. It is a type of energy that is sustainable and has a low carbon footprint. The energy generated by the fall or rapid movement of water is typically known as hydropower and has been used for centuries in a variety of mechanical applications. In the late 19th century, hydropower was first used for electricity generation and has continued to develop as an important renewable energy source ever since. Hydropower is produced by passing water through turbine generators consisting of a series of electronic parts: alternators, inverters, control panels and power switches. This type of technology is incredibly versatile, and examples of its application can be seen all over the world, one of the most famous being the Hoover Dam in the United States. This type of technology can also be used in rivers and not only in conditions where water falls vertically. Although carbon emissions from these plants may be low, they are not totally free of impact on the environment. Indeed, it is important to consider additional factors such as protection of fish from turbines, appropriate land use, and assessment of surrounding wildlife when developing new sites for hydropower use.
The two remaining renewable energy sources using the hydrokinetic potential of water look similar but are actually very different. Tidal motion is continuous and constant, so energy is produced in predictable patterns through tidal flow generators located in suitable coastal areas. In contrast, energy from sea currents is generated directly at sea, operates in a much less predictable manner, but generally plays a minor role in the overall tally of renewable energy sources. In Italy, the Strait of Messina is one of the most interesting sites for the exploitation of this type of energy. Despite the differences between the various methods of energy utilization, all types of hydropower plants require electronic components, both to ensure the conversion of kinetic energy into electricity and to monitor the efficiency of the plant through the observation of external and internal environmental conditions. And it is precisely in these demanding electronic applications that Electrolube products make the difference. Electrolube’s protective compounds, such as encapsulating resins and conformal coatings, enable the application to operate efficiently and sustainably even i under harsh environmental conditions. Devices such as sensors and data collectors are important for gathering information both inside and outside the plant. These provide details such as water depth and wave acceleration, and in this way allow the systems to be better adjusted and achieve better results. Water protection for these devices is just one example in which an encapsulating resin can make these measurements possible and effective, greatly reducing maintenance time and human interaction in data collection.
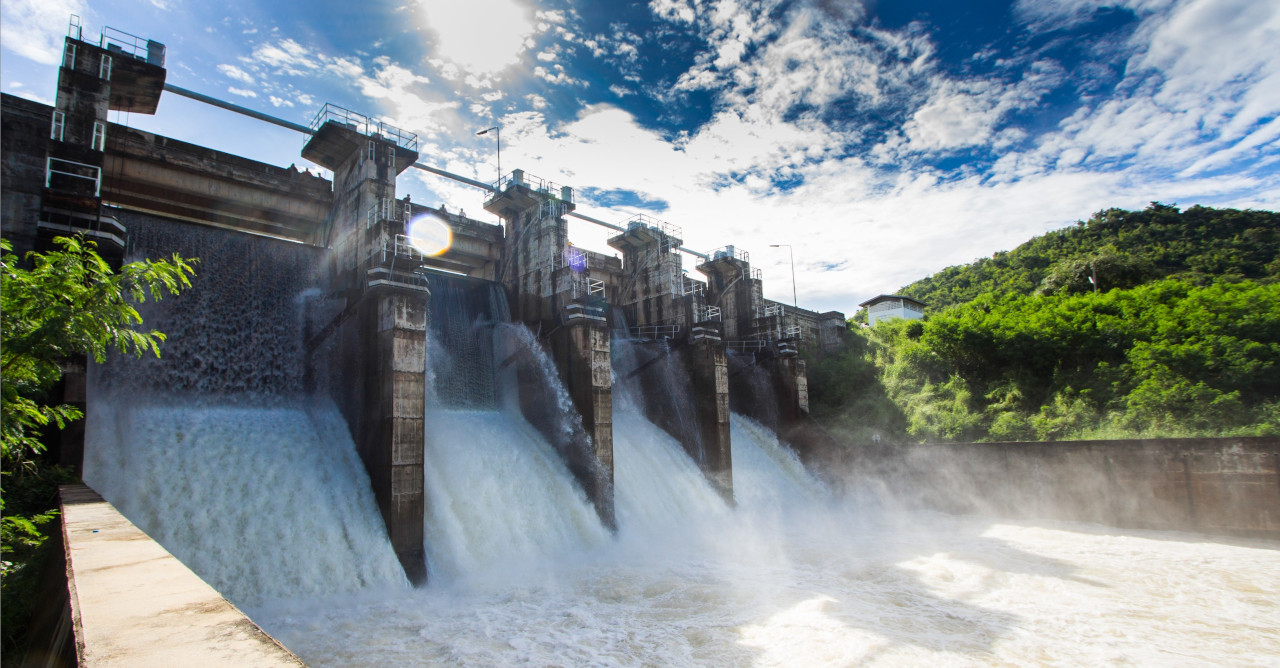
SOLAR ENERGY.
Solar energy is produced by capturing energy from sunlight and converting it into heat, electricity or hot water. Solar cells produce direct current electricity from sunlight through technology known as photovoltaics. However, the applied technology does not stop at the solar cell alone. Inverters are used to convert direct current to alternating current so that the solar panel can power electronic appliances in your home. There are also capacitors that are used to temporarily store electricity where needed. In the case of off-grid applications that are therefore not connected to main power grids, batteries may be needed to store energy for wider and greater use. In such cases, these electronic devices will require protection from the external environment, but they will also need to be able to operate at higher temperatures and offer some form of thermal dissipation because of the high operating heat. Depending on specific requirements, thermal management products can be used to help dissipate heat from devices, such as in the form of thermal fillers (Electrolube GF400). However, to provide both environmental protection and thermal dissipation, special encapsulating resins such as Electrolube’s ER2221 may be needed.
In addition to capturing and converting energy, it may be necessary to have to measure the performance of the solar panel in order to make its operation and maintenance more effective. For example, measuring the temperature of individual panels can be very important in order to manage facilities such as solar farms by ensuring more efficient use of technology. While the equipment used should be able to withstand some rather extreme weather conditions (including direct exposure to the sun, heat and other environmental elements), very often the electronic components that make up the solar equipment system can prove to be relatively small and fragile. Electrolube works directly with companies developing applications for harnessing solar energy, gaining unparalleled direct experience and new application challenges. In one customer application, a small device for displaying information about the performance and connectivity of a solar panel system required protection from the external environment. Some problems had arisen with the resins tested, where the hardness of the material had caused pressure on the LED screen, leading to failures during operation. Initially some silicone options were also tested given the low-stress requirement, but these did not achieve the same effectiveness provided by Electrolube’s UR5044, which showed great stability and low hardness over a wide temperature range. The adhesion achieved by this polyurethane resin was significantly higher than the previous silicone resins tested and thus resulted in significantly better protection.
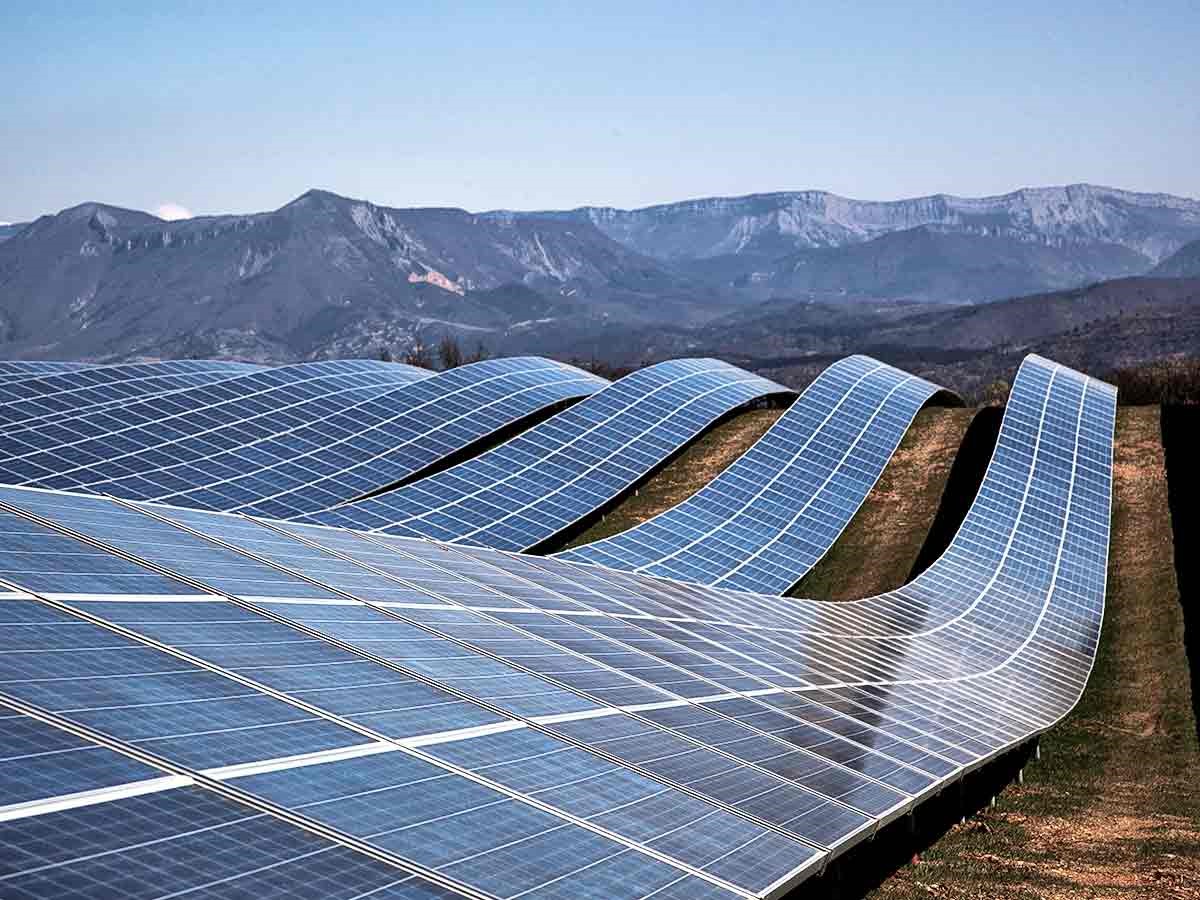
A major limitation in the performance of solar panels is the accumulation of dirt on the surface, which adversely affects the efficiency of the panel. In large systems, it can be difficult to ascertain the source of inefficiencies, so electronic devices that help monitor the condition of each panel through the use of detection sensors prove very useful. These compare the measurements in the system with those in the control reference panels, thus calculating the dirt loss index. These sensors will need both protection from the environment and the ability to operate with maximum performance. In order to achieve these goals, the choice of the most suitable protective compound is crucial. As mentioned earlier with hydropower applications, it is necessary to understand the conditions under which a given technology operates in order to enable its optimal management.In this case, measurements of solar radiation and ultraviolet and infrared light spectra are extremely important. Such data must be transmitted via GPRS or Bluetooth, and any protection compound used must not interfere with these signals. Encapsulating resins with a low dielectric constant are best suited for this type of application, such as Electrolube’s UR5118, which also offers excellent water resistance. However, in cases where the unit is well sealed and thus has an already high IP rating, it may also be possible to use a conformal coating (Electrolube AFA) to prevent the effects of condensation and minimize the weight of the device.
Every day in our cities, from decorative garden lighting, to street signs, station roofs, and bike lanes, you can now see solar panels powering electronic devices in a wide variety of applications. These have now become woven into our daily lives, and their uses are increasingly increasing and integrating with other technologies. Smart streetlights and solar benches are among the most recent examples where integration with numerous other innovative technologies, such as remote management control, wireless charging, and Wi-Fi hotspots, can be observed. All of these integrated electronic technology components need adequate protection, and with this in mind it seems clear that the chemical industry is playing a decidedly important role in directing new developments and evolutions. Right up to solar paint technology that is estimated to exponentially increase electricity production, the chemical applications in the solar industry are seemingly endless.
Although the increasing degree of reliability and efficiency in renewable energy sources is highly dependent on the equipment used for production, which is characterized by a significant amount of moving parts, it is clear that electronic developments have been and will be critical to the development and integration of these sources into our daily lives. Over time, power generation is likely to become even more automated and increasingly intertwined with information technology. Efficiency and reliability will further increase as the level of artificial intelligence increases. Thermal management materials, conformal coatings and encapsulating resins play a central role in the protection, reliability and durability of devices used in renewable energy production.